In the dawn of a new country
We are in Madrid, it is the year 1974. Spain is still under the dictatorship of Francisco Franco who is now very old and ill. In a matter of weeks he’ll pass away and will give the country the chance to re-establish itself as a democratic territory.
Banco Coca is an important financial entity in Spain at this time and they contact Rafael de la Hoz Arderius and Gerardo Olivares to design their new headquarters. The plot sits at Plaza Castelar, adjacent to Paseo de la Castellana which is the most prestigious avenue in the Spanish Capital.
De la Hoz is a second generation architect, and one with a special pedigree. He’s been studying in the USA for a year and at the very young age of thirty two he’s recognised with the National Award of Architecture for his project “Colegio Mayor Aquinas”. Probably his year at the Massachusetts Institute of Technology (MIT) is what influences and directs him towards a technological approach to architecture, always aware of the latest innovations and construction techniques in the discipline.
Rafael de la Hoz was also the architect responsible for drawing up the “Normas Tecnológicas de la Edificación” – NTE) , which is the document that regulated and gave recommendations for all aspects of the discipline of architecture such as design, calculations, construction, control, valuation and maintenance.
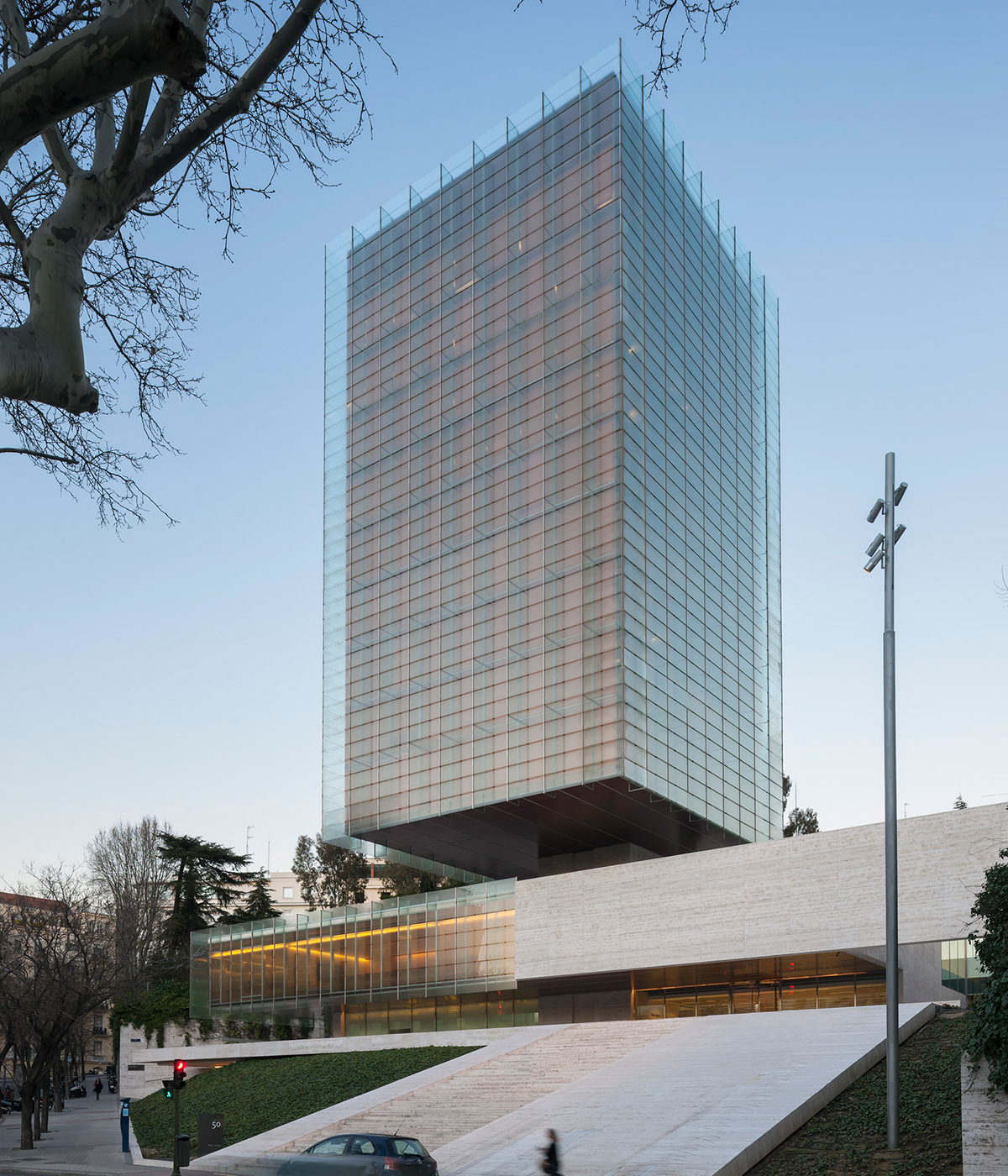
Castelar Building Architects: Rafael de la Hoz Arderius and Gerardo Olivares. Access to the building from Paseo de la Castellana, the glass and steel lantern appears as a floating object over the travertine podium.
Photography by Duccio Malagamba
The persistence of the architects
Like most remarkable architecture achievements, the process to get the Castelar Building completed was long and difficult. The project took 12 years to be built. The concept design stage started in 1974 and it wasn’t until 1986 when the building was finished. During this time Banco Coca went through financial difficulties in the midst of the Spanish Banking system crisis (1977-85) and the institution ended up being acquired by the Banco Español de Credito (Banesto) in 1978.
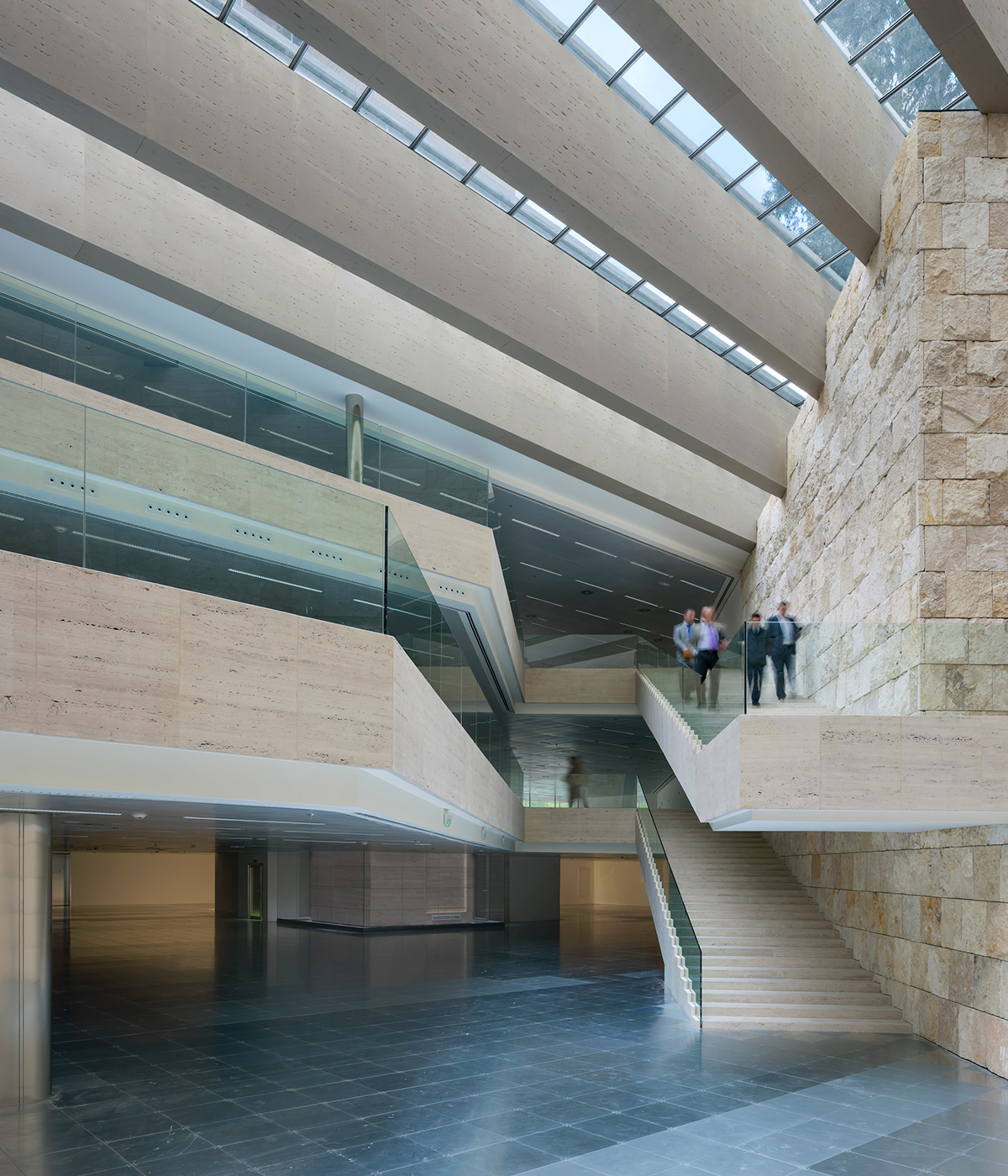
Castelar Building. Architects: Rafael de la Hoz Arderius and Gerardo Olivares. Internal atrium view. Rafael del Hoz Castanys, son of the architect, undertook the renovation works in 2010. Brickwork walls inside the atrium were substituted by rough stone blocks in line with the original vision of the project.
Photography by Duccio Malagamba
When Banesto took over the direction of Banco Coca, the building was still under construction and the new owners were not confident of the value of the investment in order to finish the building. De la Hoz and Olivares fought hard to keep the vision alive and convinced the new owners that the building would be more valuable once finished if they wanted to sell it. The architects knew of the unique opportunity that they had in their hands to bring to real life a project that was pushing the boundaries of architectural language and construction technology in a way that it had not been seen before in the country.
The Concept : Minimal art brought to urban scale
The decade of the 60s had seen the rise of a new stream of art in the United States called Minimalism. Artists such as Carl Andre, Donald Judd or Sol Lewitt had achieved international recognition with their work . The Museum of Modern Art described it in this way: “Relying on industrial technologies and rational processes, Minimalist artists challenged traditional notions of craftsmanship, using commercial materials such as fiberglass and aluminum, and often employing mathematical systems to determine the composition of their works.”
I see the Edificio Castelar as a continuation of this artistic ideology that still influences architects around the world today. De la Hoz and Olivares pushed for a proposal that defied the convention and the laws of gravity, an expensive prototype with a number of innovative solutions in every aspect of architecture design: space, structure, construction, cladding design or treatment of light.
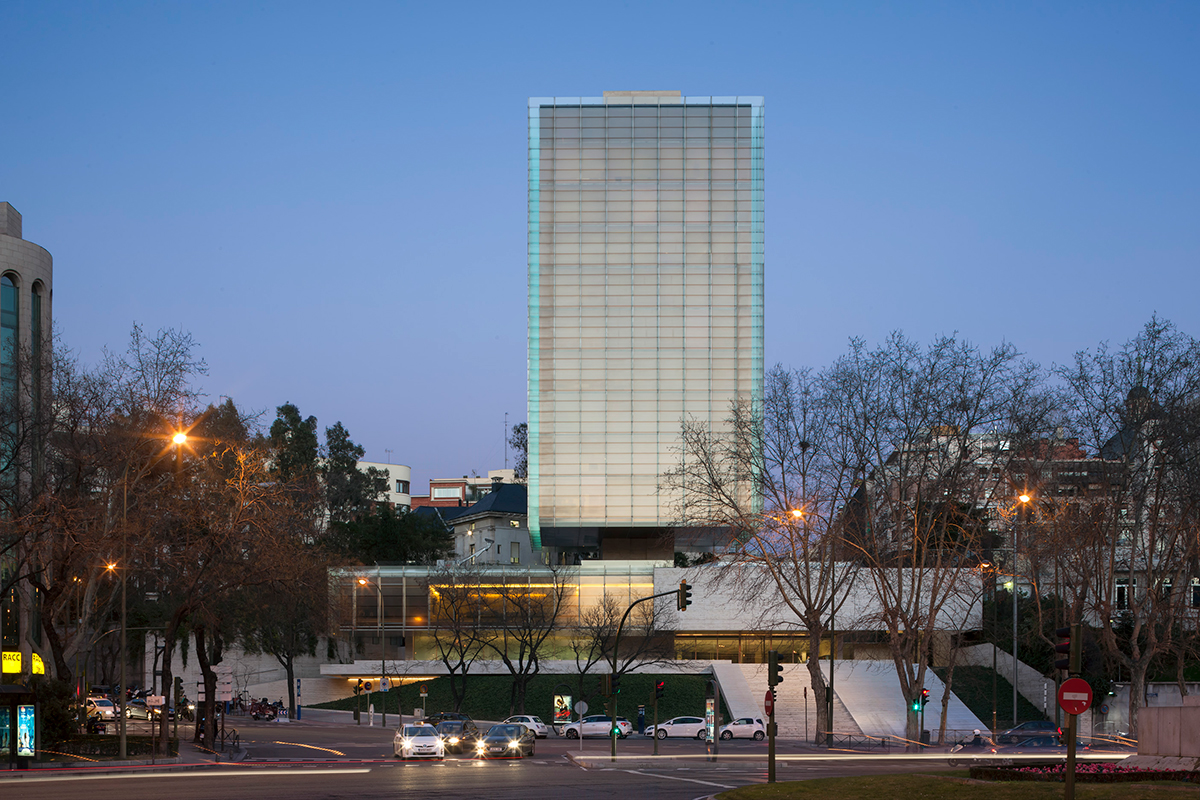
Castelar Building. Architects: Rafael de la Hoz Arderius and Gerardo Olivares. Front elevation at sunset time from Paseo de la Castellana, the building resembles a minimalist sculpture. The abstract glass volume presents as a pure geometric form devoid of scale on which we hardly appreciate the different floors contained.
Photography by Duccio Malagamba
Taking risks and making the difference with a bold structural concept
The architects chose to respect the sloped nature of the site with a building that hovered over the terrain. A kind of abstract glass lantern floating in the air several meters above a travertine podium. And they wanted to make it float. They placed an L-shaped concrete core sitting at the back of the plot. A vertical and hollow mega column that contained stairs and lifts and a horizontal arm at the top from which all of the floors, built with a perpendicular grid of steel beams, would hang from. This unusual and bold solution allowed them to have the entire floor plate free of columns and visual obstacles.
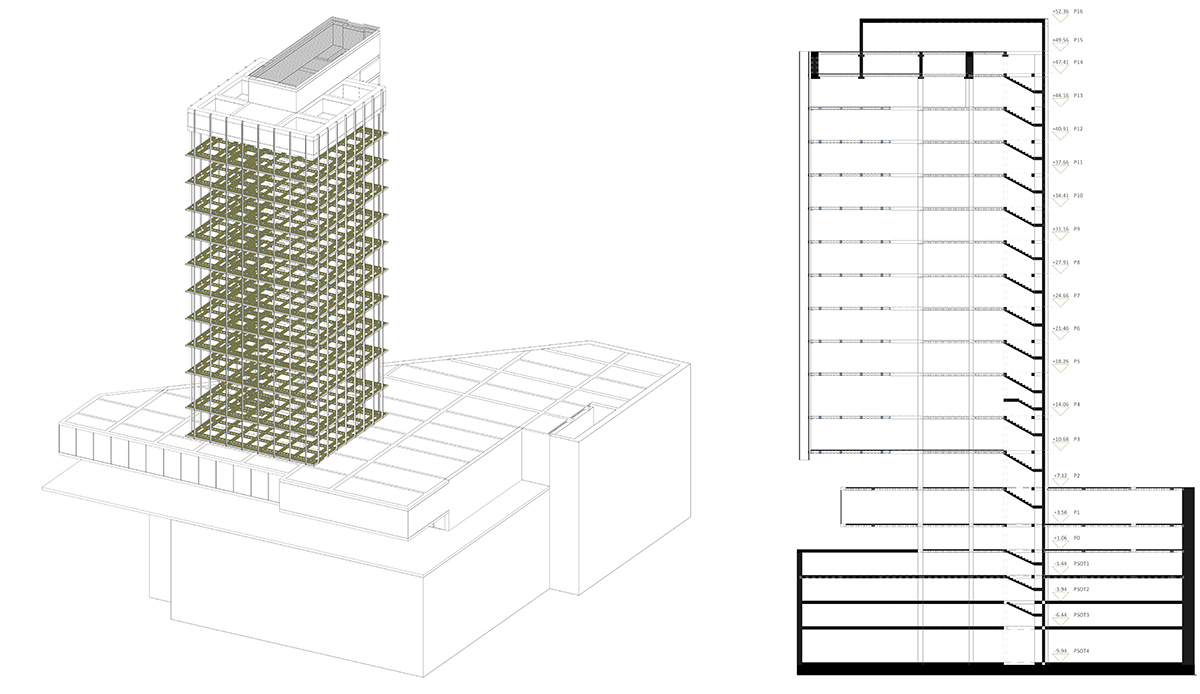
Castelar Building. Architects: Rafael de la Hoz Arderius and Gerardo Olivares. Axonometric and Section diagrams explaining the structural principles of the building. A 90 degree grid of steel beams form the floor slabs that hang from the off-centered concrete core.
Drawing by Paula Varela
De la Hoz and Olivares committed themselves to bring to their country the latest architectural tendencies and became an active part in defining what avantgarde meant at the time. They joined other architects’ efforts, like the british Richard Rogers and Norman Foster, in proposing similar approaches by placing the vertical cores at the perimeter of the floor plates so these could be as flexible as possible. Remember for example the Lloyds Building in London or the later HSBC Headquarters in Hong Kong.
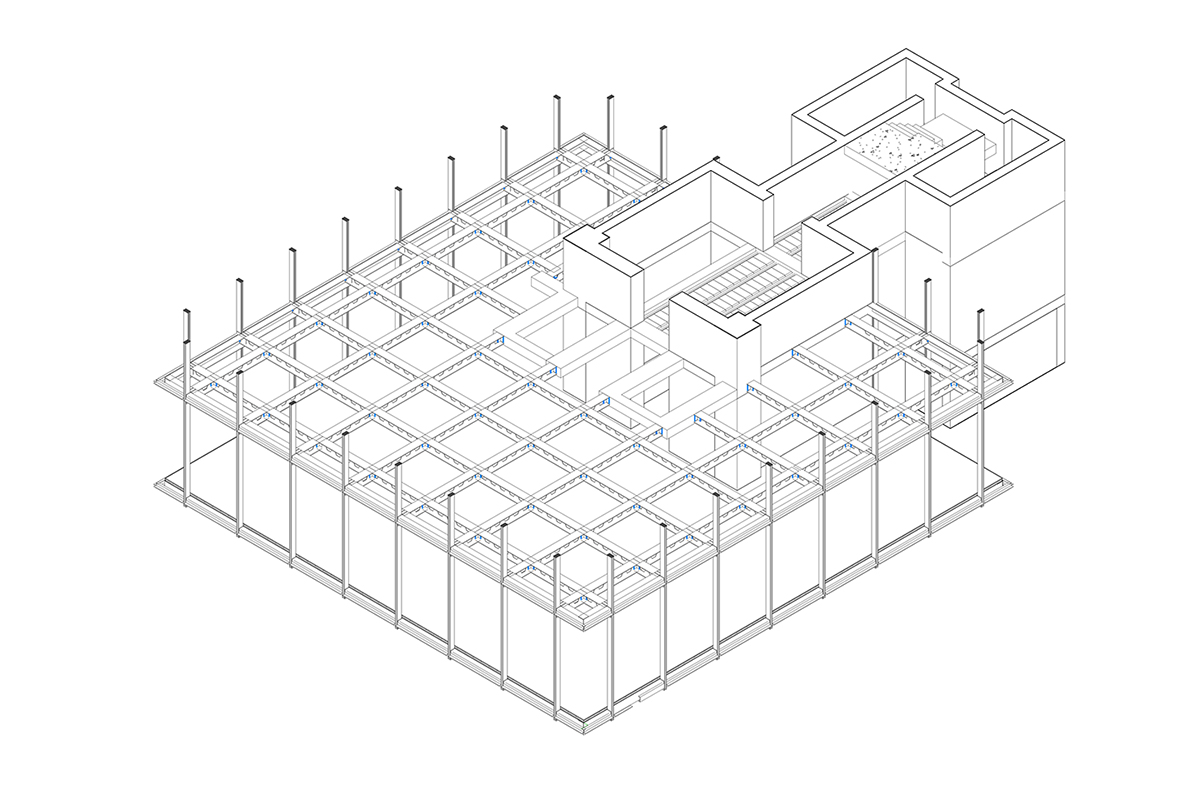
Castelar Building. Architects: Rafael de la Hoz Arderius and Gerardo Olivares. Axonometric view of an isolated floor, the concrete core is split in two vertical shafts separated by a corridor, this way the core increases its resistance to tipping forward due to the off centered weight of the floorplates. The steel grid is attached to the core and hangs from the perimetral columns supported at the top floor.
Drawing by Paula Varela
They took the risk to propose something new and exciting. The son of the architect, the also well-known Rafael de la Hoz Castany, happily remembers how his father would call him every time a storm hit Madrid, asking if the building was still standing even years after its completion.
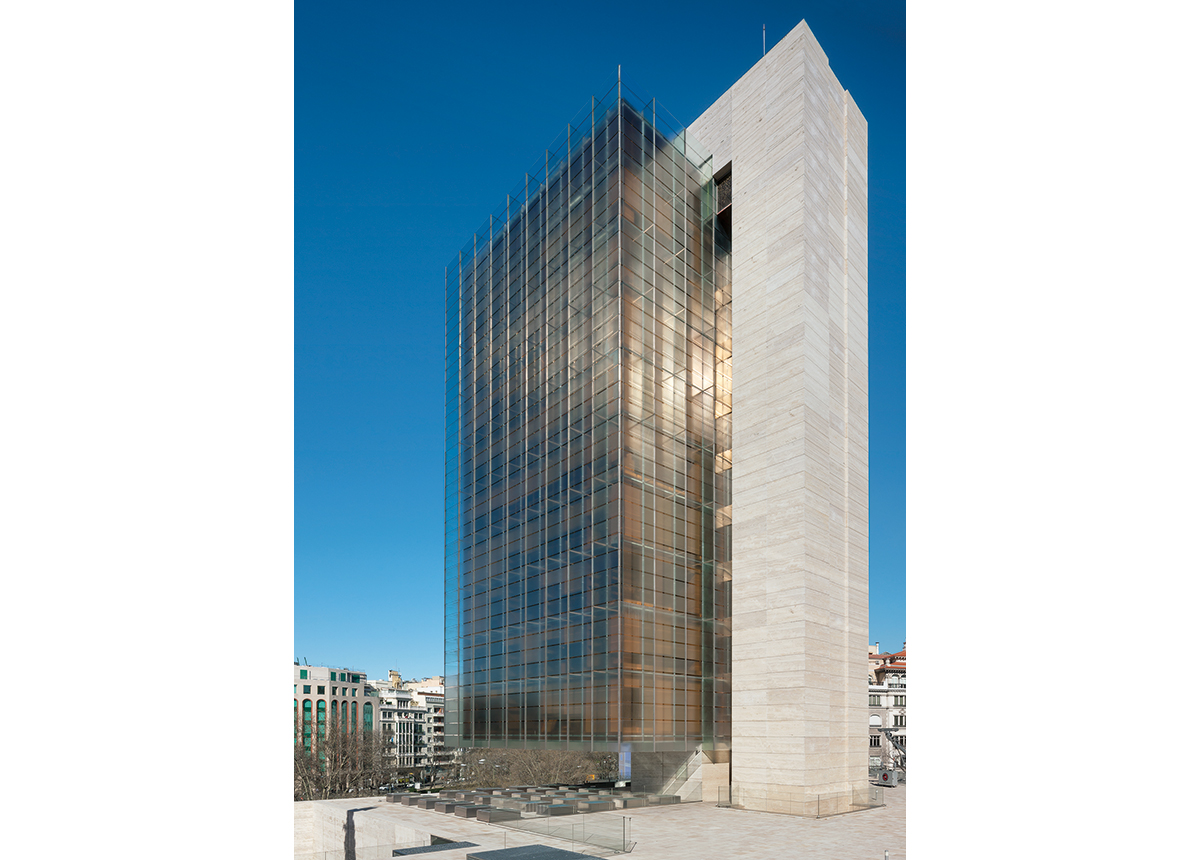
Castelar Building. Architects: Rafael de la Hoz Arderius and Gerardo Olivares. The office space volume cladded in a double skin of glass hangs from the off-centered, travertine-cladded, concrete core at the back.
Photography by Duccio Malagamba
Radical approach up to the level of the details
The selection of glass as the most appropriate material to represent the idea of the floating lantern presented some challenges that came as a consequence of the nature of the material itself. The glass is a fantastic material that allows us to see through it but at the same time, if not resolved adequately, it can also allow the heat to penetrate the building, creating a greenhouse effect in the internal space. Spain is a country where the amount of sunny days surpasses those of the northern countries where this ethereal architecture of glass emerged, therefore a different strategy had to be implemented.
The architects designed a double skin of glass that wraps around the floating volume. The inner layer of glass encloses the space and protects it from the environment, allowing the light to come through while keeping the rain and the wind outside. The second glass becomes a rainscreen, offering a first layer of protection and creating a buffer zone in between the glass layers that, since it’s open at the top and the bottom, lets the warm air escape and functions as a fantastic layer of transparent thermal insulation. The light goes through and the heat stays outside.
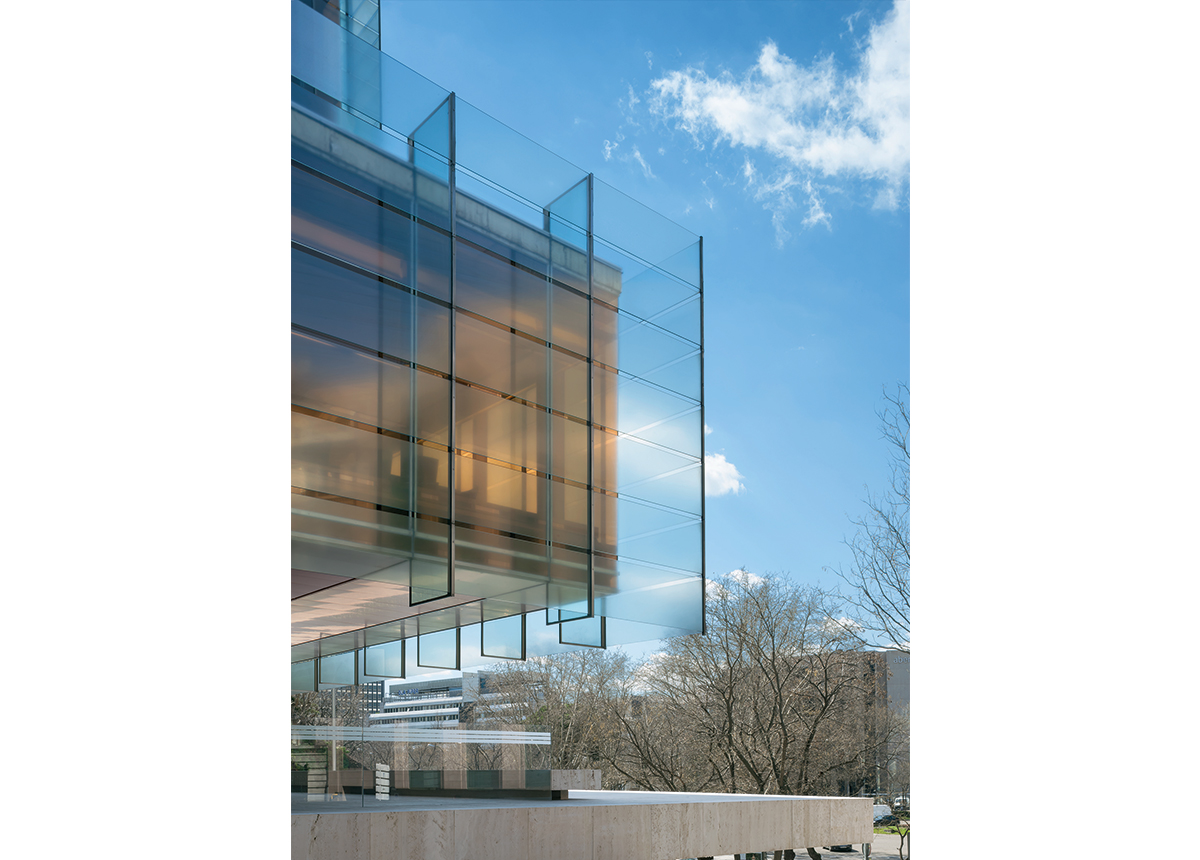
Castelar Building. Architects: Rafael de la Hoz Arderius and Gerardo Olivares. Detailed image of the double glass skin construction. The outer layer of glass hangs in the air and it is fixed back to the building by means of a series of glass fins specially designed for this building.
Photograph by Duccio Malagamba
In order to be true to the original idea of the floating volume, De la Hoz and Olivares designed a system of cables and glass fins that connected the outer layer of glass to the internal one. This was innovation right through to a detailed level.
Pushing the boundaries of technology means having to spend time and resources resolving problems that have not appeared before. Edificio Castelar was conceived as a prototype, one of a kind that came at an expensive cost. Time has passed and the building not only still stands proud in the golden mile of business in Madrid but its value has increased since then proving that design and architecture adds value to the capitalist equation.
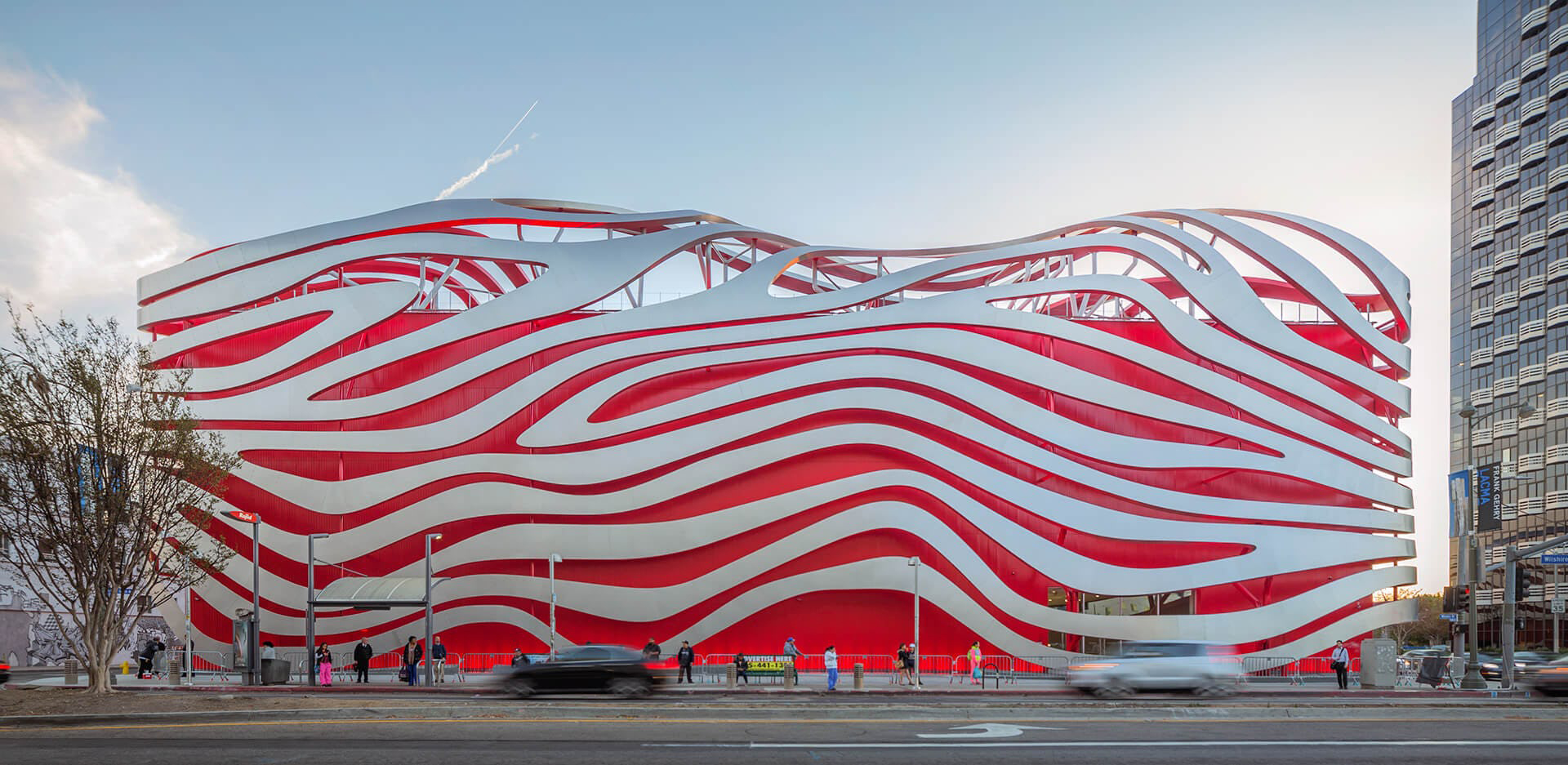
With its characteristic curving stainless-steel ribbons the exterior of the Petersen Museum re-interprets the ‘Googie’ architectural style influenced by car culture and the space age.
Photography by Tex Jernigan
Founded on June 11th 1994, by magazine publisher and car aficionado Robert E. Petersen, the $40-million Petersen Automotive Museum is owned and operated by the Petersen Automotive Museum Foundation. The museum was originally located within the Natural History Museum of Los Angeles County and later moved to a historic department store designed by Welton Becket, a well-known contemporary LA architect who died in 1969.
Six years after the department store closed in 1986, Robert Petersen selected the largely windowless site as an ideal space for his museum—allowing artifacts to be displayed without harmful exposure to direct sunlight.
The museum, opened in 1994, showcases championship-winning race cars, art cars, notable motorcycles, vehicles from Hollywood films, and other memorable vehicles. Pieces on view include concept cars from the 1950s and 1960s, the Batmobile from the Batman comics, the Jaguar XKSS formerly owned by Steve McQueen, a 1964 Aston Martin DB5 driven by James Bond in the film Goldfinger and the red Ferrari that Magnum PI drove in the 1980s TV series.
The Miracle Mile’s skyline was forever changed when, in 2015, a 13-month, $125 million renovation project was launched to renovate the nearly two-decade-old museum. The building’s façade was redesigned by the architectural firm Kohn Pedersen Fox (KPF) and features a dynamic wavy steel and aluminum façade. The main inspiration for the new exterior was the movement of a car, specifically the airflow over the body of the car. KPF decided that the new building would reflect the movement of air in an air tunnel over the body of a moving car. New “ribbons” made out of angel hair stainless steel on the front and top, and red-painted aluminum on the back and bottom, flow over and wrap the building. Acting as beams that support their own weight, these evoke the feeling of speed and movement, sitting atop the existing structural system much like the body of a car mounts to its frame. At night, the color and forms are lit up from within to accentuate the steel sculpture and act as a beacon on The Miracle Mile.
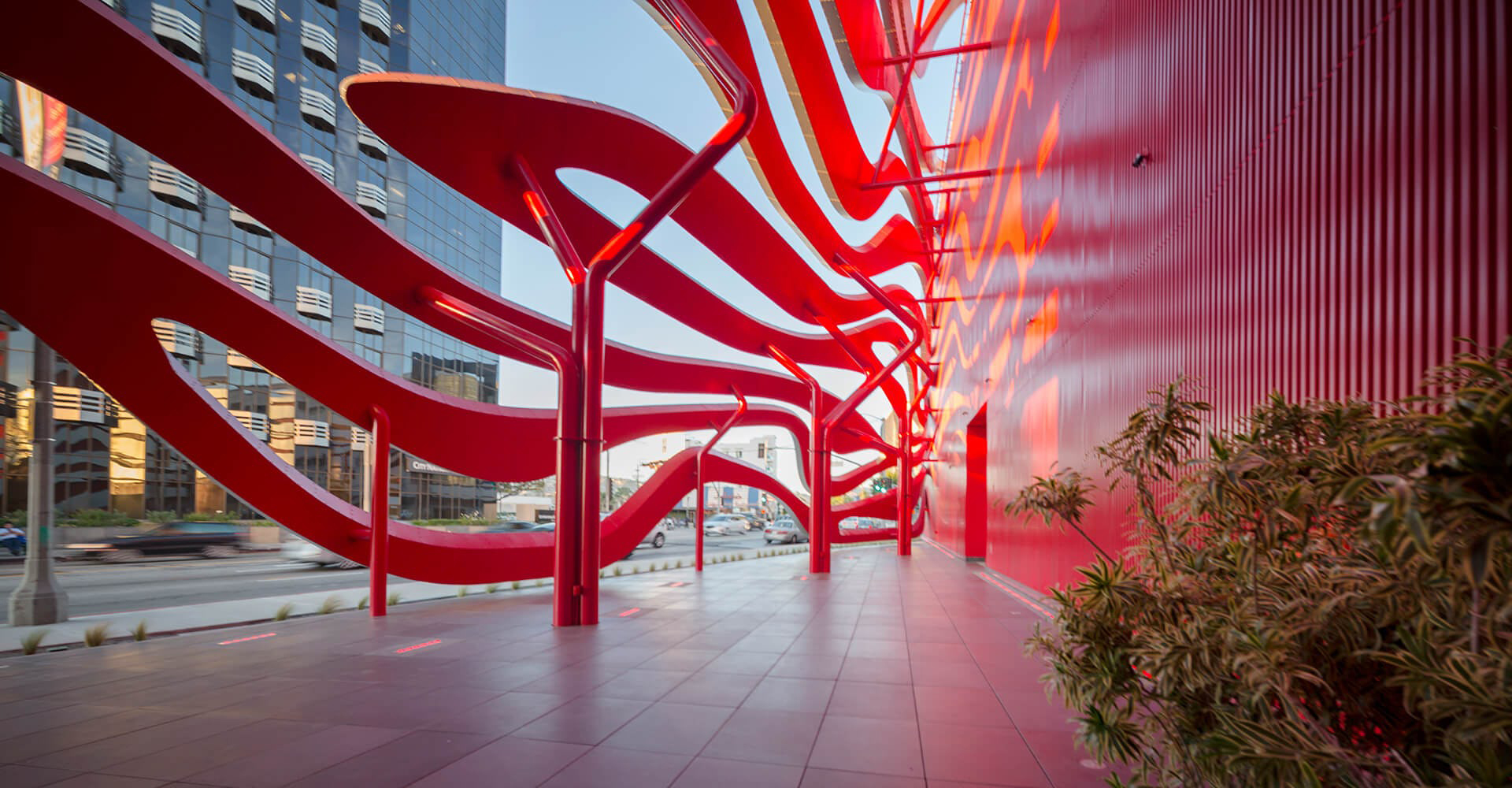
View from ground level showing the play on light between the dual steel ribbons and the red-painted corrugated aluminum rain-screen which acts as a backdrop. Each ribbon curve combines front and bottom surfaces in brushed stainless steel, while the back and top surfaces are made of textured aluminium coated with “hot-rod red” paint. The Petersen Museum.
Photography by Tex Jernigan
Los Angeles is a city that was brought to life by the automobile. The idea of Los Angeles architecture invokes thoughts of the mid-century modern movement led by architects such as John Lautner, and Wayne McAllister. This modern and space-age architecture, known as “Googie”, is characterized by upswept roofs, curvaceous shapes, and bold use of glass, steel, and neon. Googie architecture was a type of futurist movement influenced by car culture, jets, the Space Age, and the Atomic Age. It originated in Southern California with the Streamline Moderne architecture of the 1930s and was popular nationwide from roughly 1945 to the early 1970s.
The existing building, purchased by the Petersen Automotive Museum in 1994, was rectilinear and fairly straightforward in form. Because of its box-like form with no openings, it acted as a blank canvas for the design team. They encased the existing construction in a red-painted corrugated aluminum rain-screen system which acts as the backdrop for the 308 stainless steel structural ribbons, each uniquely designed. The bright red color of the aluminum backdrop is an obvious reference to sports cars. KPF Design Principal Trent Tesch comments “Our goal was to find a way to inject life into the building, with minimal intervention that would produce the maximum effect. The design offers an abstract veil of flowing ribbons, meant to invoke not only the spirit of the automobile but also the spirit of Los Angeles architectural culture.”
A flowing and dynamic design reminiscent of wind tunnel testing
The exterior stainless-steel exoskeleton is made up of more than 308 silvery steel ribbons assembled to form a dramatic contrast to the building’s “hot rod red” exterior. This 100-ton ribbon structure is made up of 14-gauge type 304 steel sections, 25 supports, and 140,000 custom stainless-steel screws.
All the architectural metalwork was produced by the long-established metalwork specialists A. Zahner Company. Throughout the company’s history, employees at Zahner have developed advanced metal surfaces and systems for both functional and ornamental architectural forms. ZEPPS, the Zahner-patented system for developing sculptural forms, was used to build curving stainless steel ‘ribbons’ which wrap the building, giving it a feeling of rapid motion. The result looks similar to the aerodynamic flow diagrams drawn in wind tunnel tests by automotive designers.
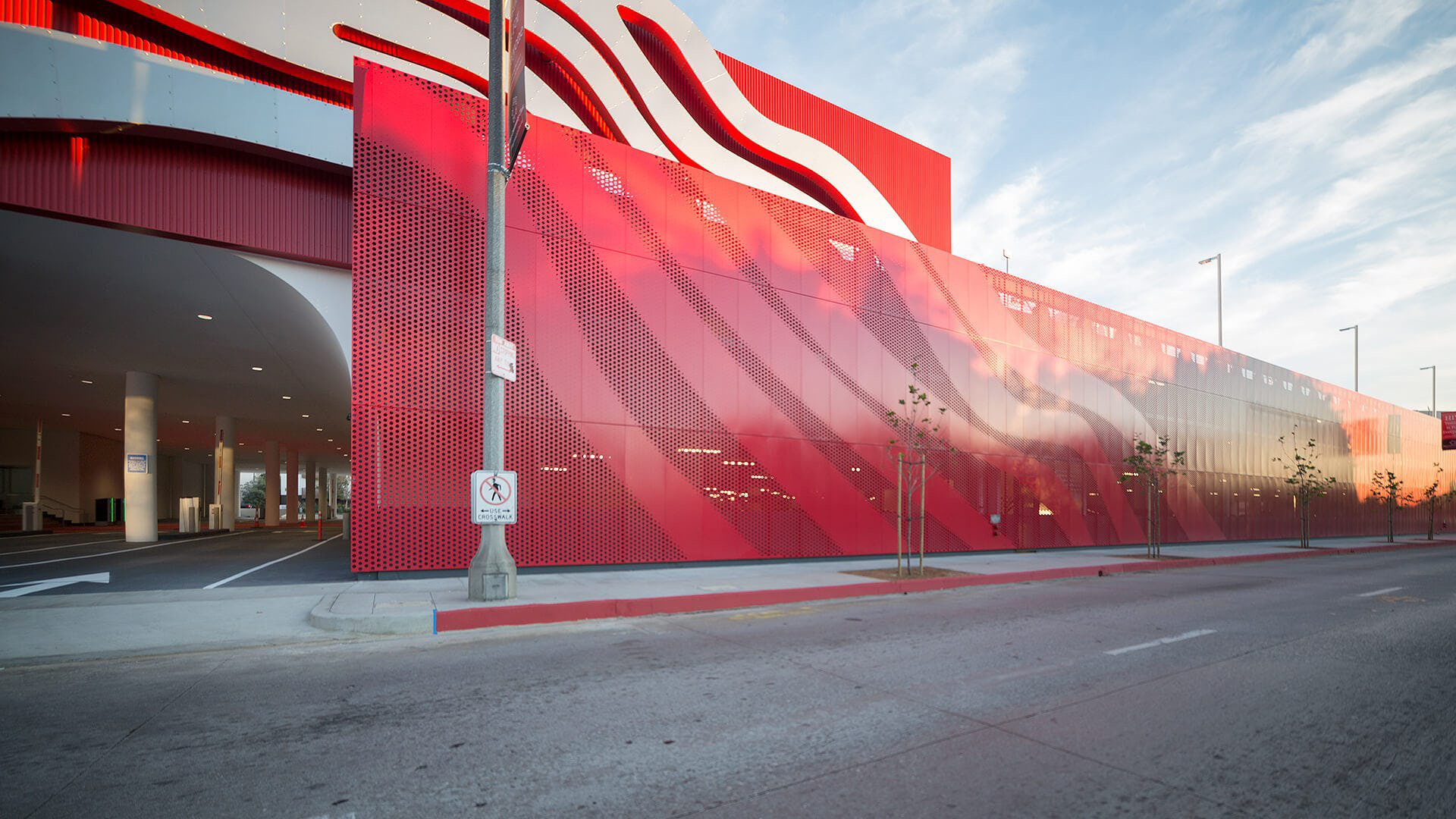
The custom perforated metal screen at the back of the building mimics the stainless ribbons to provide cohesiveness and tie in the Petersen Museum’s Parking Garage with the larger facade.
Photography by Tex Jernigan
The aluminum backdrop was completely custom and unlike any standard corrugated pattern. The corrugated profile formed an exact 90-degree angle, versus the typical sine wave that is commonly seen in corrugated metals. To accommodate for the custom nature of this design element, Zahner formed each of the corrugated panels in house, utilizing a custom die within the press brake. The front and bottom surfaces are made of stainless steel, while the back and top surfaces are made of textured aluminum coated with “hot-rod red” paint.
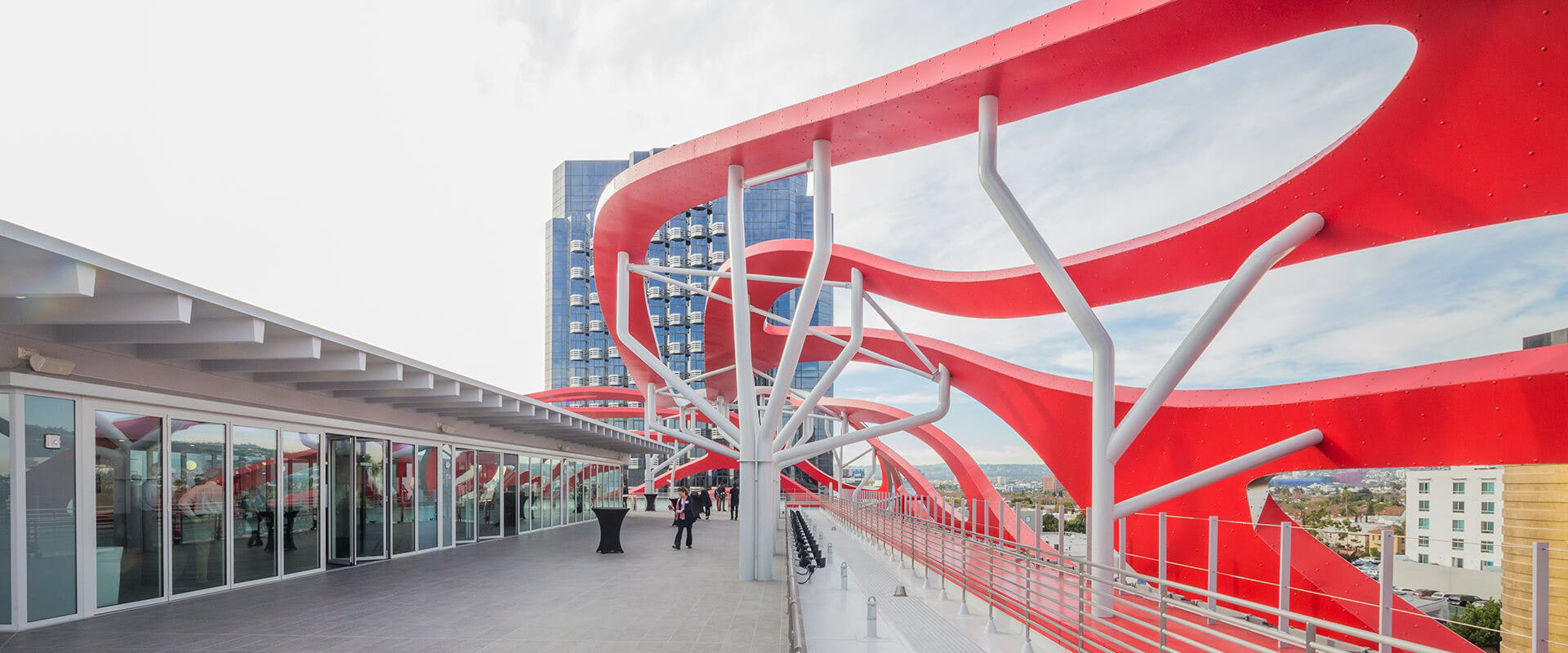
The rooftop glassed penthouse and terrace of the Petersen Museum provides a large open space of just under 10,000 sq.ft that fits up to 300 persons (standing) with panoramic views over LA and the Hollywood Hills. The cantilevered stainless steel ribbons form an aerial canopy that arches over the terrace.
Photography by Tex Jernigan
Structural steel columns shaped like hot rod manifolds
A monumental steel exoskeleton was needed to carry the loads from the red corrugated rain-screen as well as the cantilevered stainless- steel ribbons which flow over the rooftop to provide shading for a private event space as well as along the Fairfax Ave ground level. Working with the designers’ 3D models, Zahner’s team of engineers developed 25 tree-like structural columns to support the steel ribbon assemblies that weigh about 100 tons in total. The ‘tree shape’ of the structural columns was inspired by car engine hot rod manifolds. while the customized stainless-steel screws were fabricated for the project to imitate the appearance of early 20th-century automobile fasteners.
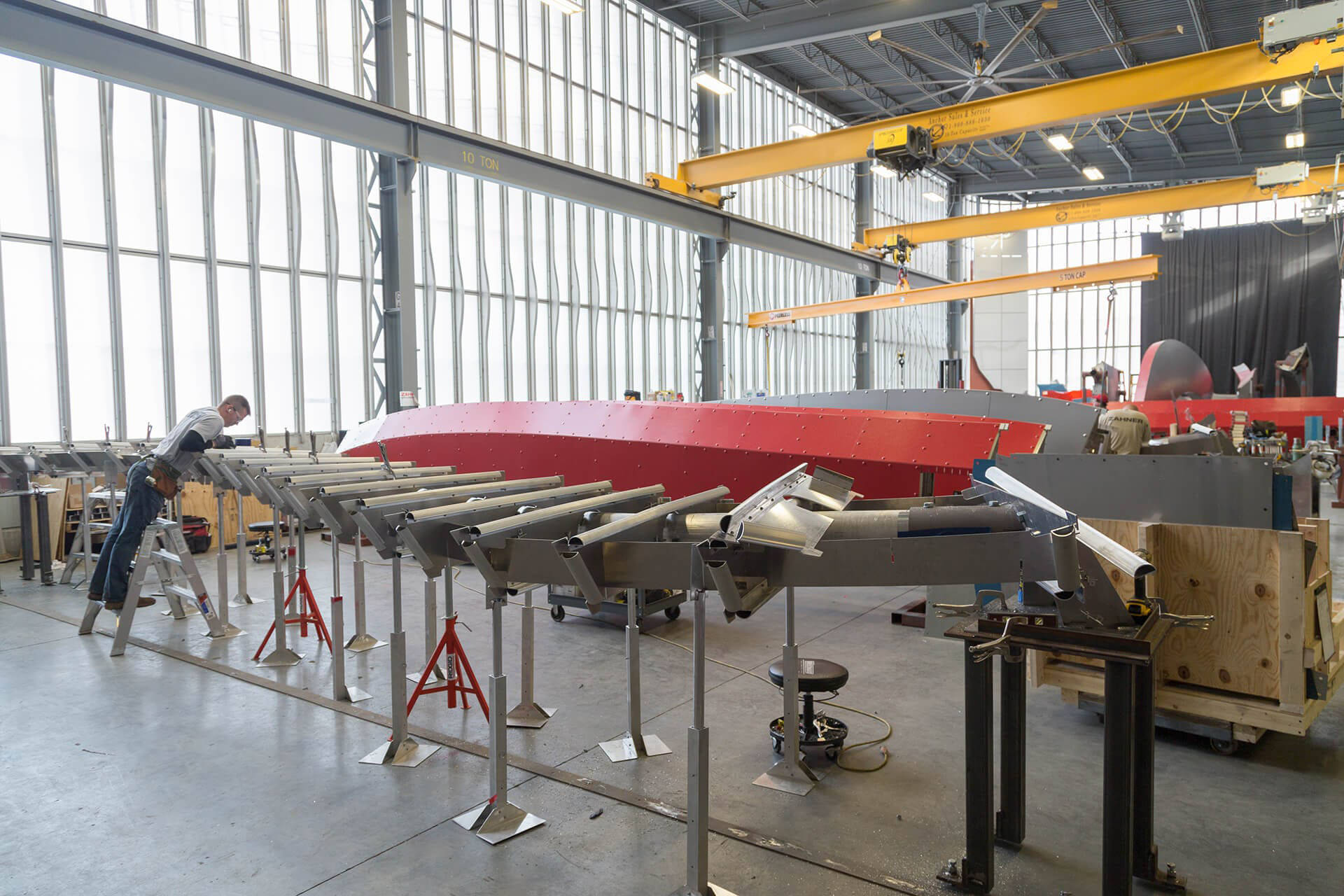
For the exterior of the Petersen Museum each curve was broken down into manageable parts for manufacturing: a series of patented aluminum structural components were pre-assembled in Zahner’s workshops before being assembled on site.
Image from A. Zahner Company
Before starting the manufacturing process the engineers examined the geometry of the architect’s 3D model. Each band required custom curved structural steel that was analyzed and made to measure according to the exact radii provided by the model. The dual curves were broken down into more manageable, structural components to allow for greater precision within the manufacturing process, and quicker job site assembly. These components were then pre-assembled at the workshop to compose the structural form before assembly. Using aluminum extrusions rather than steel allowed for a lighter load on the structure of the façade as well as more cost-efficient manufacturing.
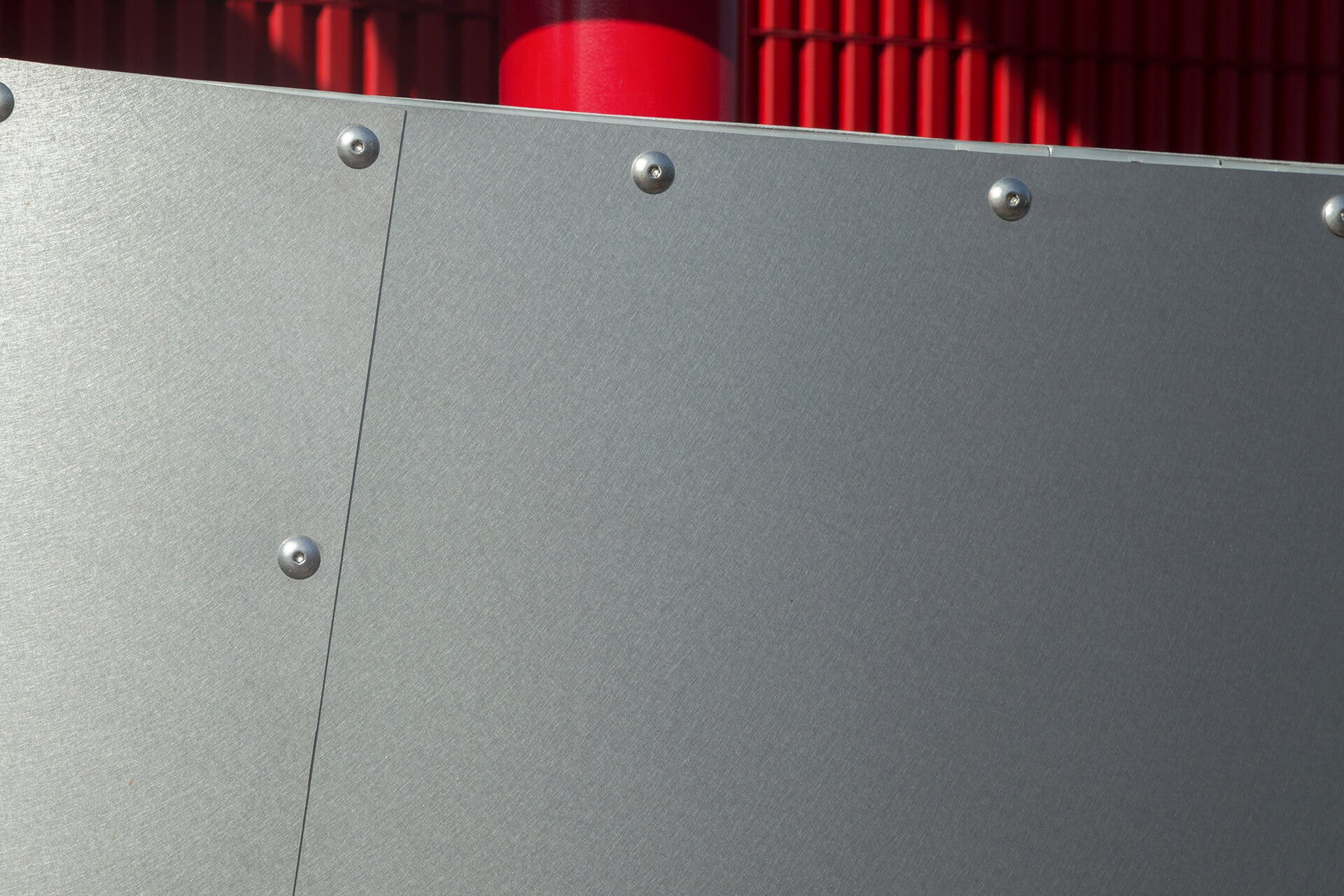
Angel Hair is a patented process to soften the glare of standard grain finishes. It uses precision-controlled machinery to etch stainless steel with a fine grain to create a smooth uniform light-diffusion metal surface.
Image from A. Zahner Company
The dual curves for the Petersen Automotive Museum were clad with Zahner’s Angel Hair Stainless Steel surface. This reflective metal sheeting was first developed for the famous Guggenheim Museum in Bilbao designed by Frank Gehry. At night the building’s flowing exterior envelope is illuminated at night by 866 individually controlled LED fixtures.
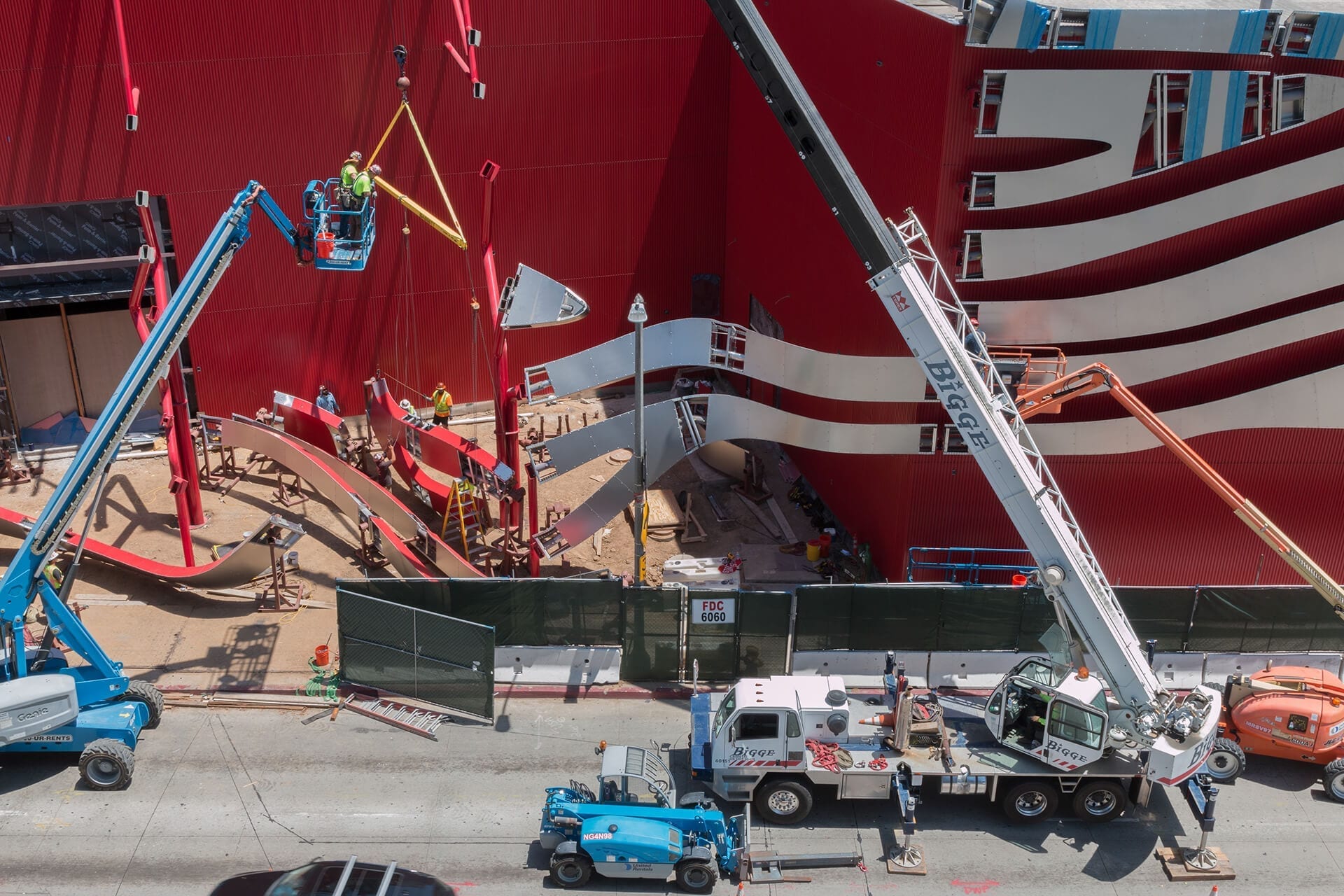
Using aluminum extrusions rather than steel allows for a lighter load on the structure of the façade. Breaking down the dual curves into units allowed also for much quicker assembly on site. The Petersen Museum.
Image from A. Zahner Company
An extensive collection of rare and valuable vintage cars
The museum’s exhibition space totals 95,000 square feet (8,825 square meters) spread across three levels bringing together 25 galleries representing the history, industry, and design of the automobile.
The visitor experience is intended to begin on the top storey, which is dedicated to the history of the automobile. The upper floor also showcases the exhibition Southern California: A Region in Motion, which uses interactive videos to demonstrate how LA “grew out, instead of up, like most cities”.
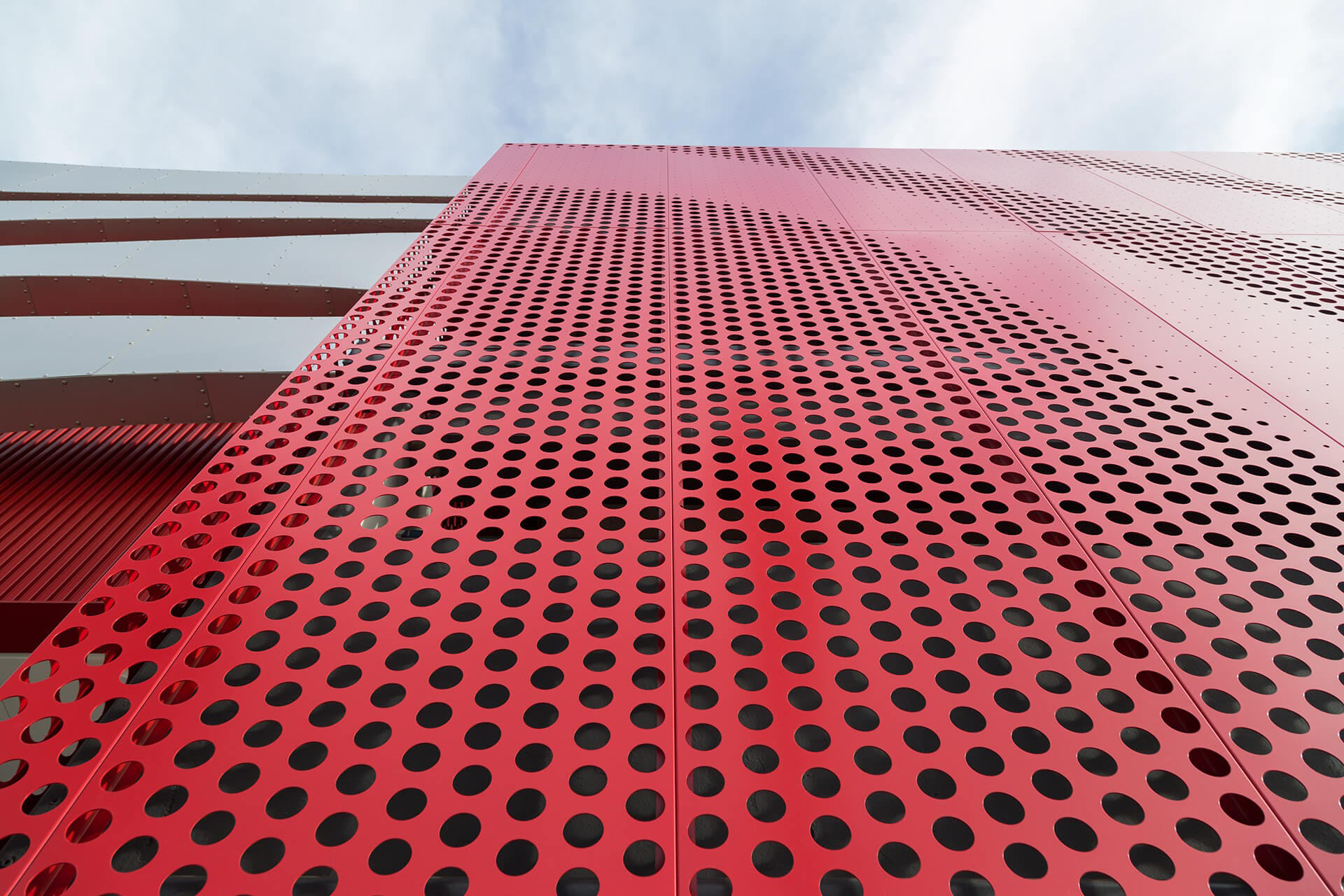
The red-painted perforated aluminium screen that forms a backdrop to the wavy stainless steel Angel Hair ribbons for the façade of The Automotive Petersen Museum.
Photography by Tex Jernigan.
The ground floor focuses on car design showcasing an array of extravagant automobiles. It includes French Art Deco cars from the 1930s, an exceptional period for automobile design. Among the rare vintage models, visitors can admire a 1939 Delahaye Type 165 and the famed 1936 Bugatti Type 57SC Atlantic, by some accounts the most valuable car in the world. A “Precious Metal” exhibit in the Bruce Meyer Family Gallery features an estimated $120 million worth of silver-skinned American and European cars.
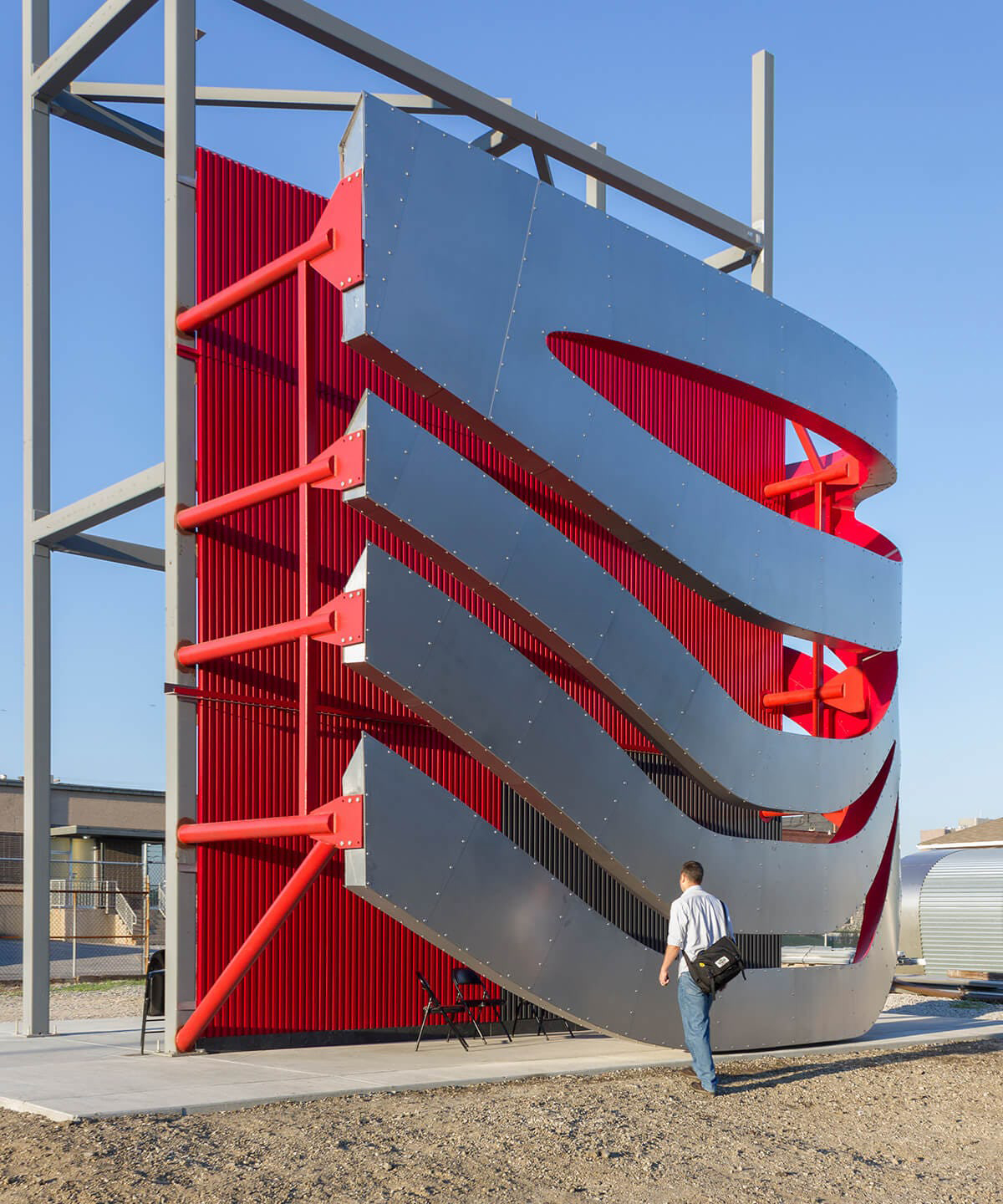
The full-scale mock-up a section of the façade of The Petersen Automotive Museum in red-painted aluminium and wavy ribbons in stainless steel Angel Hair. The red backdrop was clearly changed since the mock up to a perforated finish rather than vertical strips.
Image from A.Zahner.
The second floor is principally concerned with industrial engineering—including design, performance, and a collection of interactive teaching exhibits. Special displays on the industry floor cover racing, motorcycles, hot rods, and customs. The third floor chronicles the history of the automobile with an emphasis on the car culture of Southern California. And if visitors are still feeling up to it there are an additional 125 to 150 vehicles from the 300-plus pieces from the permanent Petersen collection which are displayed in the underground “Vault” located in the basement level of the building. By now you will have understood that one of the ambitions of the museum is to attract return visitors.
In February 2019 the Petersen Museum celebrated its 25th-anniversary celebration by parading some of Hollywood’s most famous cars past Los Angeles landmarks such as the “Little Miss Sunshine” Volkswagen bus and the James Bond XK-R car from “Die Another Day.”
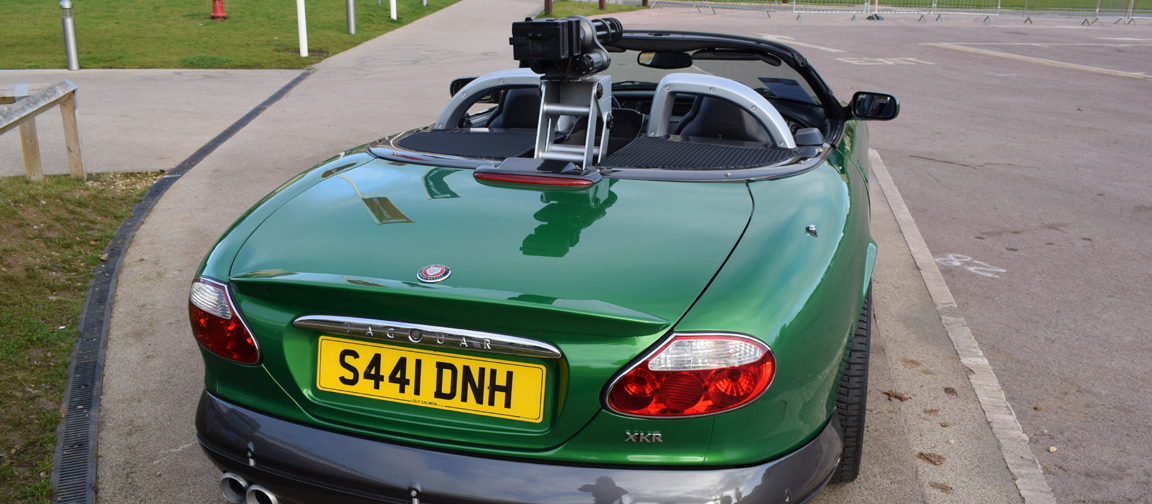
The villain’s (the character Zao played by Rick Yune) car, the Jaguar XK-R complete with M134 Minigun, used in the 20th James Bond 2002 film Die Another Day. Part of the exhibits shown in The Petersen Automotive Museum, Los Angeles.
Image from The Jaguar Daimler Heritage Trust.
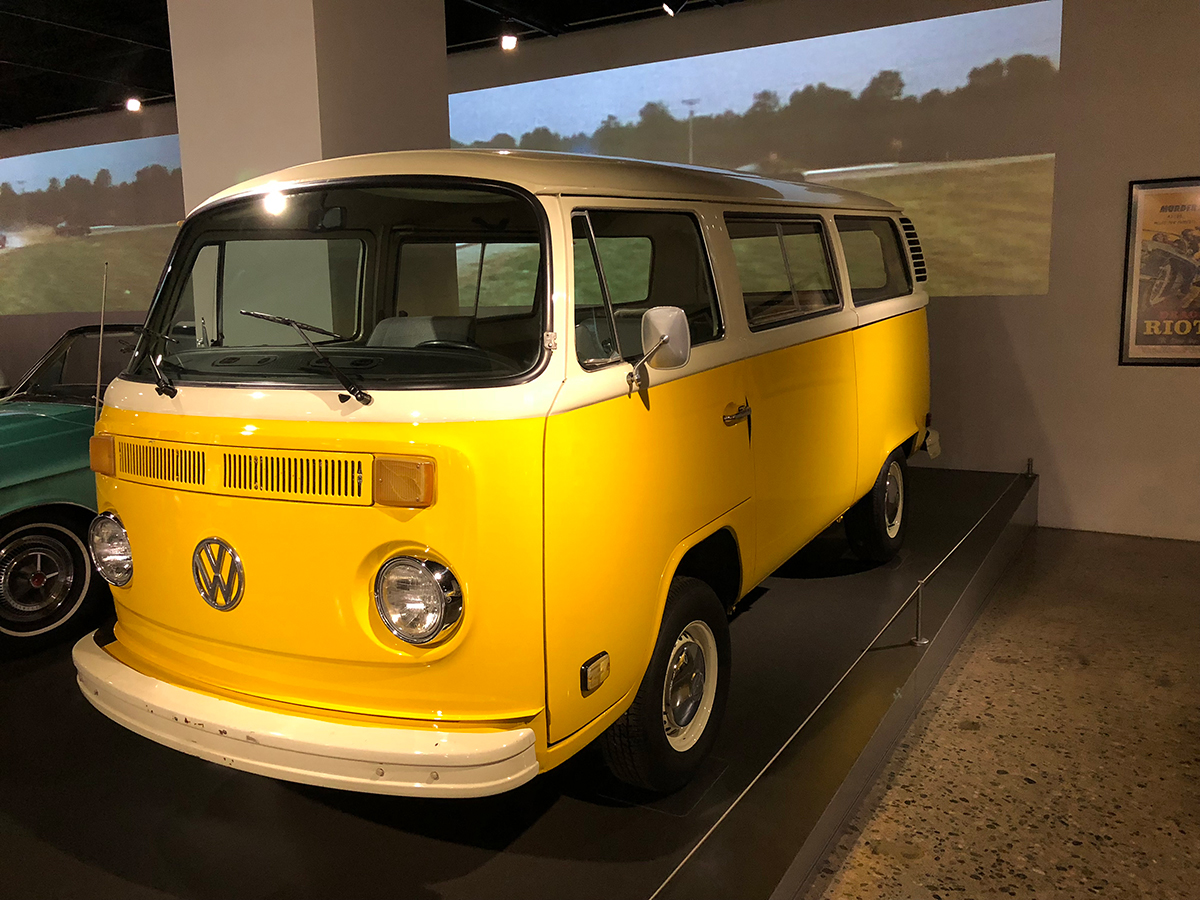
The yellow VW Camper van used in the 2006 film Little Miss Sunshine exhibited at The Petersen Automotive Museum, Los Angeles, California.
Image from Film Oblivion.
Attracting the younger generation with a trove of interactive technology
To make the museum more appealing to younger audiences a trove of interactive technology was installed. Where once were only 10 flat-screen TV monitors are now a flotilla of interactive electronics, including 47 Panasonic projectors, 35 interactive touchscreens, 25 LED monitors, 291 three-dimensional displays of engines and scale models and several enormous projection walls that will better capture the excitement of motoring and automotive art. The new museum also features 10 Microsoft Xbox Forza driving simulators, where visitors can race against virtual professionals or against one another. To get cars into and out of exhibit spaces, the Petersen has a car elevator, said to be one of the largest in Los Angeles, capable of lifting 14,200 pounds from street level to the top floor.
Through this extensive renovation, the Petersen Automotive Museum aims to be in the same league as the BMW Museum in Munich or the Museo Ferrari in Maranello, Italy. It also benefits from the attraction of LA’s famed Museum Row, which features buildings such as the Los Angeles County Museum of Art (LACMA), originally designed by William Pereira, again one of the leading lights of the futurist Googie movement that prevailed at the time in California. Located just opposite the Petersen museum is the much loved May Company building (renamed the Saban building) with its characteristic Streamline Moderne style. It has been recently renovated as part of Renzo Piano’s design for the Academy of Motion Pictures Arts and Sciences (AMPAS) which is scheduled to open in April 2021.
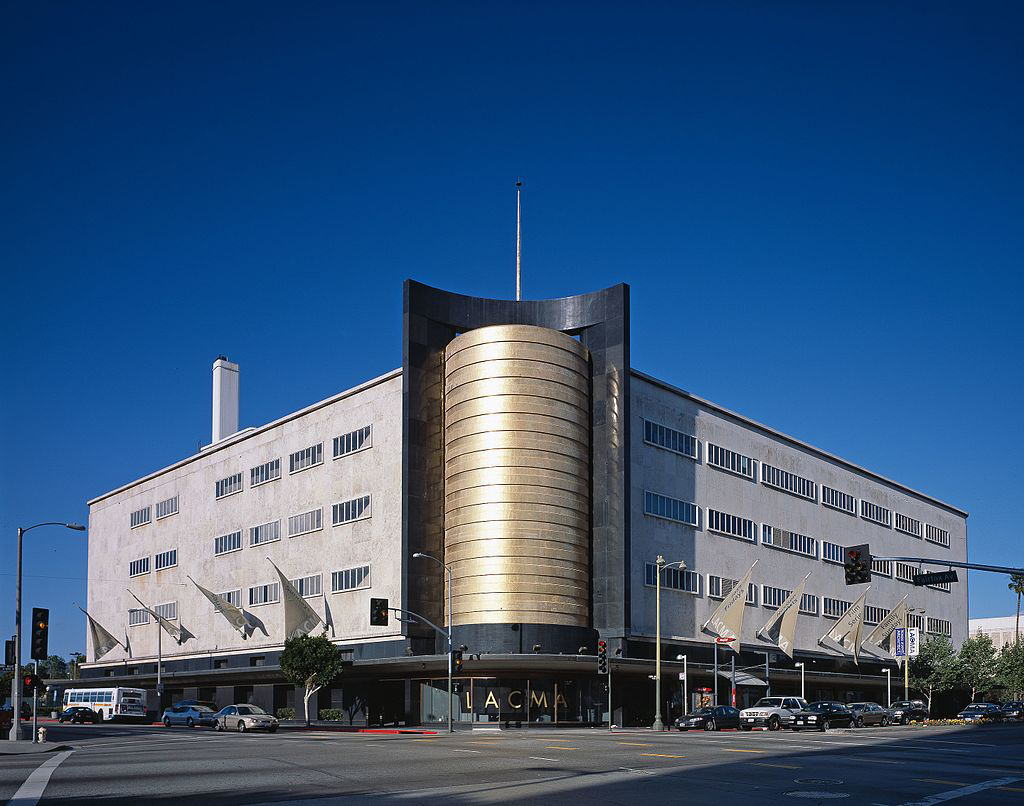
The former May Company building was a department store designed and built in 1939 by architects A. C. Martin and Samuel Marx. Its eye-catching southwest corner hemi-cylinder, clad in Italian gold-glass mosaic, was designed to attract suburban motorists.
Photography by Carol Highsmith
According to KPF co-founder and Chairman A. Eugene Kohn, the new design was “intended to express constant motion, suggesting speed, aerodynamics and the movement of air. While its other museum neighbors are the gentlemen in black tie, this is a ballerina.”
The work of American artist Richard Serra (b. 1938) takes sculpture off the pedestal and cleverly utilises industrial materials and processes. In doing so, he makes sculpture occupy a common behavioural space that can invigorate the everyday perception of the built environment. Serra uses materials such as lead and steel and explores their intrinsic properties. A work that signalled his maturity as an artist is One Ton Prop – House of Cards (1969), where four sheets of lead antimony form a cube by standing on their 2.5 cm edges. To achieve this, Serra took advantage of the individual pieces’ weight and gravity to counterbalance them and make them free stand without soldering.
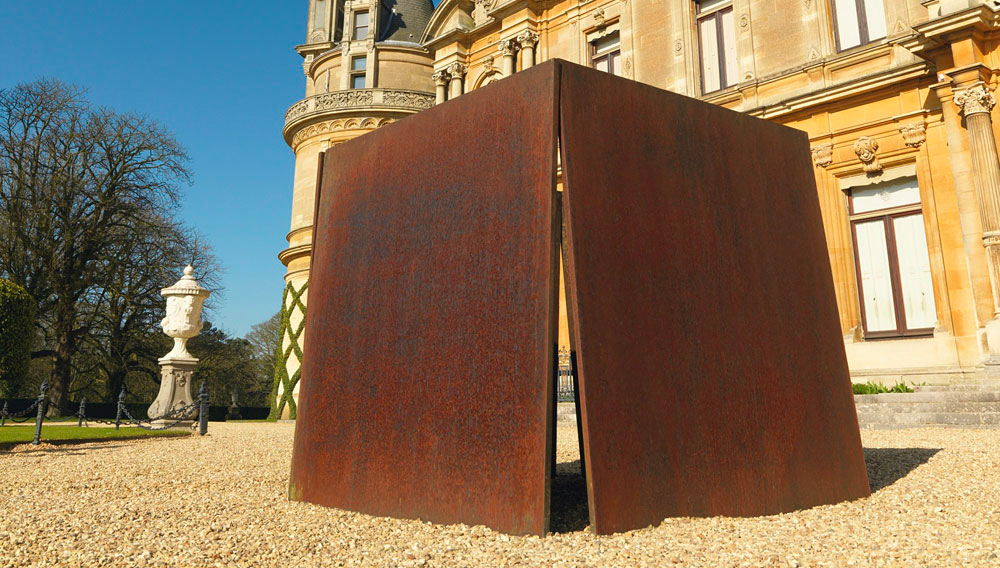
Richard Serra’s One Ton Prop (122 x 122 x 2.5 cm) consists of four pieces of lead leaning against each other. The shape of the cube appears freestanding without welding or props, expressing both solidity and delicate balance.
Image by Christies.
Corten Steel: From Shipbuilding to the Art Gallery
Today Serra’s signature style can be recognised in the use of large plates of weathering steel, also known as corten, such as the ones used for manufacturing prows of ships. Whilst continuing to explore material properties such as weight and gravity, he has employed the malleability of steel to place lithe vessels in the abstracted space of the art gallery.
My first encounter with a Serra sculpture was Snake (1996) at Bilbao’s Guggenheim Museum, shortly after its opening in 1999. Snake consists of three 5cm-thick meandering corten pieces (4 x 31.7 x 7.84 m). Each of these long sheets is made by welding together two elliptical sections of cone, joined by the lateral edges with the concave spaces looking in opposite directions, which make the sinuous form of a snake appear. Spacing the three long pieces at ground level makes two undulating passages appear between them. The middle sheet is upside down, making the base of the elliptical section become the top. As the radius at the bottom is smaller than at the top, some parts of the corridors narrow at the bottom and widen at the top, whilst maintaining an overall sense of proportion through the whole piece, since all sections, regardless of their position, have the same centre. The key here, as in much of Serra’s work, is the negative space.
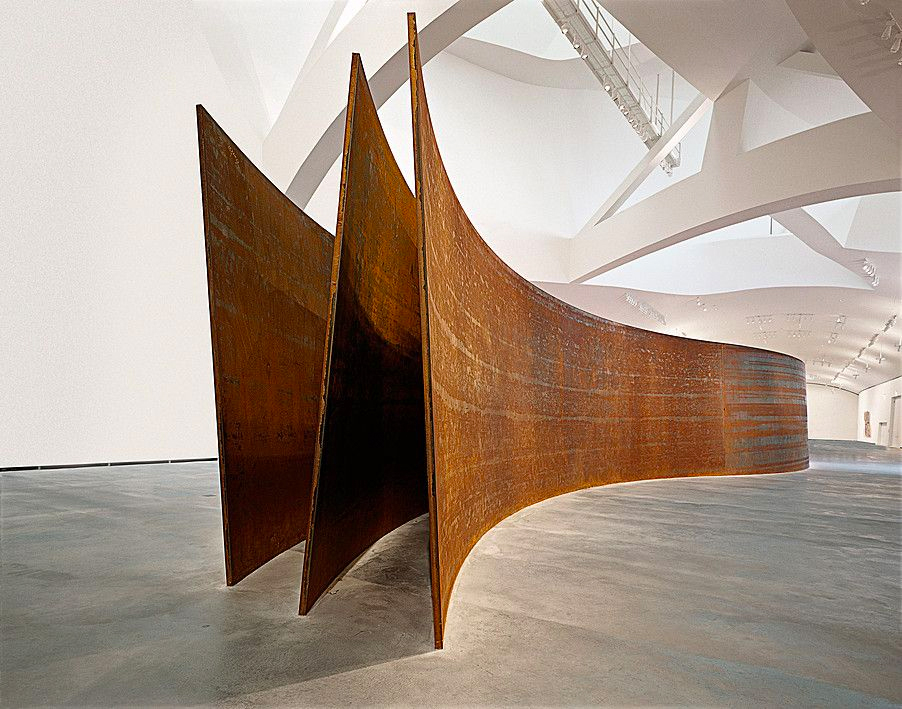
Richard Serra’s Snake (1997) in Bilbao’s Guggenheim Museum. The positioning of the corten plates expand and compress the space between them creating accessible and inaccessible passages.
Photography by nlinh.
Steel Plates Compressing and Expanding Space
One of the passages anticipates a compression of space, restricting access to it, whilst the other feels more expansive and inviting. Walking inside the piece one can feel the textured lateral surfaces of the corten sheets, their unique deep orange, and the intensity of the oxide. The sense of being and moving within such space changes as the leanings of the metal afford different spaces of possibility whilst surrounding us with delicately sinuous surfaces. There is a sense of adventure, for the body feels animated as if pulled forward by an uncertain force. Transiting the long passage, one can feel disoriented and scared at times. The perception of the duration of time augments. Every second counts.
Snake is a dynamic encounter with accessible and inaccessible spaces, gravity, directionality and multiple perspective points. This multiplicity becomes more patent when approaching the sculpture laterally and surrounding its outer walls like those of a fortress. Seeing it from the balcony above also provides a vantage point that reveals its emphatic graphism and connects Serra’s large steel sculpture with the forceful mark-making his drawing practice.
Snake is placed in the museum’s gallery 104, or the “fish gallery”. From the outside, Frank Gehry’s architectural design resembles the soft curvature of a fish’s backbone or the fluid forms of Bilbao’s river. From the inside, a set of flying buttresses of varying lengths evoke the spines of a fish. Legend has it that Gehry designed the gallery to specifically accommodate Serra’s Snake, thus continuing a fruitful and provocative conversation between architect and sculptor. The theatricality of Gehry’s design differs strongly from the simplicity of Serra’s approach, who does not try to prescribe an emotional effect. The sculpture is placed along the longitudinal space, and an interesting dynamic appears as it cuts across the flying buttresses. Serra’s minimal take on the characteristics of corten and direct play with geometric forms provokes a raw experience of perceiving space through movement in a material field. The industrial material can be comforting and familiar while threatening and impenetrable. It activates our proprioception, the sense of our body in space, in conjunction with a visual and acoustic experience that build a sense of anticipation, possibility, mystery and discovery.
Twisting Architectural Function
In 2005, the same gallery at Bilbao’s Guggenheim held Snake surrounded by other series of Serra’s work, Torqued Ellipses I, II, IV, V, VI (1996-9) and Double Torqued Ellipses I, II, III (1997-9) for the exhibition “The Matter of Time.”
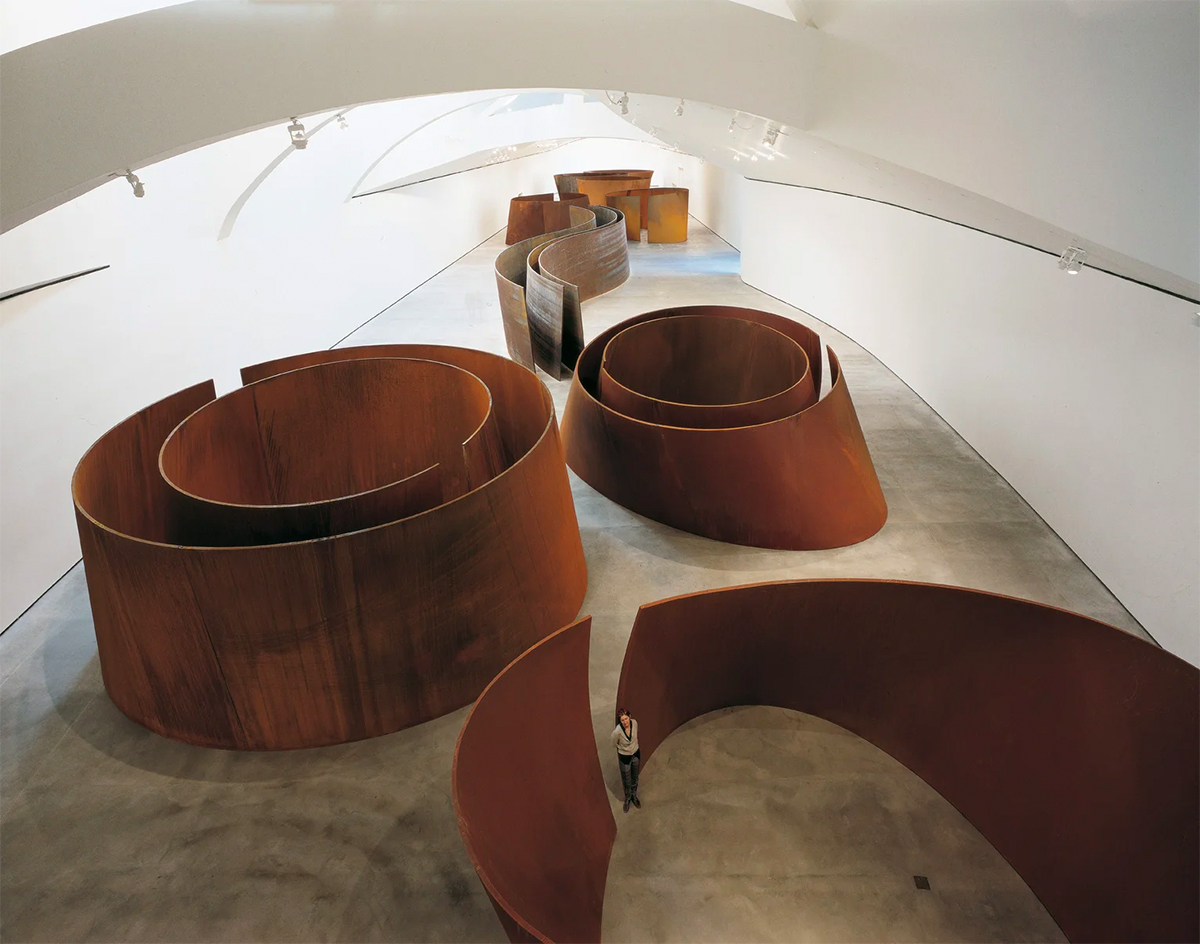
Richard Serra’s Snake alongside the series Torqued Ellipses and Double Torqued Ellipses for “The Matter of Time” exhibition (2004). The installation prompts an exploration of negative space and the material properties of corten steel.
Photography by Guggenheim Museum, Bilbao.
On this occasion, Serra proposed a journey from simple to more complex forms. The departure point was cylinder and cone sections cut at different planes, sometimes parallel, sometimes inclined, thus revealing circular and elliptical forms which would become the top or bottom of the piece when free standing. As the section is cut open, the properties of rolled steel become apparent for a single corten sheet can lean in different directions depending on shape and weight. This makes some pieces appear as if torqued or twisted. Walking around a piece from the outside, can be unpredictable, whilst entering it offers a total view of its curvilinear shape. Finally, looking at the top opening frames the forms of building, as if containing Gehry’s spectacular conceits.
In Double Torqued Ellipses Serra introduces variations of this procedure to achieve more complex configurations, such as corten rings wrapped around each other that look like reels or torcs, the Bronze Age open front necklaces found in ritual burials and hoards. Some rings might have openings, thus allowing to walk into the centre, or space in between that permits to circumnavigate them in a spiralling movement. The view from above can remind of a galaxy, where the rings stand for the capricious orbits of different planets circling round the same centre.
From the outside, simple individual forms can resemble a huge thimble or a fort, others with a smaller base look like pots. Nevertheless, the installation must be seen as a whole. At floor level, it is a journey through walled containers, sinuous thoroughfares and concave gathering sites. It feels like an abstracted urban space all made of curves, rather different from our experience of the modern city, mostly defined by rectilinear forms. Yet, these contradictions are to be resolved by whoever experiences them, as the artist shuns from prescribing specific emotional effects.
Serra has deservedly become an emblematic figure of American art, for he presents the basics of modern architecture and engineering through an experiential take on materials which, even if seemingly muted, have the potential to inspire both awe and fright.
The purpose of anodizing is to passivate the surface of a metal sheet or profile. Passivation allows the surface of the material to develop a protective coating or a shield on its surface that will protect against future corrosion.
The process was patented in 1923 by two British men, Bengough and Stuart and the use of industrial-scale anodizing began in the same year. One advocate was the Curtiss Aeroplane Company who used the new method to manufacture an experimental flying boat for the US Navy – the HS-2L.The aircraft had four huge wings and in order to save weight, they were fabricated from duralumin – a proprietary aluminium alloy that was one of the first lightweight metals used in aviation. Landing on the sea, however, meant salt corrosion was a problem so the HS-2L’s wings and other duralumin components were anodized to protect them from degeneration.
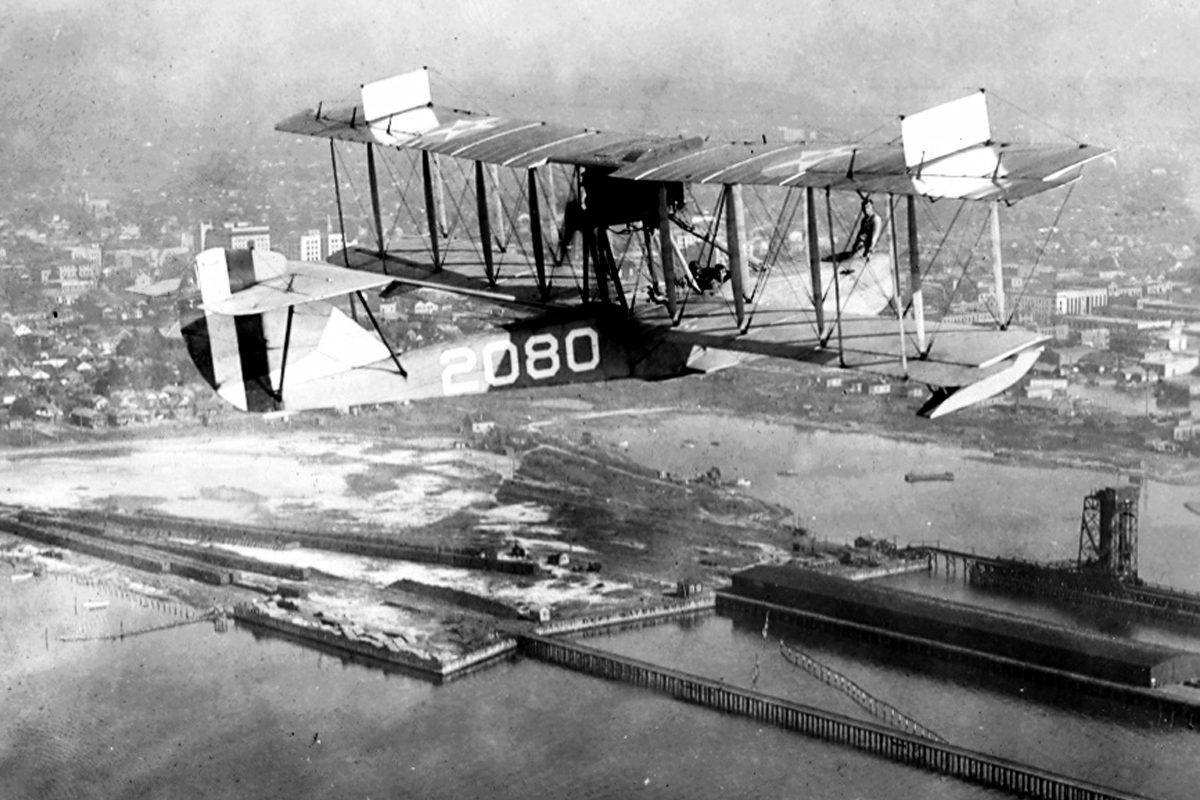
A HS-2L Flying Boat in the air over Florida in the 1920s. The aircraft was designed and built by the Curtiss Aeroplane Company using duralumin, a lightweight aluminium alloy.
Image from U.S. Navy National Museum of Naval Aviation.
The anodizing process
Bengough and Stuart’s anodizing technique uses non-metallic substances that, after an electrolysis process, provide aluminium or an aluminium alloy with a corrosion resistant coating. This is achieved by submerging the metal in a bath containing chromic acid or a material capable of producing chromic acid at the anode.
Here is a simple description of the process:
The aluminium sheet or part is immersed in a solvent suitable to remove grease, then rinsed in hot water to prepare it for becoming the anode.
The next step is to prepare the acid solution for anodization. It must contain 3% chromic anhydride and be free of sulphuric acid and sulphates. The cathode can be carbon and the temperature should be raised to 40 degrees celsius before the aluminium sheet or part is placed in the solution bath.
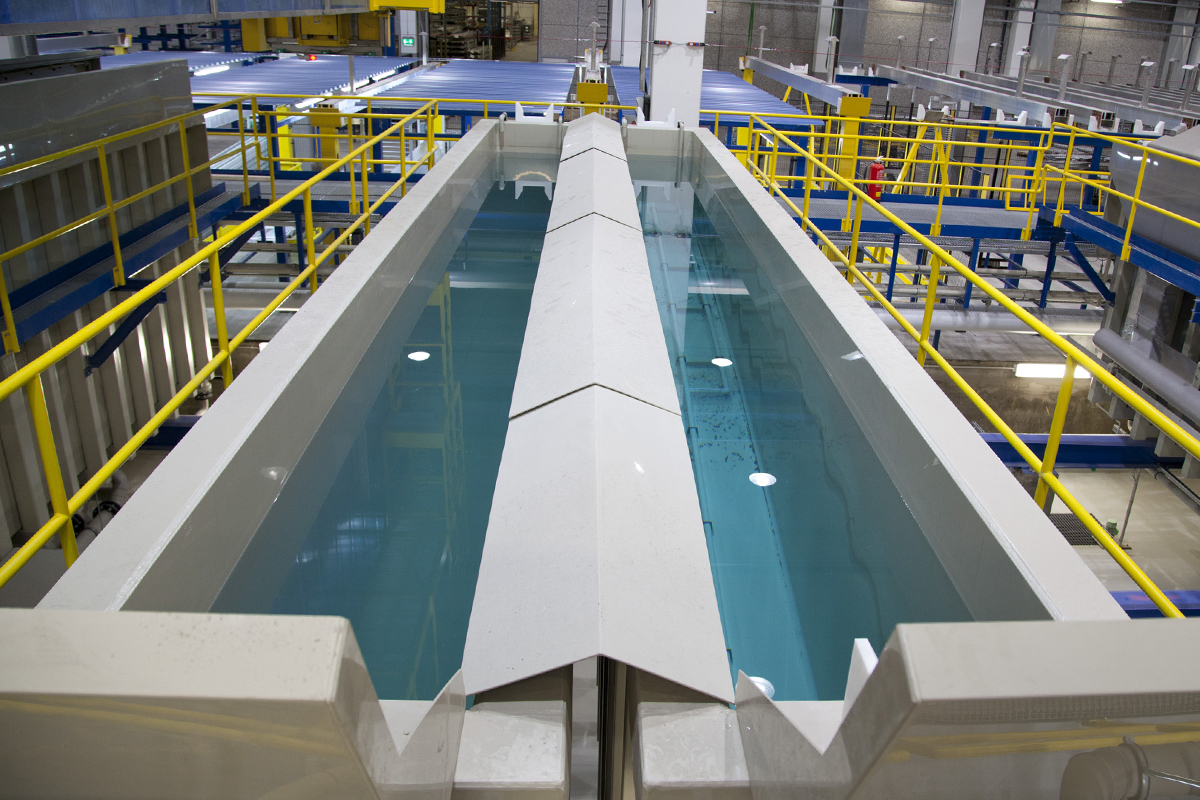
Rinsing baths in a fully automated aluminium anodizing plant. The process of anodization utilises electrolysis to give metals a corrosion resistant anodic coating.
Photography by Galvatek.
Once this has been done, the voltage should be gradually increased over 15 minutes to 40 volts. After maintaining 40 volts for at least 35 minutes, the voltage is increased over a further 5 minutes to 50 volts and kept at this level for 5 more minutes. The object can then be removed from the bath, washed and dried. It is now ready for further processing, such as painting, oiling or dying.
The resulting anodic films will increase the surface resistance to corrosion and provide better adhesion for paints and adhesives.
The advantages and disadvantages of anodized coatings
The most commonly anodized metal is aluminium but other metals can have an anodic coating applied including titanium, zinc and even iron. Anodic coatings are much more durable than paint but are also brittle. If an anodized sheet is put on a press brake to be formed, the anodic coating will fail due to its inherent brittleness. Even so, the anodic coating on aluminium is much harder than the metal’s original surface.
One of the main advantages of the anodizing process is that it allows for coloured, cosmetic coatings other than paint to be applied. This can be done by anodizing the metal with a thin transparent film that interferes with reflected light, producing a perceived colour. Another way is to use a thicker anodic coating which can then be chemically dyed.
Using dyes to colour anodized metal
The range of dye colours available is vast but the most popular are yellow, green, blue, black, orange, purple and red. These are also the cheapest to produce, however, lightfastness is another problem that has to be considered. Blues and reds are particularly susceptible to ultraviolet light and will fade if exposed to sunlight over some time. Once a product has been anodized and dyed, this problem can be solved by applying a sealing to the top surface to prevent the colours fading.
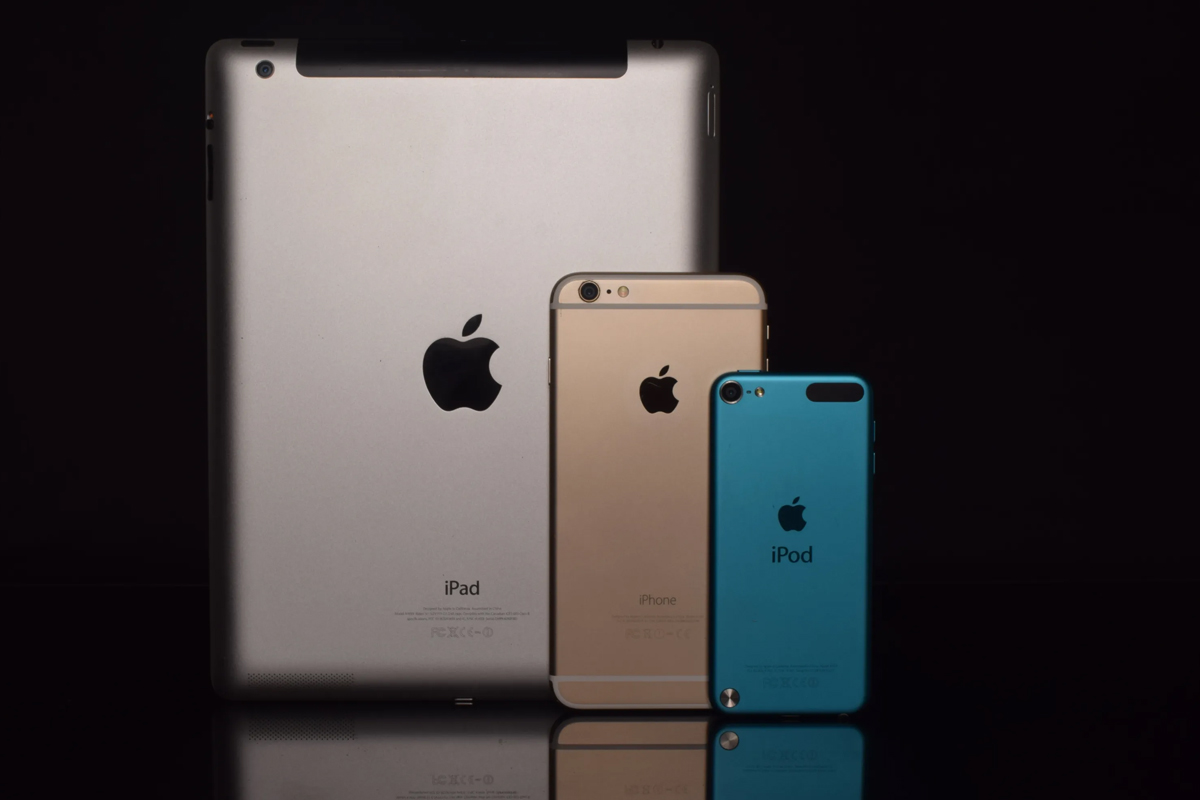
Iconic Apple products: the iPad, iPhone and iPod touch. The aluminium casings undergo a process called anodization to enable durable, lightfast colouring of the metal.
In the architectural world, dyes that replicate real metals are very popular. The most common stains in use in construction projects include black, gold, bronze and champagne. These dyes applied to ironmongery and other architectural metals mimic the appearance of the real metals, and gold and black dyes that have been produced by chemical methods such as ferric ammonium oxalate are significantly less prone to ultraviolet damage.
Somewhere on the Mongolian grasslands in the year 1171, a nine-year boy named Temujin, along with his mother, Hoelun, his three brothers and his two half-siblings were left to fend for themselves.
The boy’s father had been the Great Chief and ruler of most of Mongolia, Yesugei Baghatur. He died at the age of 37 after he was fed a poisoned meal by Tatars at a wedding celebration. The Tatars were exacting revenge for an earlier raid on their lands by Yesugei.
The manner of Yesugei’s death in such unpleasant circumstances was ironic. His name translates as ‘like nine’ and in Mongolia, the number nine has always been considered to be the luckiest number. It is a symbol of the power of an intelligent and alert mind.
A ruthless Mongol Emperor
Temujin, which in Mongolian translates to ‘of iron’, survived the time in the wilderness with his remaining family and grew into one of the most admired and feared military leaders in history: Genghis Khan. ‘Khan’ simply means chief or military leader in Mongolian.
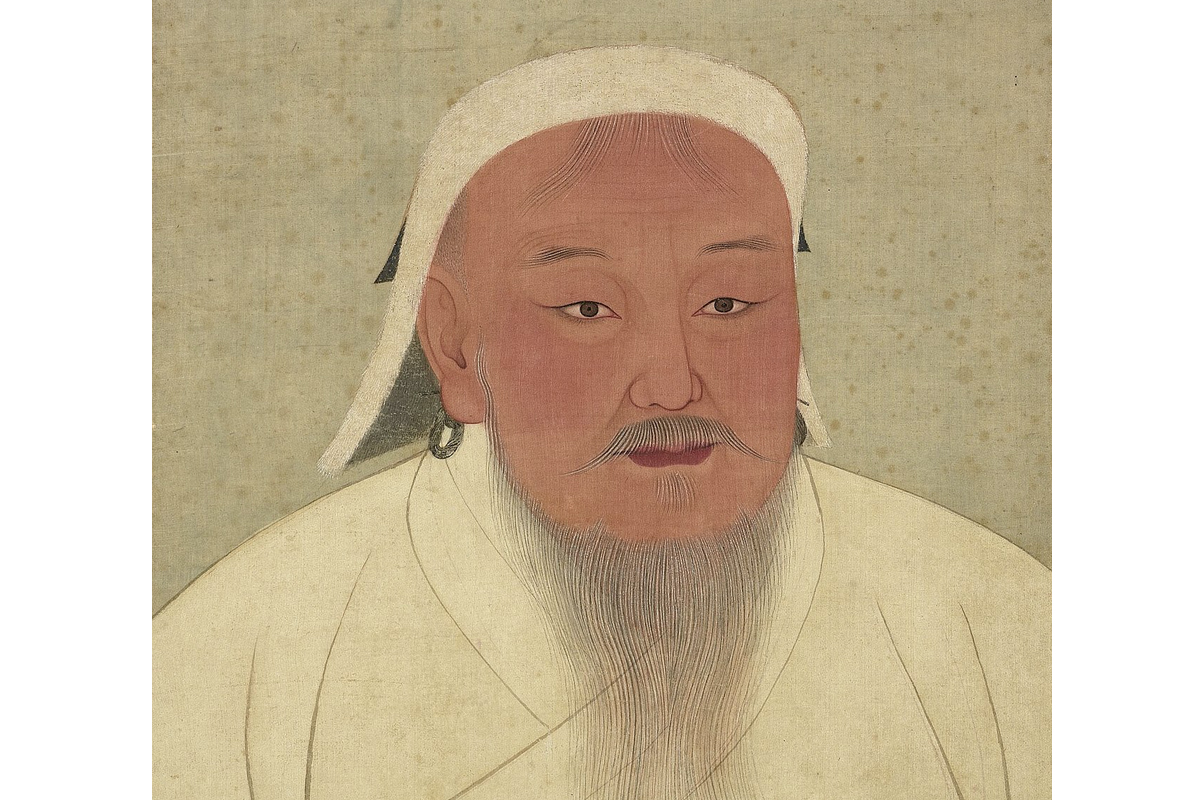
A 14th-century portrait of Genghis Khan. At the height of his power the Mongol leader ruled about 17% of the world’s landmass from East Asia to the eastern fringes of Europe.
Genghis Khan and his armies are thought to have been responsible for approximately 40 million deaths which was almost 11% of the entire world’s population at that time. Slaughter on this colossal scale did not return until World War 2; a conflict that killed 70-85 million people, equivalent to 3% of the world’s population.
Demise and revival of a national hero
During the occupation of Mongolia by Soviet forces during the 20th century, Genghis Khan and his legacy began to be removed from Mongolian history. The deeds of the great Mongol leader, both good and bad, were erased from Mongolian school textbooks and he started to fade away.
Once the Soviets left in the early 1990s, Genghis Khan again became a popular figure in Mongolia. His image appears on the country’s banknotes, many of its postal stamps and the main airport in the capital city of Ulaanbaatar also bears his name.
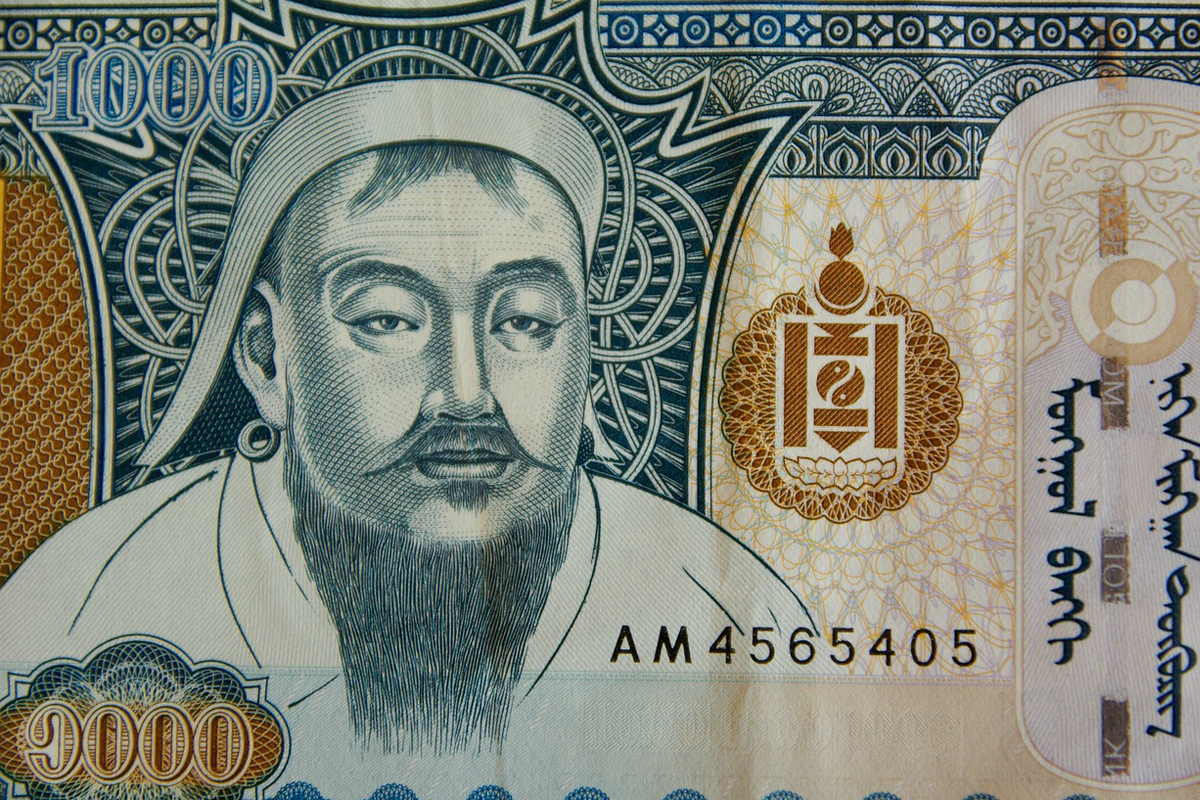
Genghis Khan on the Mongolian 1,000 tugrik banknote. The former Emperor is also celebrated across the country in names of buildings, on stamps and numerous monuments.
Statue memorial to Genghis Khan
Such is the old Khan’s current popularity that the Mongolians have recently erected an enormous statue in his honour. In 2008, a design team led by the Mongolian artist and sculptor D. Erdembileg and the architect J. Enkhajargal completed a complex, built to commemorate Genghis and celebrate his achievements. The centrepiece to this complex is an incredible 250- ton, polished stainless steel statue, portraying Genghis Khan saddled on his horse. The Khan and his steed are gazing sternly towards his place of birth in the East and, in his right hand, the Emperor holds his golden whip. The whip is said to have helped him conquer half the world and has been formed from rose gold PVD stainless steel, very similar to the product made by Double Stone Steel.
The complex is 54 kilometres from Ulaanbaatar on the bank of the river Tuul, the place where the legends say Genghis found his golden whip. The circular base of the statue is a cultural museum where visitors can see a replica of the whip, eat traditional Mongolian food or take an escalator to the viewing platform on top of the horse’s head. The architectural design is intriguing – each of the 36 supporting columns represents a former Khan.
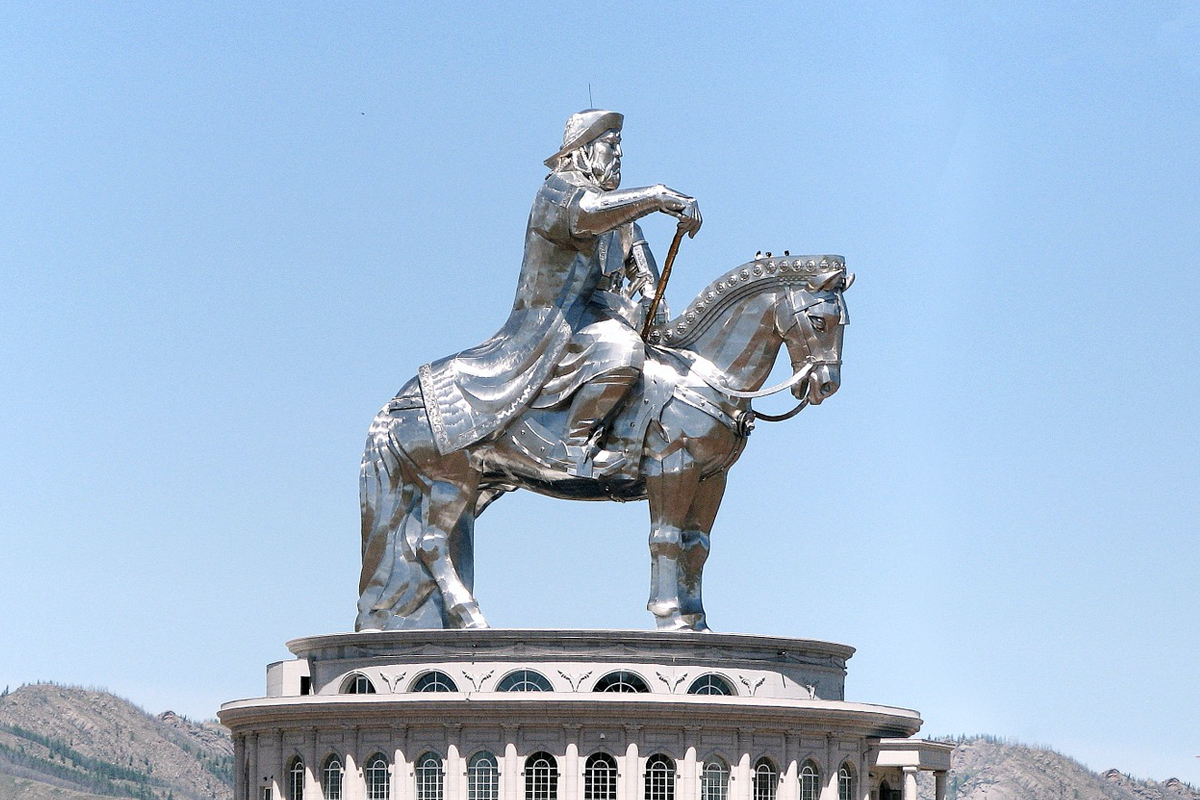
The Genghis Khan memorial complex in Mongolia. The 250-ton, 40m high, stainless steel monument stands on top of a museum and is the largest, equestrian statue in the world.
This monumental statue is the largest equestrian statue in the world, towering 40m above the ground and completely dominating the bleak, grass-filled landscape. We need to think of it as the cultural equivalent of the more famous, ‘Christ the Redeemer’ in Brazil or Mount Rushmore in the USA.
In 1933, the U.S. Steel Corporation developed and patented a new weathering steel alloy.
The company sold the product under the brand name Cor-Ten and it is still a popular product today, used throughout industry, art and architecture. It was designed to be tough and to have a controlled corrosion rate – the name comes from an amalgamation of the words corrosion and tensile.
Design purpose of Cor-Ten steel
U.S. Steel specifically designed Cor-Ten for the construction of hopper cars used in the railroad industry. A hopper car is a railroad freight car used to transport raw materials such as coal, wheat, and iron ore in large quantities. They have to be very robust and resilient, able to withstand thousands of tons of coal or iron ore dropped in them year after year. Cor-Ten was a way to remove the need for painting the trucks and extending the working life of the hopper car.
The weathering steel was also used to build passenger railcars from the 1930s to the late 1940s. These passenger cars were considered a paradigm shift in material use from the traditional timber railcars. Trains such as the art deco ‘Spirit of Progress’ in Australia, were fabricated from painted Cor-Ten which was a very advanced material for its time. It is still used for its original purpose of manufacturing bulk transport railcars to this day as the inherent strengths and the cost of the product remain attractive to the railway industry.
Shipping containers are also manufactured from Cor-Ten, making it a heavily used material in maritime transport.
Cor-Ten steel in architecture
It was not until the 1960s that architects discovered Cor-Ten. The pioneer for the use of this weathering steel was the brilliant Finnish architect Eero Saarinen who had designed the Gateway Arch in St. Louis and the iconic TWA Flight Center at John F. Kennedy Airport in New York.
He was commissioned by William Hewitt, the President of John Deere, the heavy agricultural equipment manufacturer, to design their new headquarters. Hewitt was under pressure to move the company’s world headquarters to either New York or San Francisco but knew his customers would not be impressed by a move to either city. He decided instead to locate the new headquarters in Moline, Illinois but insisted it had to be a distinctive building.
Hewitt wanted a down-to-earth, rugged and practical building that reflected the company’s clients and their businesses. Saarinen satisfied the brief perfectly by using Cor-Ten steel; the earthy rust coloured corrosion that develops on the material, matched the type of rusty finish seen on metal ploughs and other farm implements used by John Deere’s clients. It was the first architectural use of pre-rusted Cor-Ten steel and, just like the railcars before it, would never need painting.
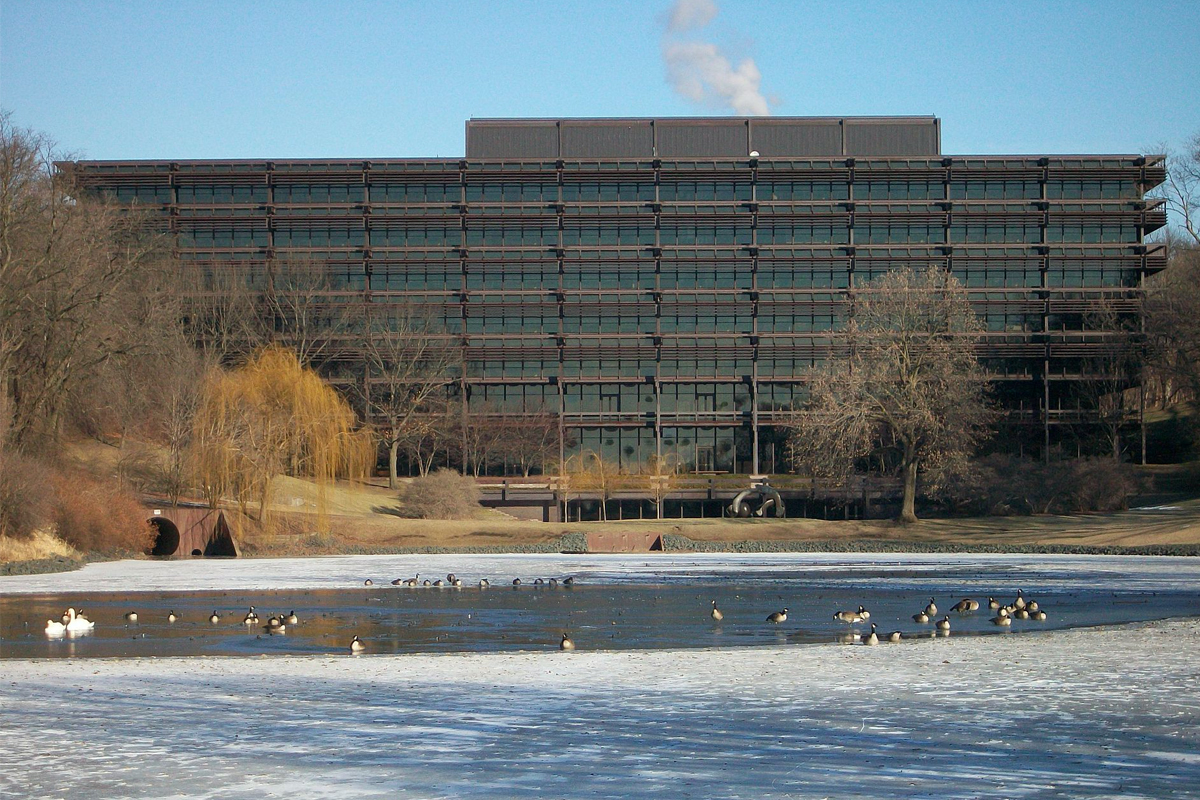
John Deere Headquarters in Moline, Illinois. The complex of three buildings designed by Eero Saarinen is constructed from Cor-Ten steel and holds around 900 employees.
Photography by Ctjf83.
Tragically, Saarinen never saw his building completed. That honour went to Kevin Roche, who worked with him and finished many of Saarinen’s projects after his early death at the age of 51 while undergoing surgery to remove a brain tumour.
U.S. Steel Tower in Pittsburgh
The next notable, architectural Cor-Ten steel project was for U.S. Steel itself, the company that invented the material. The corporation wanted a building to showcase the properties of Cor-Ten steel to the architectural community and decided the best way of achieving that was to build their head office out of it.
Construction on the U.S. Steel Tower in Pittsburgh, Pennsylvania started in 1967 and finished in 1971. Standing at 841ft tall, it is the tallest building in the city and has the Cor-Ten steel columns on the exterior to display the building material.
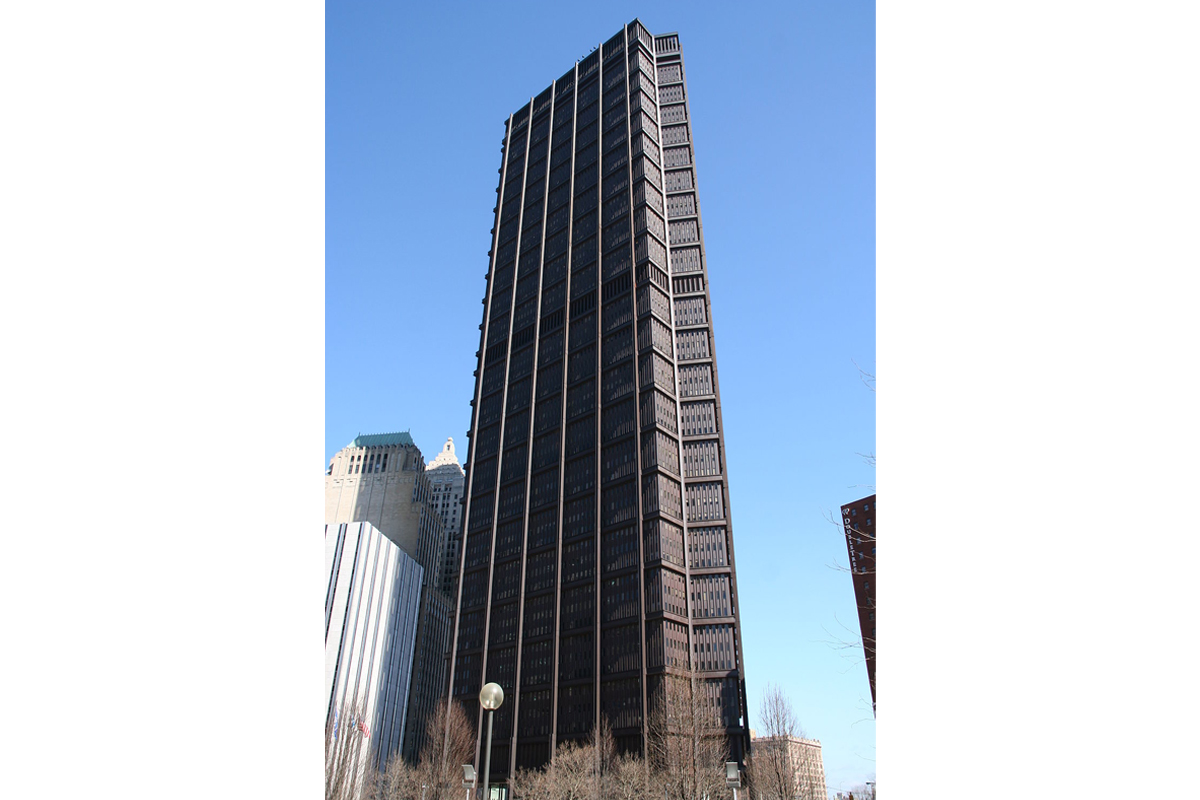
U.S. Steel Tower in Pittsburgh, Pennsylvania. The building is 64 stories high with an acre of office space on each floor and is constructed from Cor-Ten steel.
Photography by Derek Jensen.
One problem uncovered in using Cor-Ten to construct the tower was that in rainy weather, the initial corrosion layer washed off the surface of the steel, staining the surrounding pavements and buildings with a rusty brown or reddish colour. Once the weathering was complete, the company organised a clean-up operation to remove the stain although the sidewalks still have a decidedly rusty tinge!
Cor-Ten used in sculptures
Cor-Ten steel has also found a niche with sculptors the world over. Antony Gormley’s ‘Angel of the North’ in the United Kingdom, is a massive 200-ton, 20-meter tall, and 54-meter wide sculpture made from the steel.
‘The Angel of the North’ by artist Antony Gormley stands in Gateshead, North
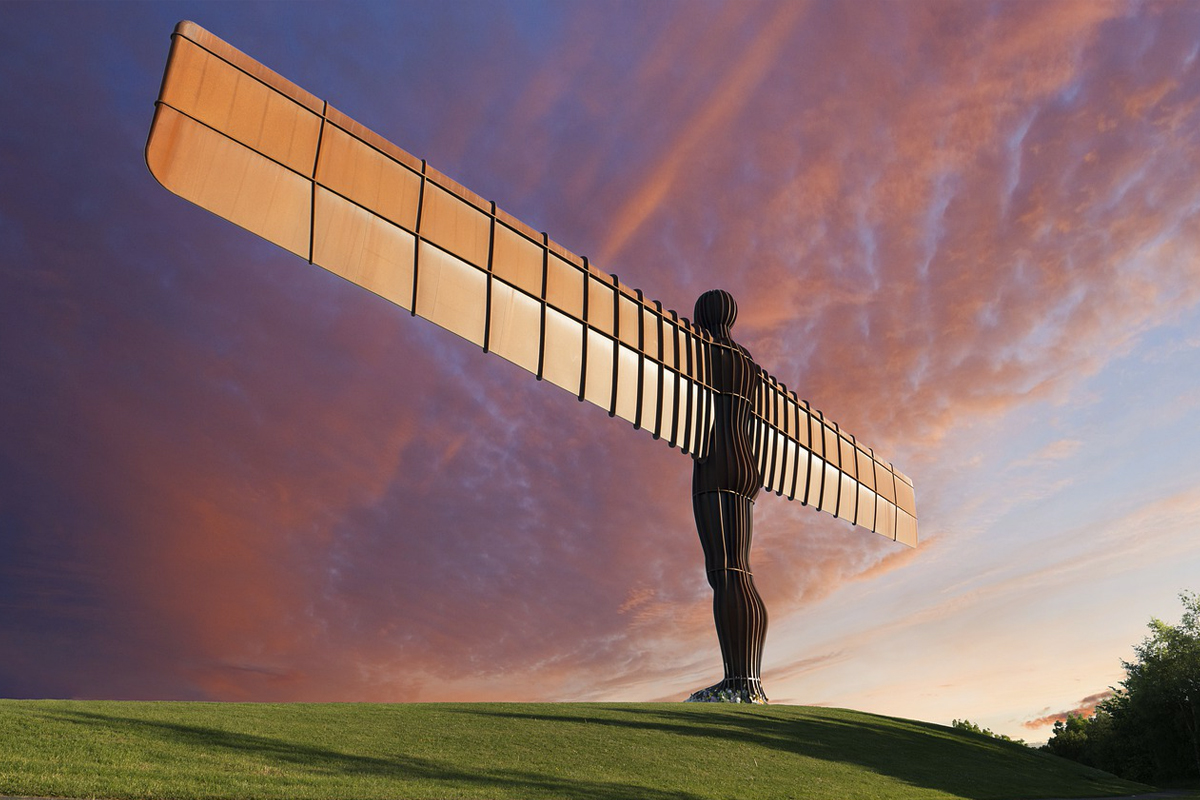
‘The Angel of the North’ by artist Antony Gormley stands in Gateshead, North England. The sculpture is made from Cor-Ten steel and the wings have a span of 54 metres.
In Australia, Astra Parker used Cor-Ten to produce her group piece, ‘Sisters’ and Pablo Picasso also worked with the material to produce his untitled piece known as ‘The Chicago Picasso’, which he gifted to the city in 1967.
Pittsburgh’s tallest, most massive skyscraper is a multifaceted paradox of elegance and clumsiness, success and failure. The US Steel Tower later renamed the USX Tower is an emblematic building both for the city of Pittsburg and the US steel industry. This 64 storey office building culminates above the city at 256 m. At its completion in 1970, the U.S. Steel Building seemed like a monument to the triumph of the steel industry. In a city full of corporate headquarters such as Gulf, Westinghouse, Alcoa, and Koppers, U.S. Steel would be the largest in town, indeed the tallest building between New York and Chicago.
Founded in 1901 by J. P. Morgan, Andrew Carnegie, Elbert Gary and Henry Moore the giant U. S. Steel Corporation was ranked as the world’s most valuable company worth $492 million or $15 billion in today’s money. In 1902, only their second year of business, U. S. Steel made approximately 67% of all the steel produced in the USA. In 1943 the company employed 340,000 people. At the very peak of its steel production in 1953, the company produced 23 million tons of steel.
Before working on the design of the US Steel Tower Harrison, Abramovitz & Abbe had recently completed the aluminium clad headquarters building for Alcoa Corp. also located in Pittsburgh. Basing themselves on the shape of downtown Pittsburg which is known as ‘The Golden Triangle’ they came up with a triangular floor plan with indented corners rather than the more traditional square or rectangular floor plans in use for nearly all other towers. The Tower still boasts the world record for the world’s tallest building with a completely flat roof.
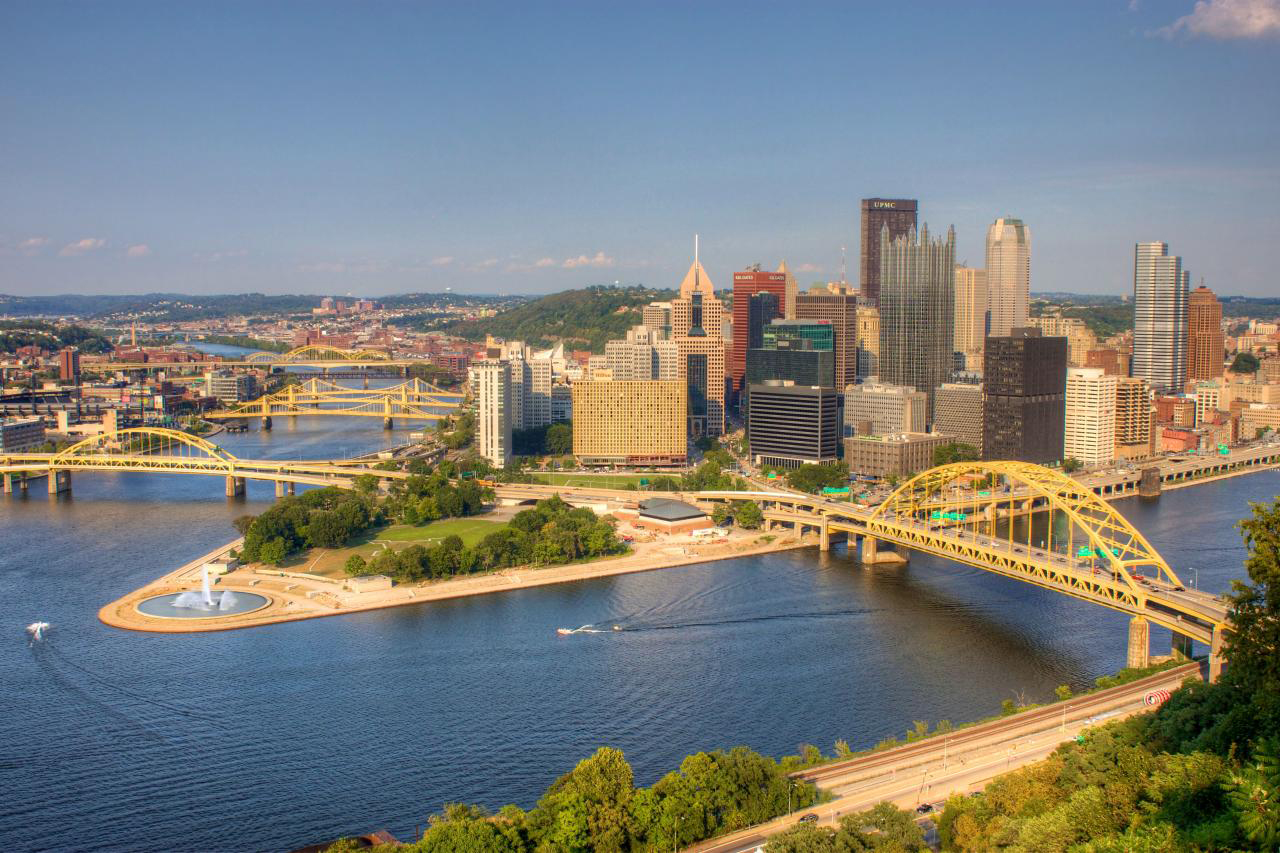
The US Steel building culminates above Pittsburgh’s Golden Triangle, a bustling downtown district located at the confluence of the two main tributaries of the Ohio River
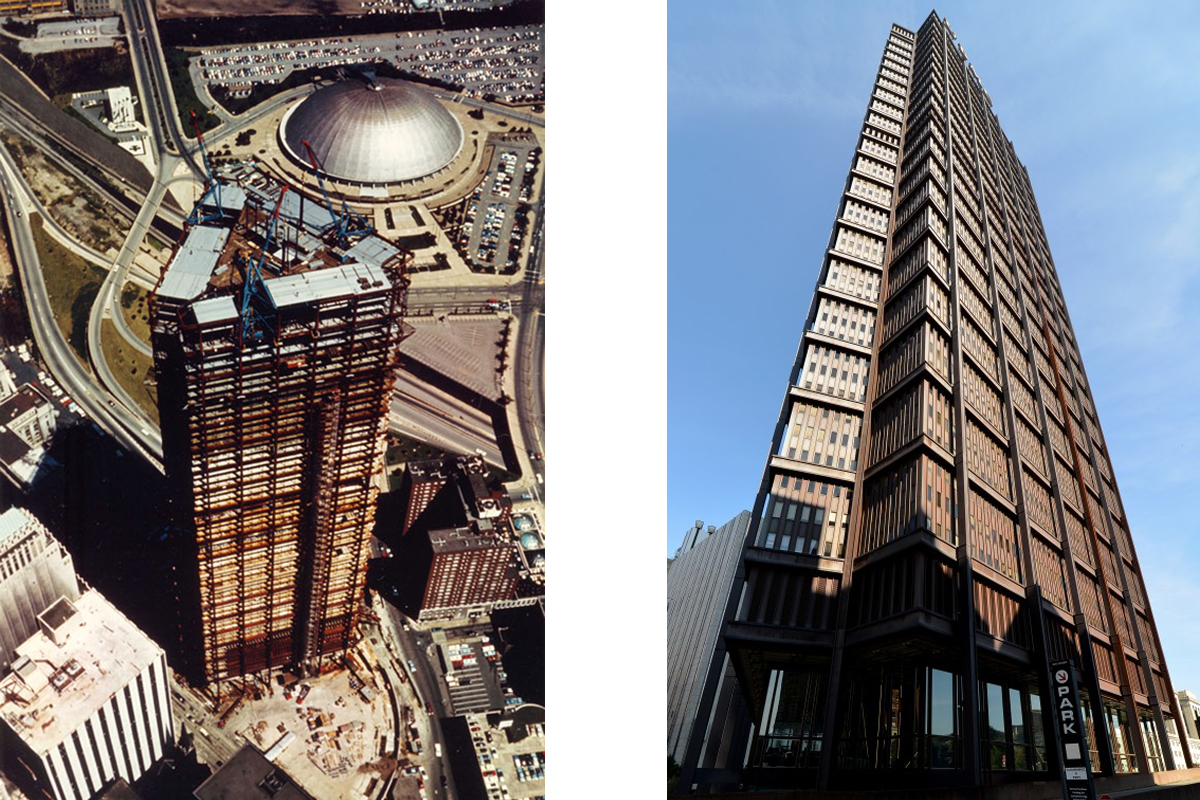
The US Steel building is the tallest skyscraper in Pittsburgh and contains over 44,000 U.S. tons of structural steel, and almost an acre of office space per floor.This aerial view taken during construction reveals its triangular floor plan with indented corners as well as its exterior structural columns
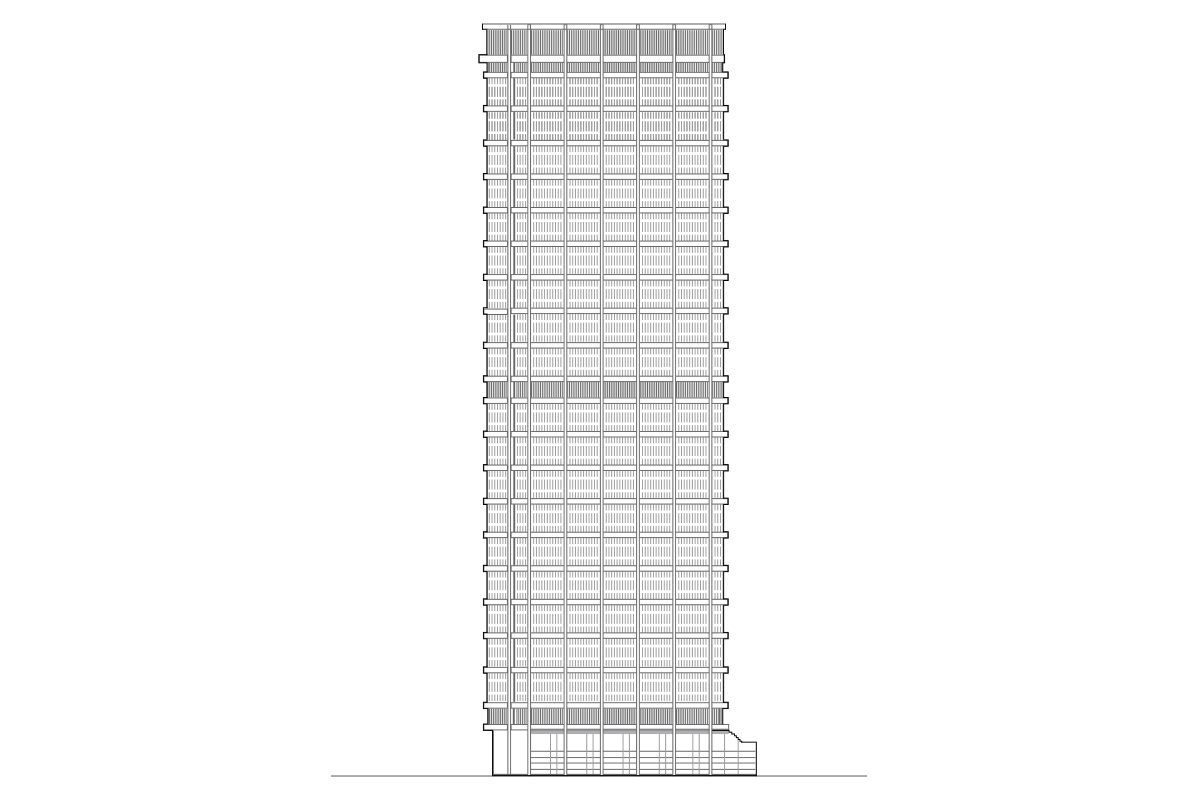
Elevation of the U.S Steel Tower. The US Steel building is 841 ft high (256,3 m) with 64 storeys above ground making it the tallest skyscraper in Pittsburgh. It contains over 44,000 U.S. tons of structural steel and almost an acre of office space per floor.
COR-TEN an innovative steel product both for industry, and the world of art and architecture
U. S. Steel Corporation developed in 1933 a new weathering steel patented as COR-TEN. This steel product was made up of a group of steel alloys which were developed to eliminate the need for painting, and form a stable rust-like appearance after several years’ exposure to weather. Because of its exceptional mechanical resistance Corten was originally intended for rail carts carrying bulk products. The benefits of using this steel was that it did not require painting or expensive maintenance due to rust. Cor-Ten forms a protective layer of dark brown oxidation on its exposed surface and became very popular in industrial product designs. It also gained a lot of attraction in the art world. In 1967 the city of Chicago took possession of a monumental 147 ton sculpture designed by Picasso in Cor-Ten steel. Once the artist had approved the final mock-up, its manufacturing was put out to tender. U. S. Steel won the contract with its bid of $351,959.17 (approximately $2.8 million today) and its fabrication took place in their Gary Works production unit in Indiana.
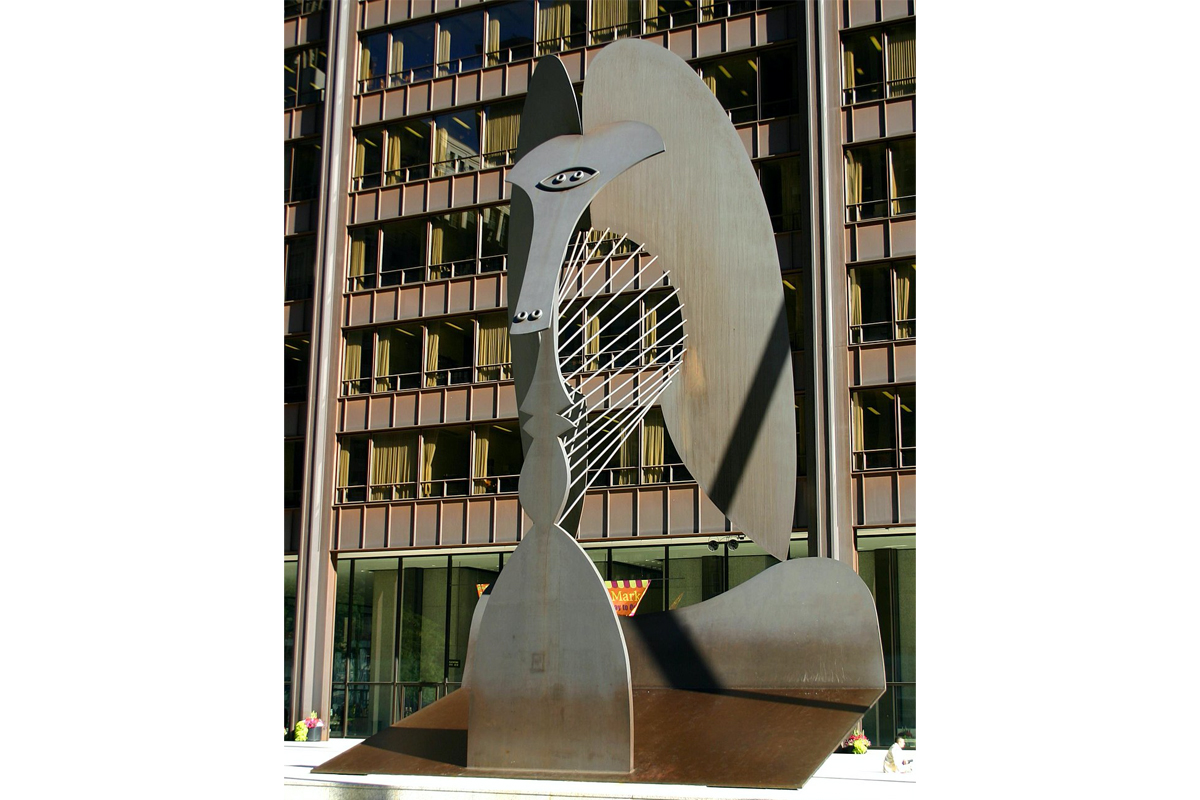
Picasso’s massive Cubist sculpture was designed for the City of Chicago. It weighed 147 tons and was built in Cor-Ten by U. S. Steel in their Indiana production unit.
Photography by J. Crocker
The US Steel Tower project was another opportunity to showcase Cor-ten towards architectural circles. So Harrison & Abramovitz came up with a design that highlighted its steel structure as much as possible. To do so they introduced eighteen structural columns made in Corten on the exterior of the building. Conventionally the structural steel frame of a tall building would have either a concrete coating or would be sprayed with a fireproof coating. Curtain walling would then cover up the structural steel.
To allow the eighteen structural columns to remain visible, the engineers came up with an ingenious solution for the building. They filled the steel columns with half a million gallons of water mixed with antifreeze. This approach to fireproofing columns was common in bridges. Using the liquid-filled columns meant that the entire structural steel frame had to be perfectly watertight and leakproof.
From a rusty dinosaur to a lasting icon
Unfortunately the U. S. Steel Tower was completed just before the first oil shock occurred in 1973 marking the slow decline of the US steel manufacturing industry. In 1989 after a bitter strike, U. S. Steel shut three of their steel manufacturing plants, firing 3 500 union positions. Globalisation accelerated the demise of heavy industry so that the thriving ‘Factory Belt’ gradually became known as ‘The Rust Belt’ leading to massive changes in demography and socio-economic conditions. By 2001 U. S. Steel’s market share had fallen to 8% of domestic consumption. Nowadays the corporation employs approximately 29,000 people with a market value of $1.1 billion.
To make matters worse, the giant rusty steel tower seemed to highlight exactly the wrong quality of steel to immortalise. It didn’t help either that the Cor-Ten steel columns started flaking off tiny bits of iron oxide in the rain – as if a dying industry was crying over its imminent death. The rust then stained the sidewalks around the building into the same rusty color as the building. As the next generation of skyscrapers brought color, ornament, distinctive profiles, and well-planned plazas back to the Pittsburgh architecture, the U.S. Steel Tower seemed both haughty and shamefaced by comparison.
But substantive architecture can withstand the fluctuations of taste. Over the last five years some $60 million have been invested into the US Steel Tower particularly in terms of energy efficiency so that it is now the second-largest LEED Silver Certified office building in the world. The building’s spectacular lobby, has been entirely renovated while maintaining much of its restrained detailing in ample glass and exposed structure to become a first class venue. Certain changes have also been made to the interior design to adapt the office space to present day requirements. But the architecture of the building remains as evocative as ever of the 1970s. It remains to be seen if new buildings elsewhere can portray their own historical period as effectively as the U.S. Steel Building still does.
In production from 1959 to 2000 the Mini (originally named the Austin Seven and Morris Mini-Minor) was in production for 41 years during which 5.3 million cars were sold. Last year (2019) the Mini celebrated its sixtieth birthday.
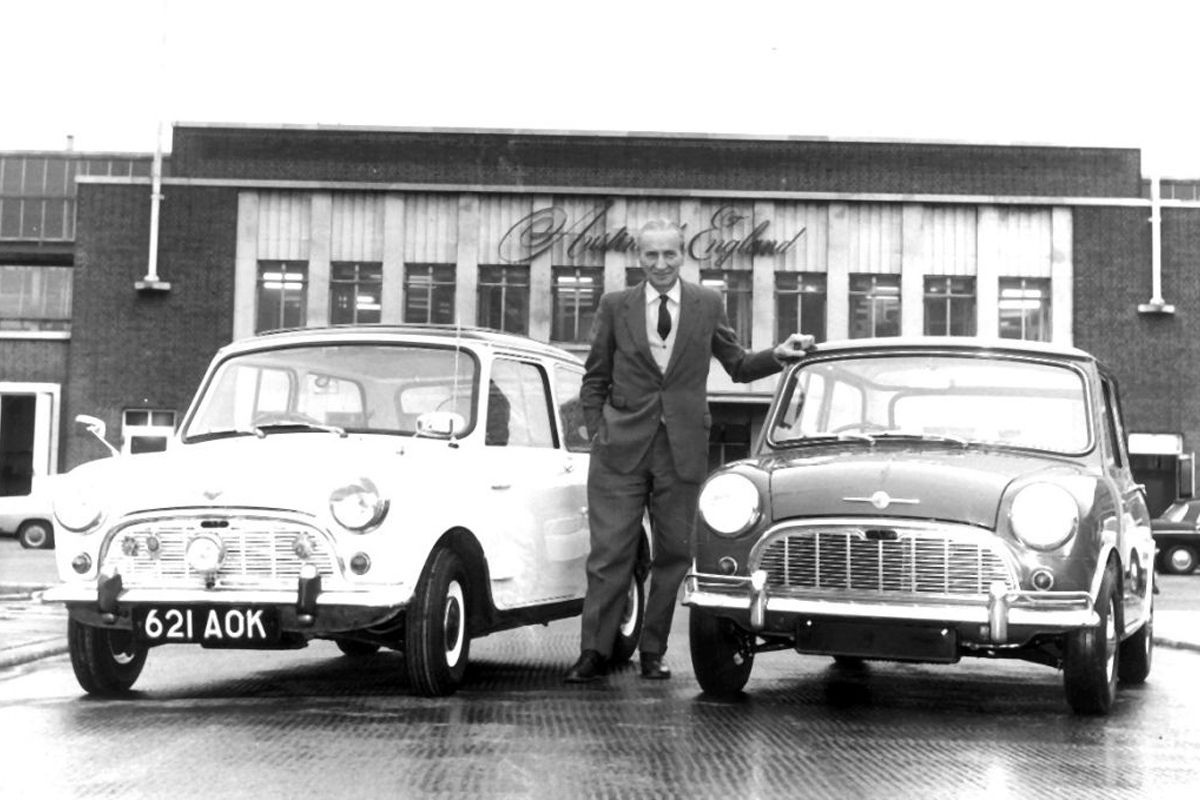
Sir Alec Issigonis at Austin, Longbridge with one of the first Minis (621 AOK) and a 1965 Morris Mini Minor Deluxe.
Sir Alec Issigonis – Background of the Mini Designer
Issigonis was born in 1906 in Smyrna (now Izmir, Turkey) when it was part of the Ottoman Empire the Issigonis family moved to England in 1922 after the British were exiled from Turkey.
Issigonis’ father was a successful shipbuilding engineer of Greek origin but with a British passport. His mother, Bavaria was said to have been related to Bernd Pischetsrieder, director at BMW and Volkswagen. Sadly, Issigonis’ father did not survive the journey from Smyrna to England.
Issigonis like his father had dreamed of becoming an engineer from a very young age. He studied engineering and excelled at mechanical drawing but struggled with the mathematics, failing the exam three times. After a number of jobs, he worked at Morris in the Engineering Department where he had his first success with the Morris Minor. After the Morris and Austin merged to create the British Motor Corporation (BMC) Issigonis decided to leave the company where he later returned after a discontinued project at Avis.
The Mini Concept
The change in political landscape at the time and the oil crisis of 1956 (and fuel rationing nationally introduced) sparked something inside Issigonis and the challenge to prove himself was set. He tasked himself to design a car with seating space for four, great driving characteristics, affordability and high fuel economy whilst maintaining a lot of interior space and a minimal outer dimension.
The Mini was Born!
By this time Issigonis had the experience and confidence to achieve his ambitious goal of a car for the people. With the success of the Morris Minor in the 40s and his background in motor-racing in the 30 and 40s he and his design team set to work on creating something new. Originally known as XC/9003 project ADO15, the small-town car was one of three models being designed and developed but due to the fuel crisis the production was pushed forward on the smallest of the three (the Mini).
With some urgency, Leonard Lord (1st Baron Lambury and captain of BMC) wanted the car moved to production as quickly as possible. By August 1959 the Morris Mini Minor / Austin Seven (later referred to as just Mini), was launched.
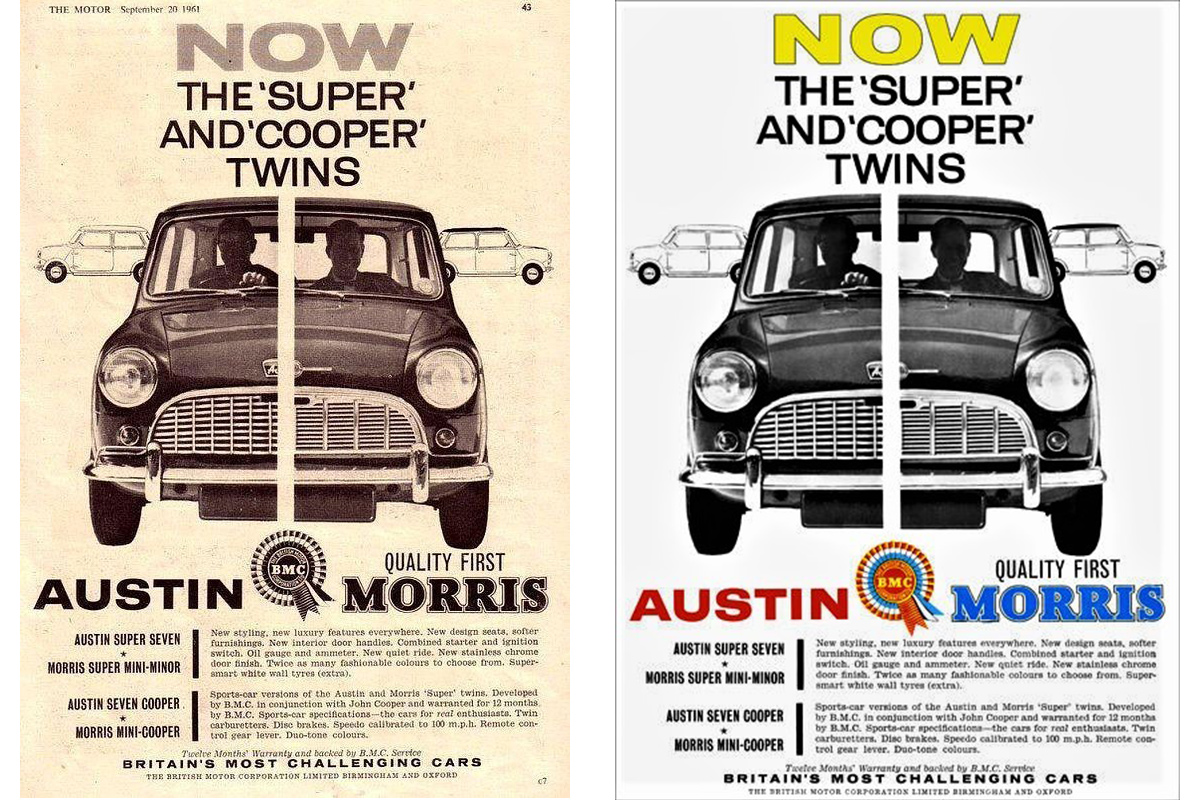
A pair of Mark I adverts for the Austin Seven and Morris Mini-Minor from 1961.
The Mini’s Initial Success
By 1960 the reputation of the Mini had started to gain traction and by 1961 it had so much success Issigonis was promoted to Technical Director of BMC. His contemporaries gave him the nickname ‘The Greek god’ due to the Mini’s overnight popularity. After the initial success production was started on a two-door van, two-door pickup, convertible coupe and Mini Cooper ‘s’ (sport model).
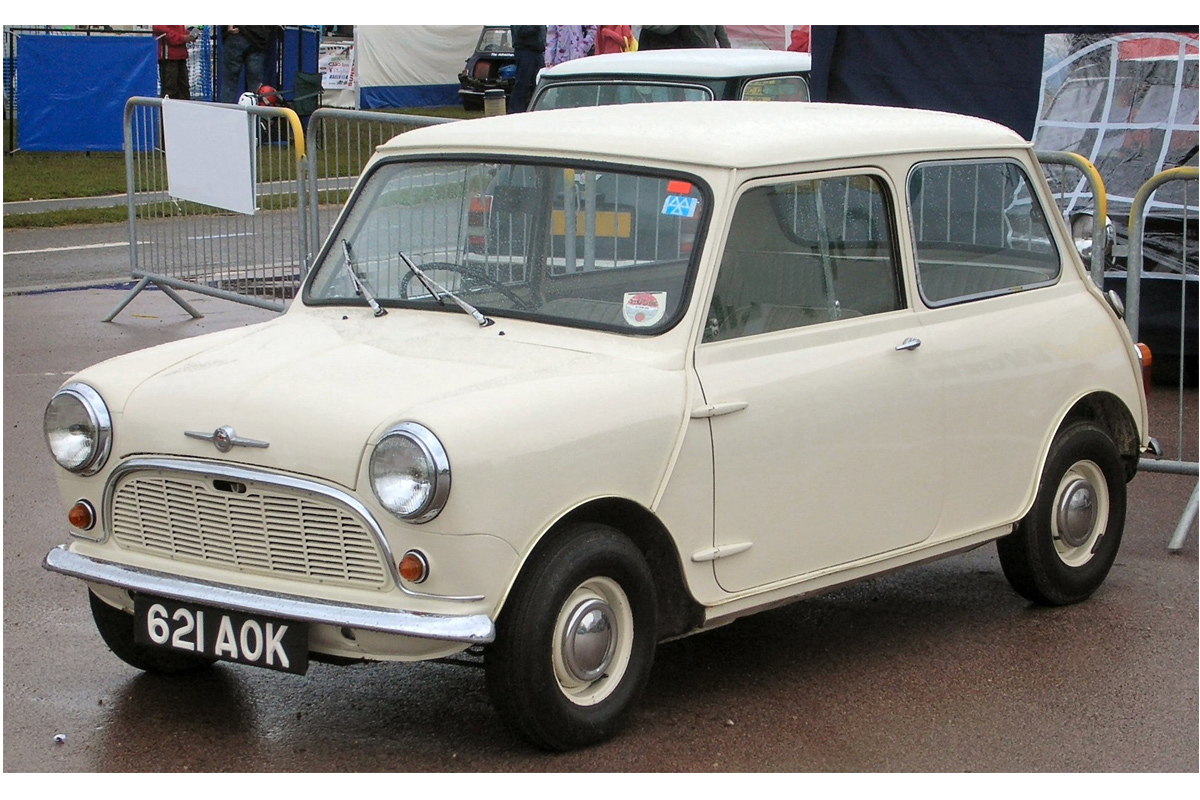
One of the first Minis from 1959 with 10 inch wheels, Mark I & II grille and door hinges. This is the same car Issigonis was photographed with outside the Austin, Longbridge plant.
Original Design
The design and the popularity of the Mini came down to a number of factors. The space saving transverse-engine and gearbox kept the package and footprint of the car compact (this concept has remained standard for small front-wheel drive cars to this day). Although this engine layout was not new it was very uncommon at the time.
The need for the car to be affordable and to save cost wherever possible impacted the design and paved the way to how the Mini looked.
Door Hinges and Welding Seams
The door and boot hinges were mounted externally. This made production of the car easier and cheaper as well as keeping the doors thin by only being single skin. Welding seams clearly visible down the A & C pillar, body and floor pan saved on assembly time and cost.
Sliding windows instead of conventional roll-up
The sliding windows allowed for a single skin door which reduced door bloating within the car’s interior space and increased elbow room. Both the window style and door hinge only appeared on these first two marks due to customer demand for winding windows.
“Smaller” Ten Inch Wheels
The ten inch wheels were more affordable and specialist tyres had to be developed by Dunlop, although a suggestion of eight inch wheels were conceptualised the idea was rejected by Dunlop.
Storage Bins
A bracing bar across the single skin doors was later reworked to create large storage bins on each door. Issigonis later said that he had sized the bins to carry the ingredients of his favourite drink, a dry martini in the correct proportions (one bottle of vermouth and two bottles of Gordon’s Gin).
Similar bins were added later to the rear seats with dual function to support the single skin body and provide more storage. When originally sold the initial Mini had optional wicker baskets to store small items under the rear seats.
Boot Capacity
The fixed rigid parcel shell supported the body and the boot. The boot has hinges at the bottom so the car could be driven with the it open, increasing the storage capacity. The number plate was also hinged so it would still be visible in this circumstance.
Ease and Cost of Production
The production required minimal JIG work, the external seams made it almost self-aligned and allowed the panels to stack on top of one another. This made it easy to ship and accessible for overseas markets and included countries with only basic industrial capabilities.
All of this combined allowed for the shell and body of the car to be incredibly thin, the pillars were small allowing full visibility. The storage buckets, parcel shelf, and under-seat space meant that you could get a lot in the car before the car began to feel cramped.
Issigonis had achieved his brief of creating a small car that seated four that was fun to drive, economical and functional all for the price of £496 (£11,498 in 2020).
Simplistic and Minimal
To save on cost and weight the Mark I and II Mini didn’t come with a radio, heater or anything extra.
Original Design flaws
Although well designed the original Mini did have some drawbacks.
- The steel was prone to rusting
- The original suspension cones were not as Issigonis intended and were a quick substitute due to time limitations
- The radiator was not in the optimal position
- The radiator fan was off the end of the block to cool the radiator causing all the ignition to be placed behind the grille where it was exposed to the rain and weather.
Mini Design changes over the 41-year production
Over the course of its production the Mini has relatively remained unchanged. The Mark III saw enough body change that the car was issued a new factory code from ADO15 to ADO20 which included concealed door hinges and windows that wound (due to customer demand). From April 1974, a heater was standard.
The Mini design is so iconic that in the 90s, Rover Group (heir to BMC), were able to register its design as a trademark in its own right.
Cosmetically on the outside the Mini remained the same after the Mark III. The only changes were based on functionality (flared wheel arches for wider wheels, engine mounting points being moved for the larger 1275cc engine).
The interior became a different environment with the shelf like dash being replaced with a more traditional flat facing concealed dash with glove box. The biggest change for the interior was during the 90’s Rover production, where most of the interior was lifted from one Rover or another.
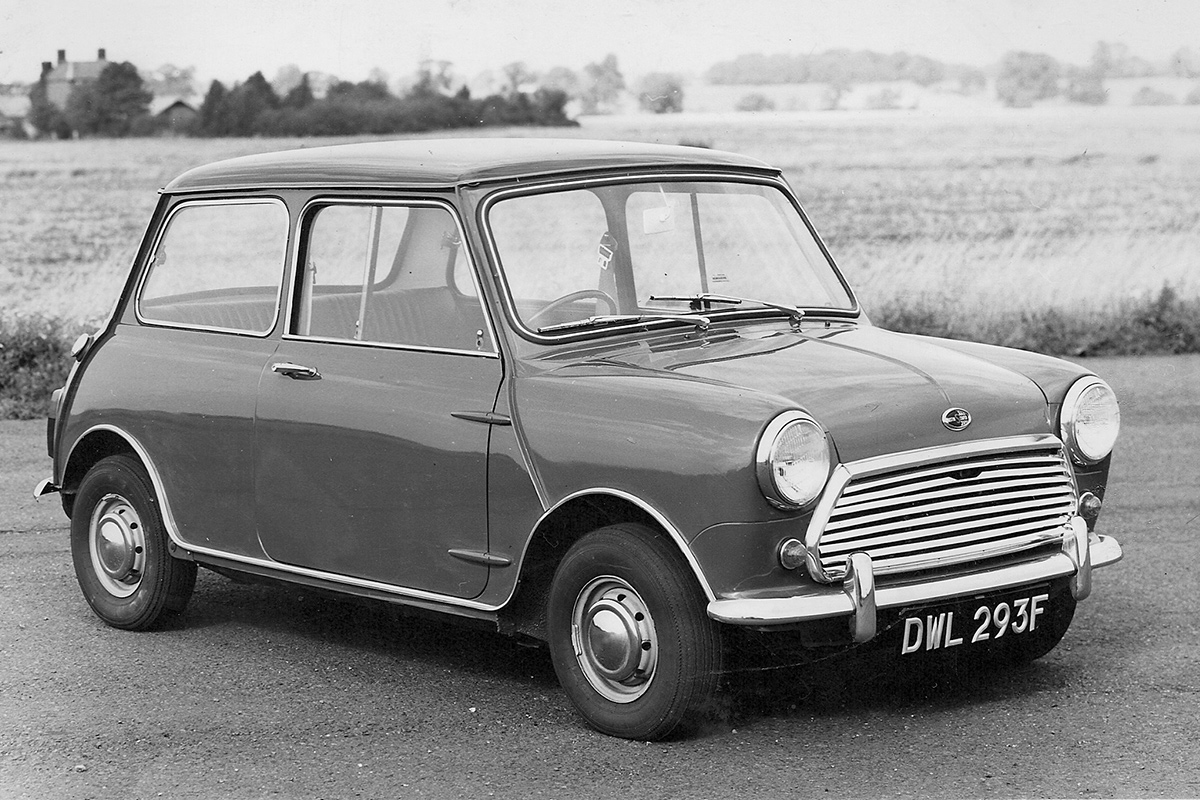
An Austin Mini Cooper ‘s’ Mark II Mini, 1275cc outputting 76 bhp with Hydrolastic suspension prior to its launch
Racing Pedigree and Cult Following
Not long after its initial release the car gained a cult following. This was initially lead by John Cooper. With a background in designing F1 cars and a friend to Issigonis, Cooper saw the potential for the Mini to be more than a Small-Town car. Issigonis, who was not convinced on the car being used for performance didn’t agree with Cooper, forcing Cooper to appeal directly to BMC management to get permission on the performance model. Both Issigonis and Cooper began working together on modifying the Mini for race!
In 1963 a more powerful Mini Cooper was launched, named the Mini Cooper ‘s’. This model featured a 1071cc (initial ‘s’ models were 848cc with a long stroke to increase it to 997cc) engine with larger 70.61mm bore, larger servo assisted brakes and a longer stroke to increase displacement. A pair of SU carburettors helped increase power from 34 to 55 horsepower. On top of engine performance, the Mini was given a close-ratio gearbox and front disc brakes (uncommon at the time).
These sporty upgrades lead to the Mini winning a number of races including the Monte Carlo Rally in 1964, 1965, 1967. Techincally the Mini won in 1966 but was disqualified controversially due to the headlights being against the rules (the Minis were fitted with non-dipping single filament quartz iodine bulbs in their headlamps, in place of the standard double filament dipping glass bulbs).
To this day the Mini competes in classic racing and the interest and momentum is only growing as time goes on.
The Original Minis Future
Although into its 60s the Mini can still be spotted regularly. With thousands, still on the road it brings warmth, happiness and nostalgia for many. Its original design was practical and accessible leading to its success and cult following.
With so many Minis around and the enthusiasts keen to keep them going the original Mini has evolved. With owners customising and personalising them visually and mechanically. From custom paint colors, unique interiors and other aftermarket features to completely different engines many Minis have become more of a statement and extension of the owner’s personalities and taste.
This expression is far beyond the original functional purpose they were designed for but a resounding statement of how good design allows people to become creative themselves.
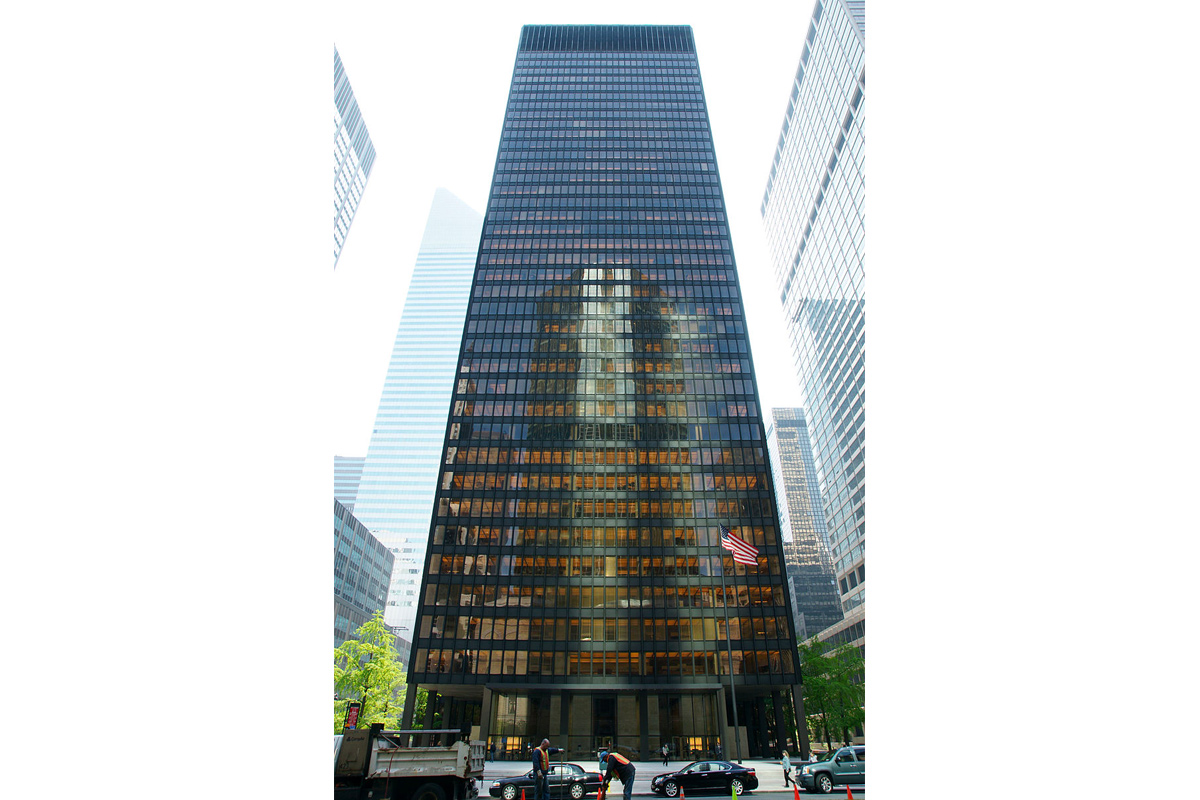
Built in 1957 the 38 story Seagram building designed by van der Rohe hailed in the Modernist style to the US and set the standard for office towers around the world. Photography by Noroton.
Delving into the roots of the building’s modernist design
Functional/Modernist architecture was a style of design that first emerged through the Bauhaus movement founded by Walter Gropius in Germany in 1919. The design innovations commonly associated with Gropius and the Bauhaus—the radically simplified forms, the rationality and functionality, and the idea that mass production was reconcilable with the individual artistic spirit—were already partly developed in Germany before the Bauhaus was founded. The original modernist buildings were typically industrial. The Fagus shoe factory, constructed in 1911 in Alfeld on the Leine,Germany is considered by many to be the first modernist building in the world. Designed by Walter Gropius and his partner Adolf Meyer the Fargus building has been designated as a UNESCO World Heritage Site. In this beautifully simple building, you can already see the roots of future modernist skyscrapers, including the Seagram Building.
Mies van der Rohe subsequently took over from Gropius in 1930 before the school in Berlin was closed in 1933 by the rising Nazi regime. When the staff reluctantly emigrated from Germany the ideas of the movement began to spread like wildfire in Europe and America. In 1937 Mies van der Rohe moved to Chicago where he was appointed head of the department of architecture at the Illinois Institute of Technology (IIT)
How Modernist principles blended into American architecture
At the turn of the twentieth century a first Chicago School of architects were among the first to promote the new technologies of steel-frame construction in commercial buildings, and develop a spatial aesthetic which evolved in parallel with European Modernism. It led to the construction of a number of high-rise buildings both in Chicago and in other cities across the US. However these tall buildings still kept elements of neoclassical architecture such as cornices and bay windows projecting out onto the street (oriels). The work of Mies van der Rohe amplified this modernist movement which played a seminal role in shaping modern American architecture right up into the 1970s.
During his academic and professional experience Mies van der Rohe had selectively adopted ideas from Russian Constructivism for “efficient” sculptural assembly of modern industrial materials. Van der Rohe also picked on the ideas of the Dutch De Stijl group in the use of simple rectilinear and planar forms, clean lines, pure use of color, and the extension of space around and beyond interior walls.
His early projects at the IIT campus presented to Americans a style that seemed a natural progression of the almost forgotten nineteenth century Chicago School style. His architecture, with origins in the German Bauhaus and western European International Style, became an accepted mode of building for American cultural and educational institutions, developers, public agencies, and large corporations.
It was Phyllis Lambert, the daughter of CEO and owner of Seagram Samuel Bronfman who commissioned the Seagram Building on behalf of the Canadian spirit brewer, Joseph E. Seagram & Sons.
A flagship project for the design of office buildings worldwide
The Seagram project was Mies van der Rohe’s first tall office building, and his design set the standard for office towers around the world. It was designed by Rohe to look elegant and to demonstrate the wealth of the owners very clearly. For this flagship project he left aside the modernist principles of using cheap mass-produced materials to build the most expensive tall towers at the time. Upon its completion in 1958 the building costs amounted to $41 million. That was a colossal amount which equates in today’s money to around $328 million. A large proportion of that budget was spent on the building’s interior design which included lavish materials such as granite, marbles and bronze.
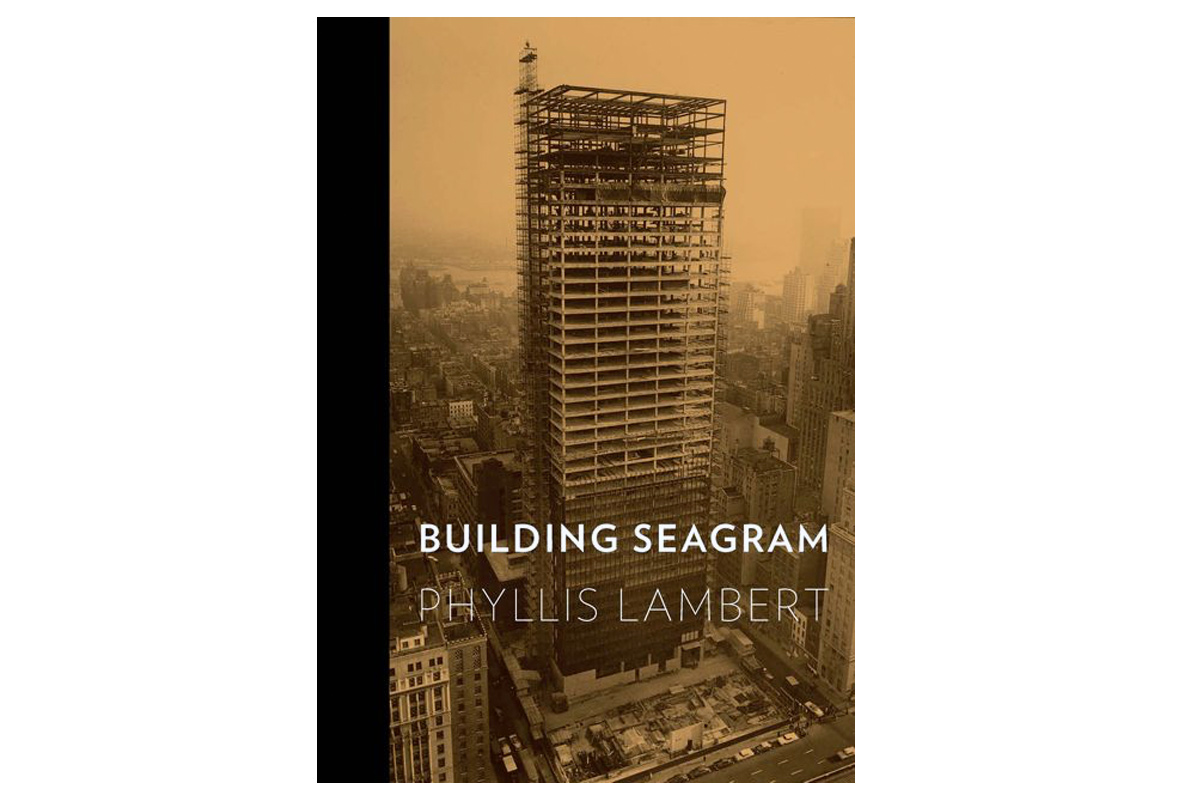
This photo of the Seagram Building, taken in December 1956, under construction reveals its steel and concrete structure (cover photo of the book “Building Seagram” by Phyllis Lambert)
This 38-story building 515 feet tall (157 meters) has a typical steel structure combining a steel moment-resisting frame with a steel and reinforced concrete core for lateral stability. Poured concrete is used to make up the floors while concrete core shear walls extend up to the 17th floor. Further diagonal core bracing (shear trusses) extends to the 29th floor. Van der Rohe also specified bronze outside the building which enhances the grey glass used in the curtain wall. Although the bronze seems to be a structural component when you look at the building from outside in actual fact, its purpose is purely decorative.
A lasting legacy for modern urban planning
Another distinctive feature is how the building was placed within the construction area. Whereas most contemporary buildings used the whole building plot, Van der Rohe set his client’s building back by about one hundred feet from the road. This decision completely overturned the financial modelling in skyscraper construction. Setting structures back from the street made the built environment friendlier for city dwellers. They freed up land surface for a plaza or public open space and allowed the streets below to gain natural daylight.
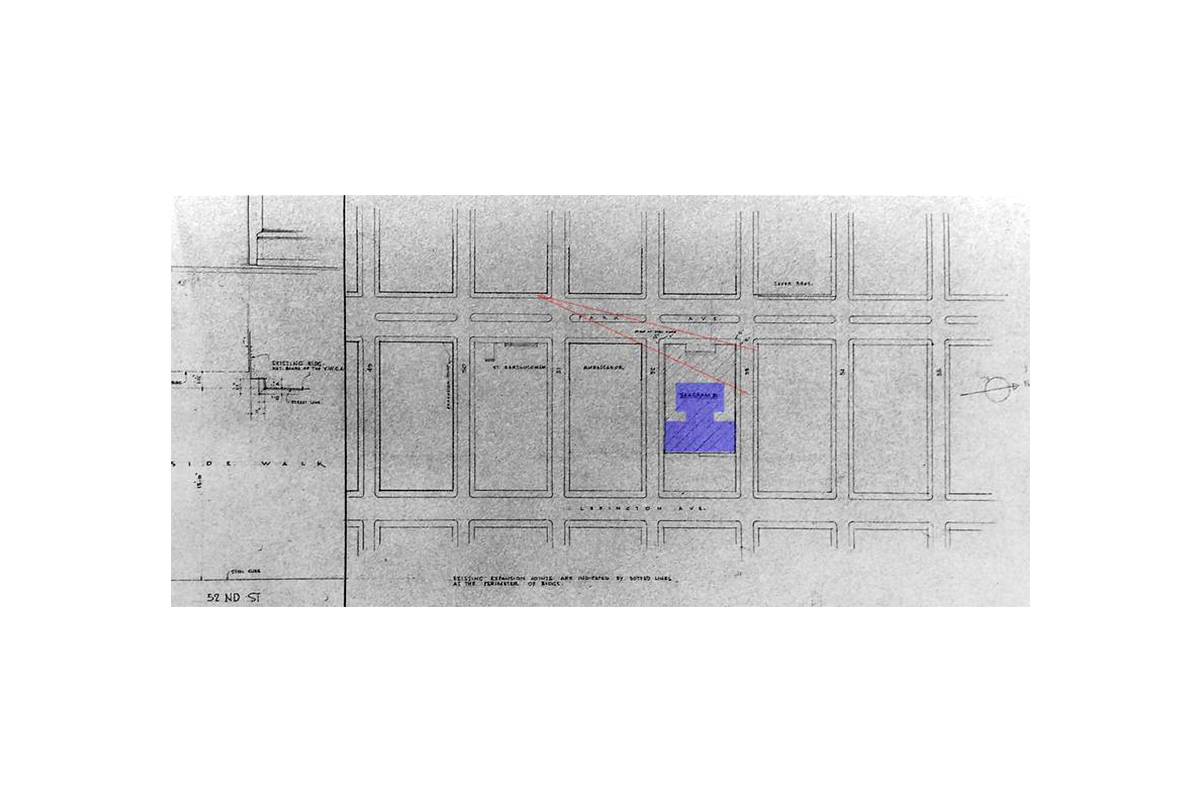
This original site plan shows that by setting the Seagram building back from the street and using only part of the building plot Van der Rohe created a precedent that was to mark US urban planning thereafter
Set back from Park Avenue, van der Rohe created a large, open granite plaza which remains a very popular gathering area to this day for office workers in NYC. There is also a set of fountains to highlight this iconic building which was bought in 2000 by Aby Rosen, the West German-born property investor for $375 million.
In 1961 the city of New York was enacting a review of its zoning laws. It brought in incentives to allow developers to include privately owned public spaces into their projects. This new zoning directive builds on the successful experience of the Seagram project. Over the years it has led to the creation of new plazas and landmarks throughout NYC such as The Hudson Yards, where Thomas Heatherwick built in 2019 The Vessel, an extraordinary structure of connected stairs in the shape of a honeycomb. To conclude the Seagram building has left a lasting legacy both in architecture and urban design.
Kem Weber (1889-1963) was a German-born architect and furniture designer. His birth name was Karl Emanuel Martin Weber but in 1914, he changed his first name to a less German-sounding, ‘Kem’ when he became stranded in the USA after the outbreak of the First World War.
Kem Architecture was part of the West Coast Modernist movement in America. His designs included many projects and products in Streamline Moderne, a form of Art Deco design and architecture that was very popular in the USA and Europe in the 1930s. This style emphasised curved forms and long horizontal lines; it was the epitome of sophistication and modernity in that era.
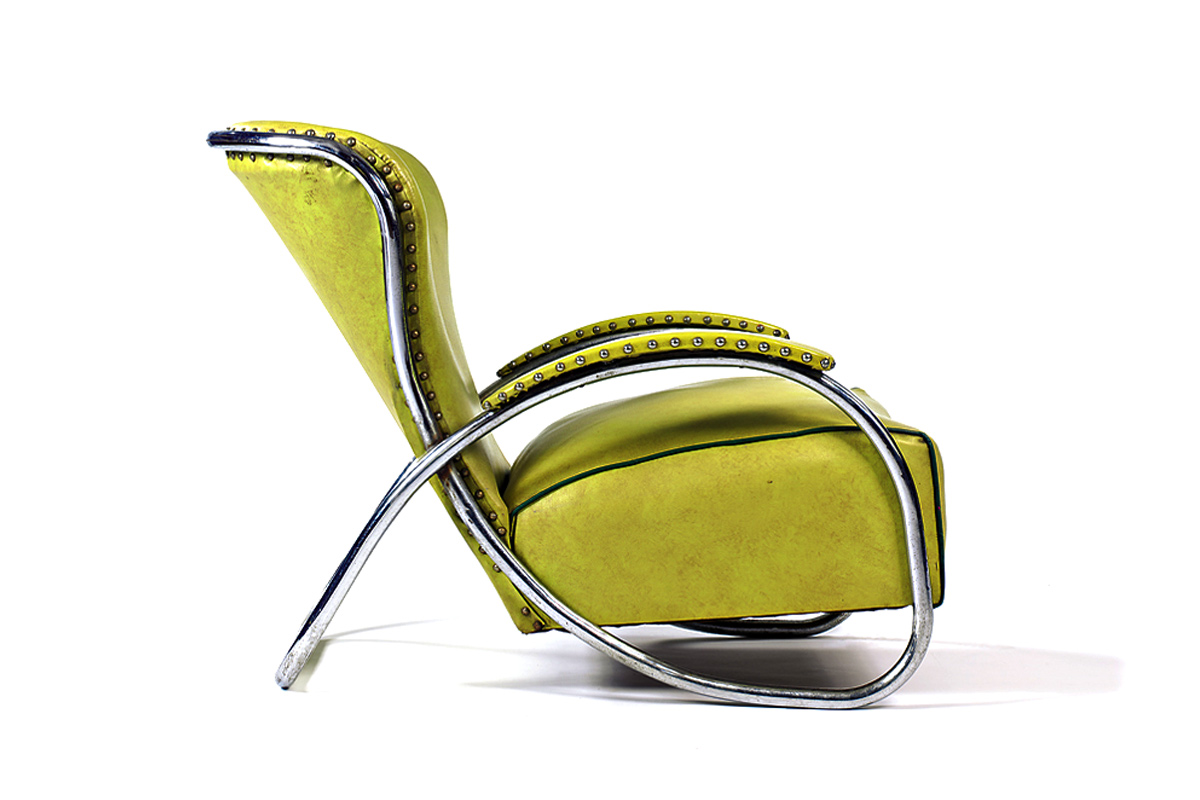
Lounge chair designed by Kem Weber for the Lloyd Manufacturing Company in the 1930s. Weber was known for the use of flowing tubular, stainless steel in his furniture.
Streamline Moderne was used for everything from stainless steel cocktail shakers to high powered steam locomotives. In fact, the railway industry immersed itself in this design school, not only for trains but also for stations.
Weber worked very successfully with many types of companies using Streamline Moderne and utilised different materials in his designs. He was comfortable working with timber, from his time as an apprentice to the royal cabinet maker, Eduard Schultz in Potsdam and he had learnt about stainless steel tube and chrome from Bruno Paul, whom he studied under in Berlin, in the 1920s.
The Zephyr clock
Weber is responsible for two of my favourite designs in Streamline Moderne. One is a clock called the ‘Zephyr’ made by the American company, Lawson Time. The Zephyr clock is very architectural in appearance and one can easily imagine a building like a gas station or an office in the same design. The clock was produced in many finishes such as chrome, stainless steel and a new material called bakelite – the world’s first synthetic plastic.
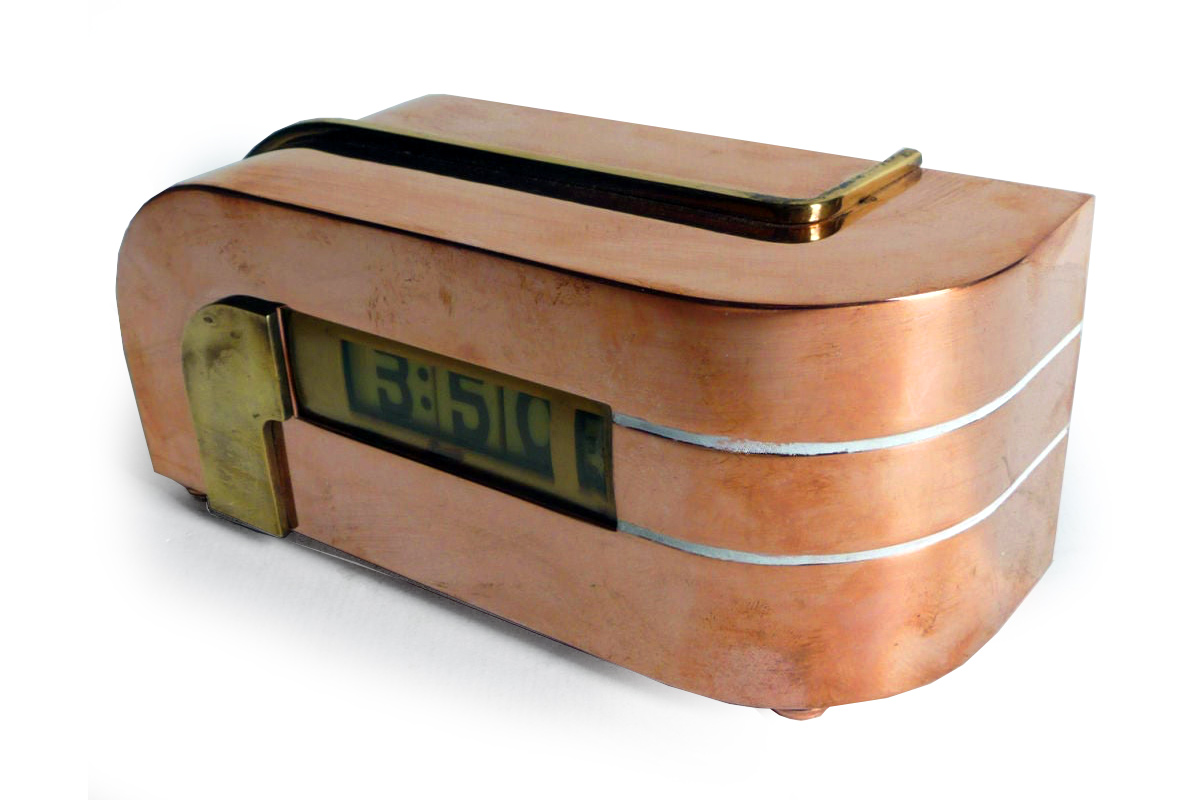
The Zephyr clock by Lawson Time. It was designed by Kem Weber in the Art Deco style known as Streamline Moderne and operated with an electrical movement by Westinghouse.
Photography by 1stdibs.com.
The word, ‘Zephyr’, refers to a gentle breeze from the west or soft light fabrics and was a popular name for many state-of-the-art products in the 1930s. Its connection to lightness made Zephyr an ideal name for anything modern and lightweight compared to older heavier products.
Pennwood Electrical Movement
The Zephyr clock used the remarkably complex, Pennwood Electrical Movement, which allowed manufacturers to produce accurate, electrical, digital clocks. Westinghouse fabricated this mechanical movement in their factory for Pennwood, and they claimed it to be mechanically perfect. This movement did not need a clock face and also dispensed with the traditional hour, minute and second hands. This was a big selling point for Lawson who did not even use the word ‘clock’ to describe their product; instead they referred to their products as timepieces or advanced time recording pieces. The price reflected the new technology – a midrange Zephyr clock was a hefty $27.50 or $506 in today’s money.
The Airline chair
Weber was hired by Walt Disney in 1938 to be the chief architect of the Walt Disney Studios in Burbank, California. He was also commissioned to design all of the furniture inside the building, working closely with Walt Disney on the project. One of the products he supplied, and another design I much admire, was the ‘Airline’ chair which he had created in 1934.
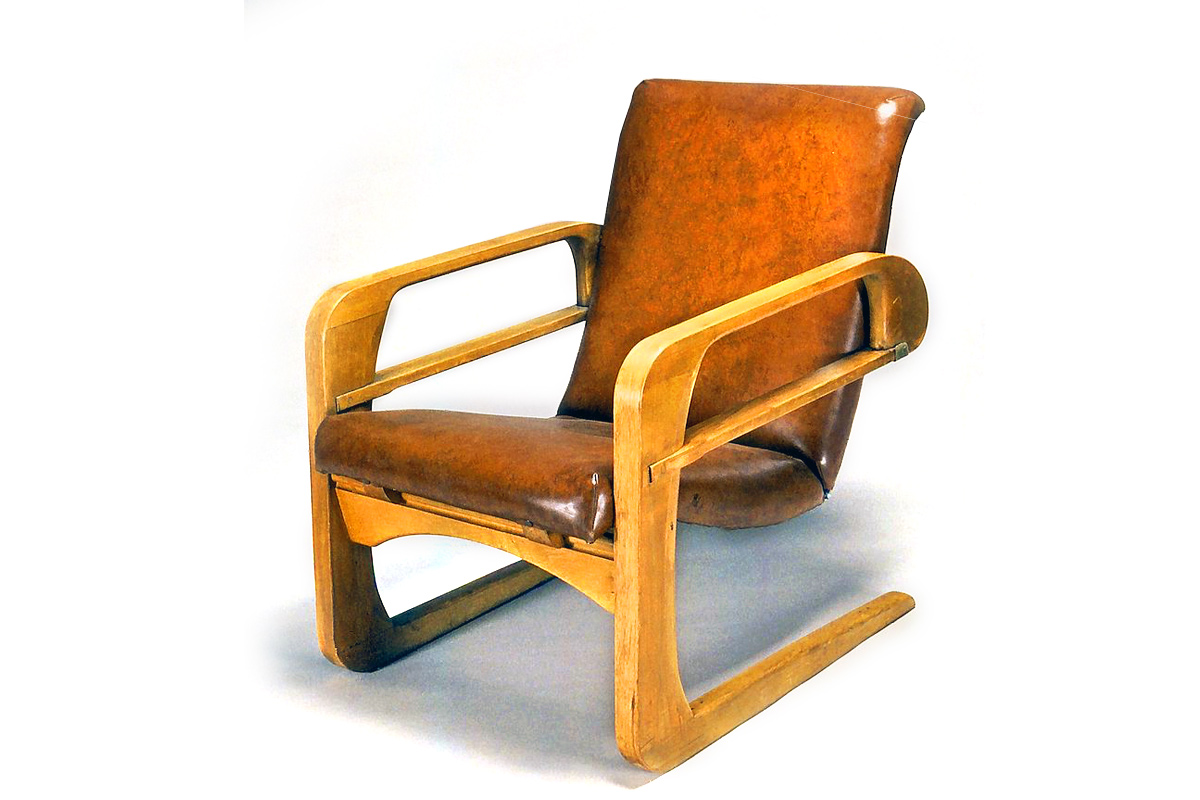
Airline chair with wooden frame and caramel-colored Naugahyde cushions. It was designed by Kem Weber in the 1930s and supplied to the newly-built Walt Disney studios.
The name was contrived to link the chair with the most advanced technology in the world – the aerospace industry – and was, in Weber’s words, ‘comfortable, hygienic, beautiful and capable of being inexpensively produced.’ The cantilevered design dispensed with the rear legs to give the user a very comfortable sitting experience and was available upholstered in either leather or PVC.
The Airline chair was an early example of flatpack furniture and many people believed that this feature and its stunning design would produce an enormous commercial success.
Sadly, Weber could not reach an agreement with a major furniture manufacturer and only 300 of these chairs were produced, all for Walt Disney.
Seattle, Washington, USA. 47°36′35″N 122°19′59″W
“In 1998, Seattle voters approved the Libraries for All bond issue, which provided for replacement or upgrade of all the branch libraries as well as a new Central Library. The International Style library building at 4th Avenue and Madison Street opened in 1960 and after almost 40 years of service, was at the end of its useful life. Koolhaas won a bid competition in May 1998 to submit a design for the new building.” – David Wilma (historylink.org/File/4163)
Seattle is known for being one of the cities with the most well educated population in the United States and it hosts an array of Fortune 500 companies such as Microsoft, Amazon, Boeing, Expedia or Starbucks. This fact remarks the kind of society that embraced such a daring idea. Each tribe selects its totems.
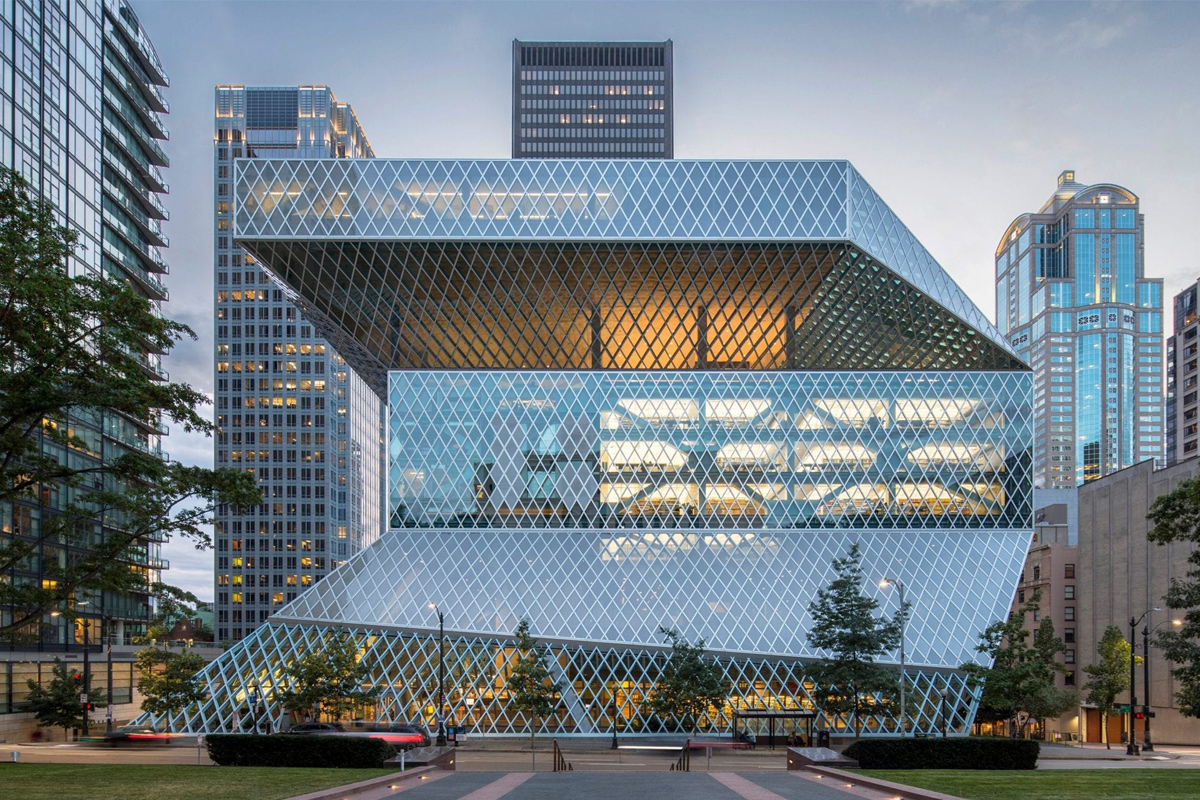
Seattle Central Library. Architects: OMA (Rem Koolhaas + Joshua Prince Ramus) and LMN Architects. Front elevation of the building where the cross bracing steel structure is seen behind the glass facade. The complex geometry responds to the local conditions such as views, orientation and urban density.
Image by Hoffman Construction Company.
An extraordinary building usually happens at a certain time at a certain place.
The 1990s and early 2000s were years of global economic bonanza and brought a handful of architecture masterpieces. Most of them followed the principles of the deconstructivist train of thought that most renowned architects were experimenting with at the time. Frank Gehry delighted us with the Guggenheim Museum in Bilbao; Zaha Hadid broke into the built architecture scene with the Vitra Fire Station; FOA designed and constructed Yokohama Ferri Terminal. My favourite of them all was the Seattle Public Library by OMA – Rem Koolhaas and Joshua Prince Ramus – in collaboration with the local firm LMN. I remember spending countless hours studying the plans, sections and diagrams that were published while developing my own final thesis project back in 2006.
The project was the result of an international competition that took place in 1998. It attracted 29 proposals from local, national and international offices. OMA won the commission among the five finalist teams that included Norman Foster, Cesar Pelli, Steven Holl and the Portland-based firm Zimmer Gunsul Frasca.
The concept behind the glass skin
Like all inventions, nothing is completely new. Every innovation is an evolution of a previous idea and in order to develop the concept of the library, Koolhaas rummaged into his obsession with Manhattan’s congestion and its skyscrapers. He took it as a starting point for the design of the library. According to him a skyscraper is a sequence of stacked floors on which anything can happen and functions can freely alternate from one floor to the next. This is exactly what happens in the Seattle Public Library.
The team of architects studied thoroughly the extensive brief of the library and decided to group functions according to their nature. They concluded that there were two types of programme functions: the stable ones, which required stable conditions and did not imply movement in themselves; and the unstable ones that were mainly spaces where any kind of exchange and movement could happen.
Those stable functions included the headquarters of the library, the book storage, meeting rooms, staff offices and the carpark. The unstable functions which imply a greater amount of movement of people across them were spread across the section of the building, placed above and below the floating boxes.
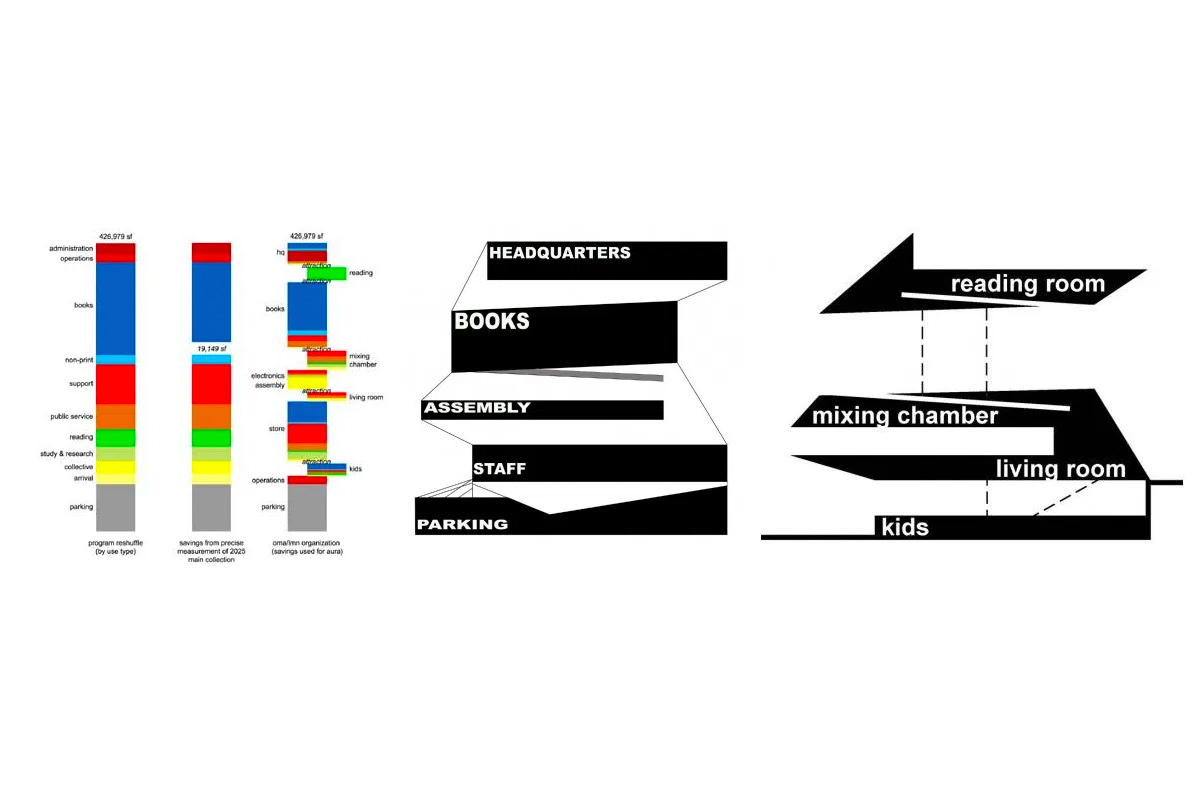
Seattle Central Library. Architects: OMA (Rem Koolhaas + Joshua Prince Ramus) and LMN Architects. Concept drawings showing a blocks diagram exploring the relationships between different parts of the programme and its direct translation into a section diagram of stacking boxes in space.
The diagrams as a design tool
Diagrams had been used in the past as a design tool that helped architects tackle complex programs that implied an intricate variety of adjacency relations within the different spaces of a building.
Koolhaas, together with other architects like Peter Eisenman or Bernard Tschumi to name a few, explored the possibilities that diagrams could offer when organising space and generating new spatial experiences by themselves.
Deconstructivist architects, named like this after the exhibition at the MOMA in New York curated by Phillip Johnson and Mark Wiggley in 1988, stretched the possibilities of this tool to the limit and many of their buildings became literal translation of such diagrams into constructed objects.
Loyal to this approach, Koolhaas and Ramus decided to translate the stable parts of the programme into boxes and place the unstable functions in between them.
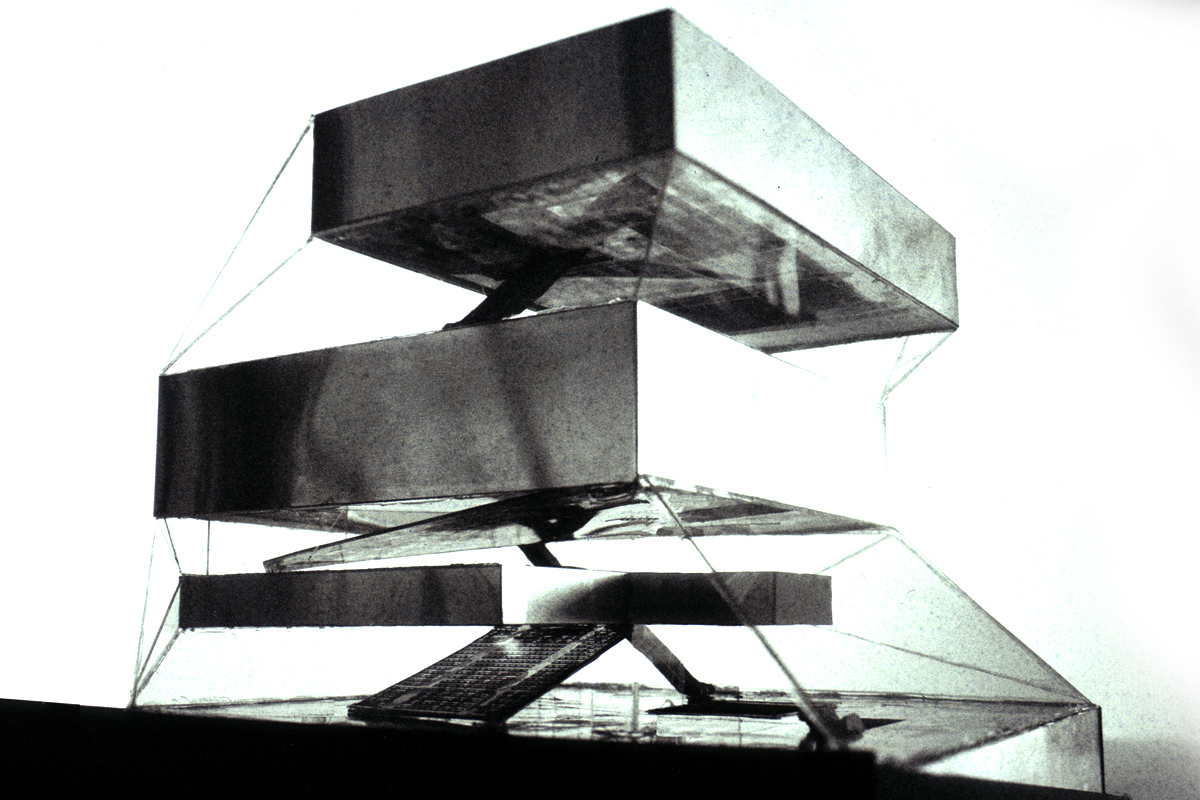
Seattle Central Library. Architects: OMA (Rem Koolhaas + Joshua Prince Ramus) and LMN Architects. Concept drawings showing a blocks diagram exploring the relationships between different parts of the programme and its direct translation into a section diagram of stacking boxes in space.
The clever twist in architectural innovation
The turning point in the design comes when the sequence of boxes are accommodated in the three dimensional space. The boxes occupy different height levels but they also shift position in plan responding to the local and external conditions of the plot: be it the views of the bay, the mountains, the density of the urban fabric around it or the orientation of the building itself. The resulting pile of boxes is then wrapped in a glass and steel skin that encloses the terraced unstable function spaces.
The fact that a complex geometry building was conceived departing from a simple operation of stacking boxes in space is, probably, the aspect of the design that captivated me the most. Those unstable functions such as reading rooms or consultation rooms end up being contained in irregular geometry spaces in between the floating boxes and the inclined planes of glass that wrap them.
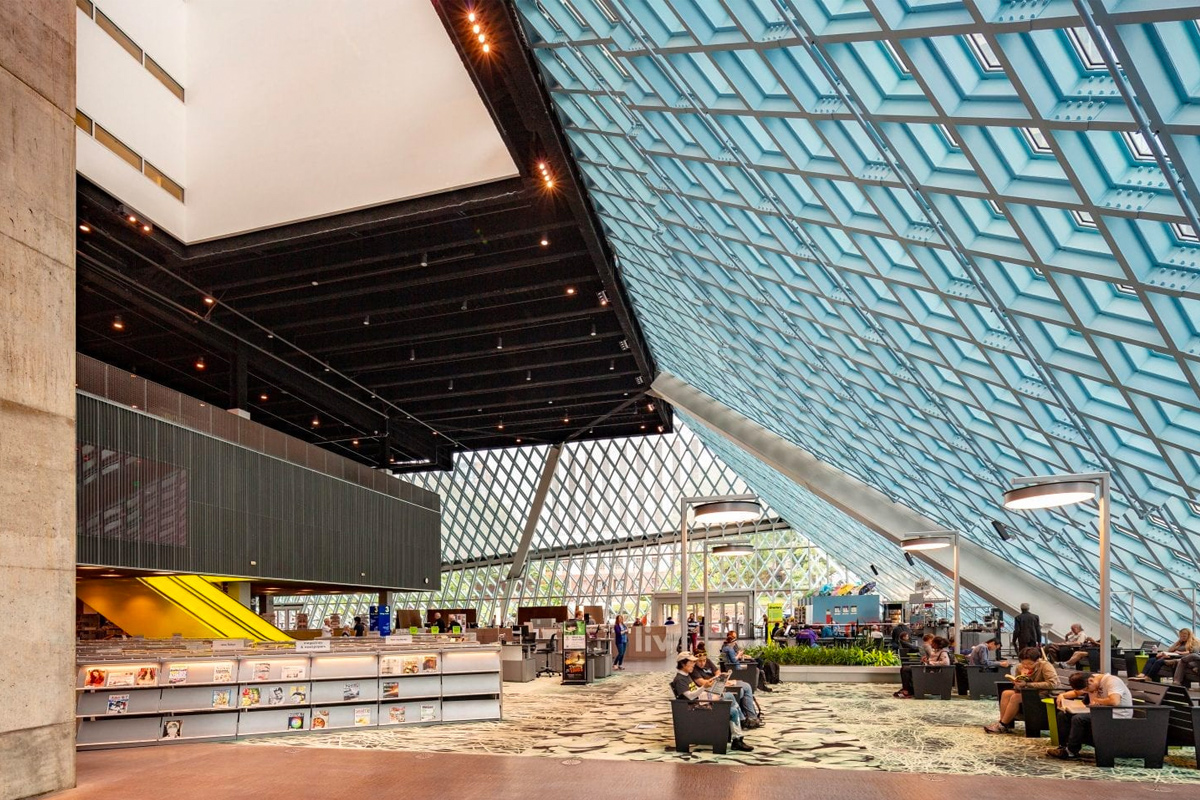
Seattle Central Library. Architects: OMA (Rem Koolhaas + Joshua Prince Ramus) and LMN Architects. Internal view of the lobby-living room. The steel mesh shapes the space of the unstable programmatic platforms of the building. Big size rugs ornamented with vegetal patterns define areas within the space.
Image by Hoffman Construction Company.
Structure
The concept of the structure combines two different systems. A regular grid of columns brings down the vertical loads to the foundations, replicating the free plan structural concept developed by the modernist architects of the twentieth century. The steel cage that wraps the boxes in space, defined as a diagonal mesh, will take the horizontal loads and stabilize the building against wind or seismic events. The skin of the building becomes its image but also its structure, and it does so in an uninhibited way. The steel elements change in size, density, orientation or even double up explicitly depending on the loads they need to resist. The structural stress diagrams become part of the aesthetic expression of the architecture.
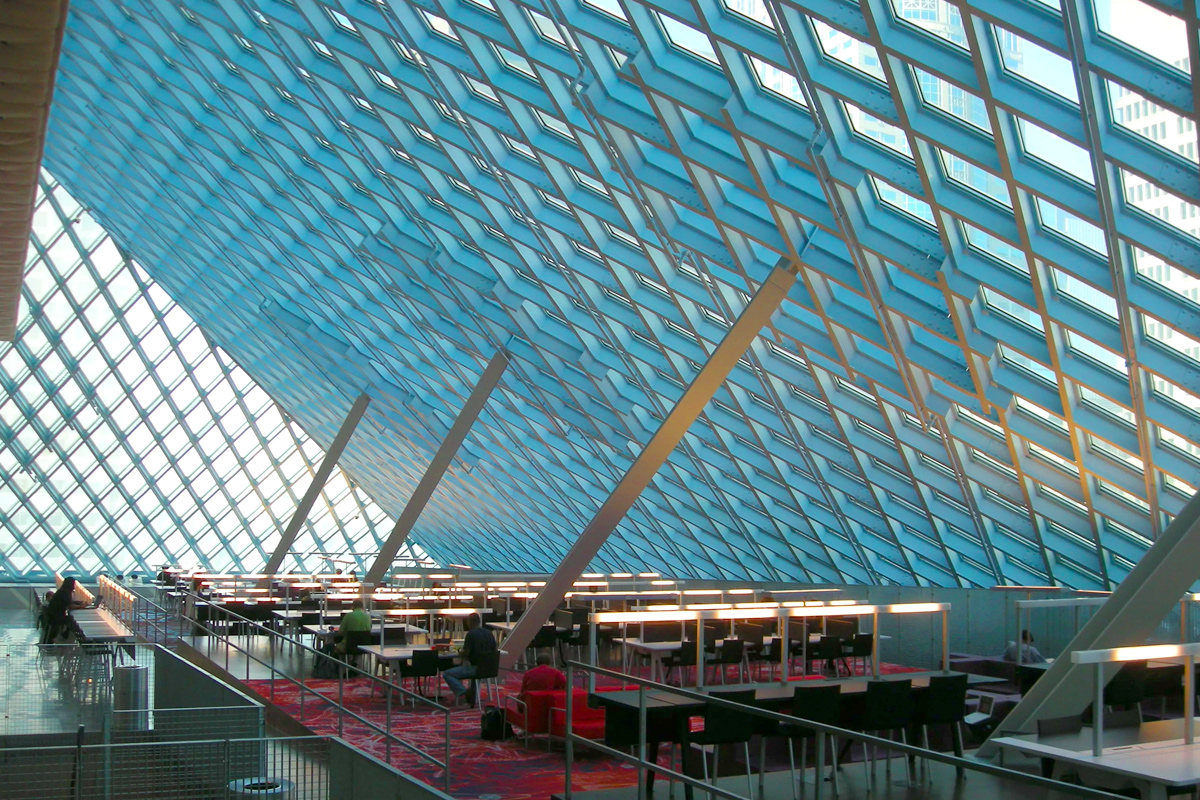
Seattle Central Library. Architects: OMA (Rem Koolhaas + Joshua Prince Ramus) and LMN Architects. Internal view of the lobby-living room. The steel diagonal mesh stabilizes the building against the wind and seismic loads. Painted in white, it offers an ever changing image of the internal space as the light reflects on its surfaces.
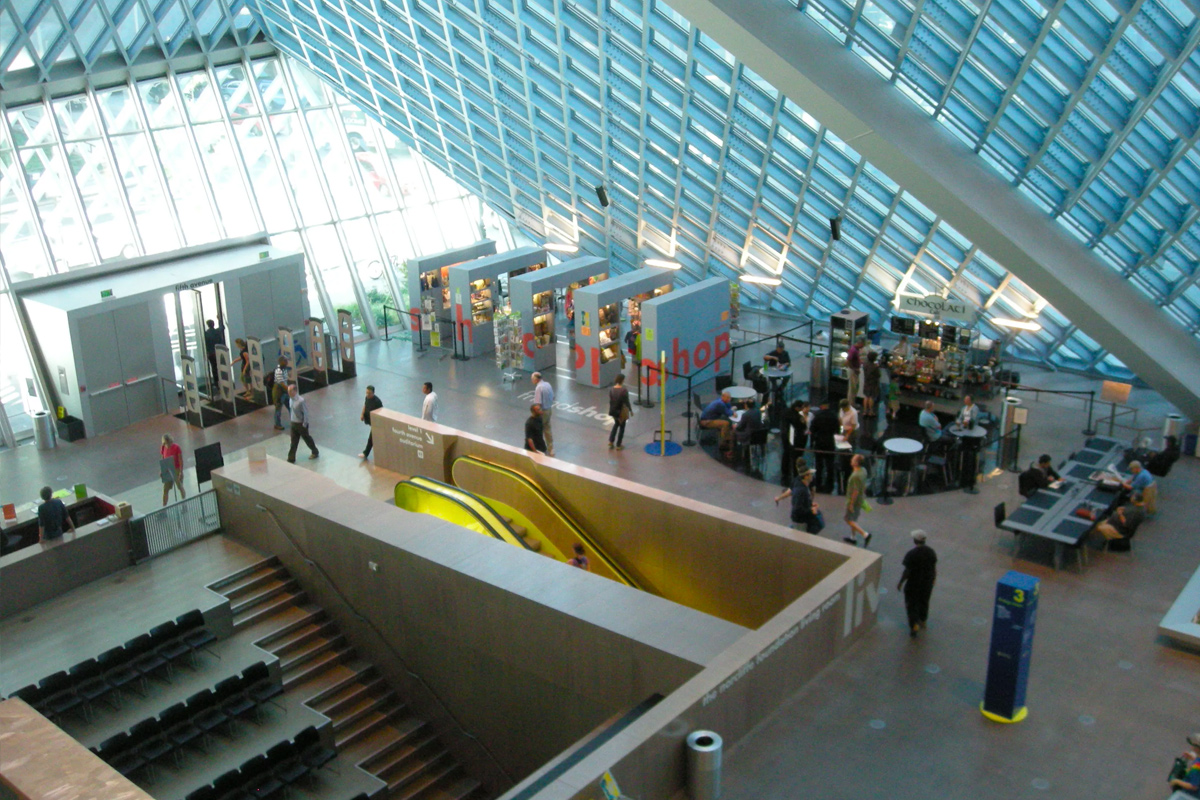
Seattle Central Library. Architects: OMA (Rem Koolhaas + Joshua Prince Ramus) and LMN Architects. Internal view of the lobby-living room. The steel diagonal mesh stabilizes the building against the wind and seismic loads. Painted in white, it offers an ever changing image of the internal space as the light reflects on its surfaces.
Inside the Boxes
The visitors are offered a different kind of experience inside each of the programmatic boxes. The “Assembly” box containing meeting rooms for public hire is entirely painted in bright red. Corridors and rooms are enclosed with curvy shapes recreating the experience of circulating through the veins and organs inside a body.
The Books box is in a continuous spiral which allows the books to be ordered in a linear system. One could think of it as an adaptation of the car park typology into the heightened purpose of containing shelves with books and knowledge showing one more time those intelligent shifts that distinguish OMA’s work.
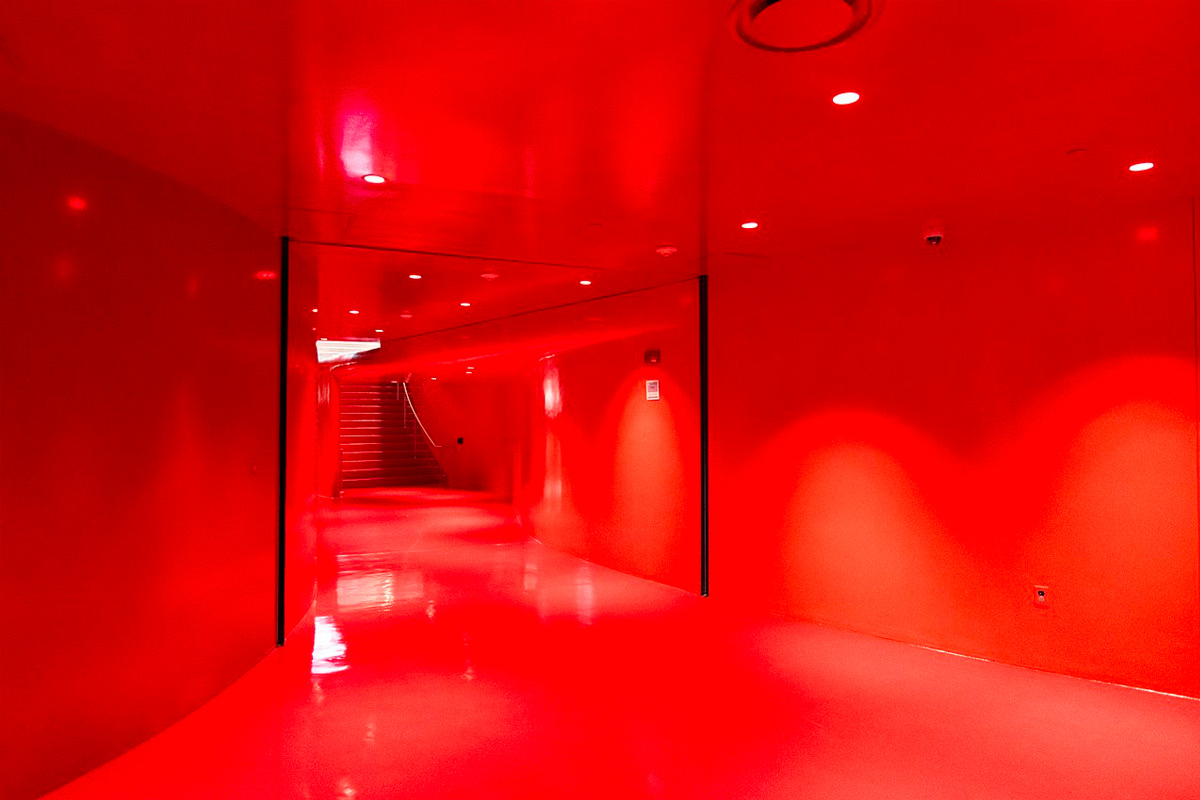
Seattle Central Library. Architects: OMA (Rem Koolhaas + Joshua Prince Ramus) and LMN Architects. Internal view of the corridor at the meeting rooms box. Every surface is painted in red and the curvy geometry suggests to visitors that they are circulating inside a body.
Even if you haven’t yet travelled to NYC you will not fail to recognize the unmistakable triangular shape of the Flatiron Building which has featured in countless blockbuster movies such as Reds, Godzilla, or Spiderman.
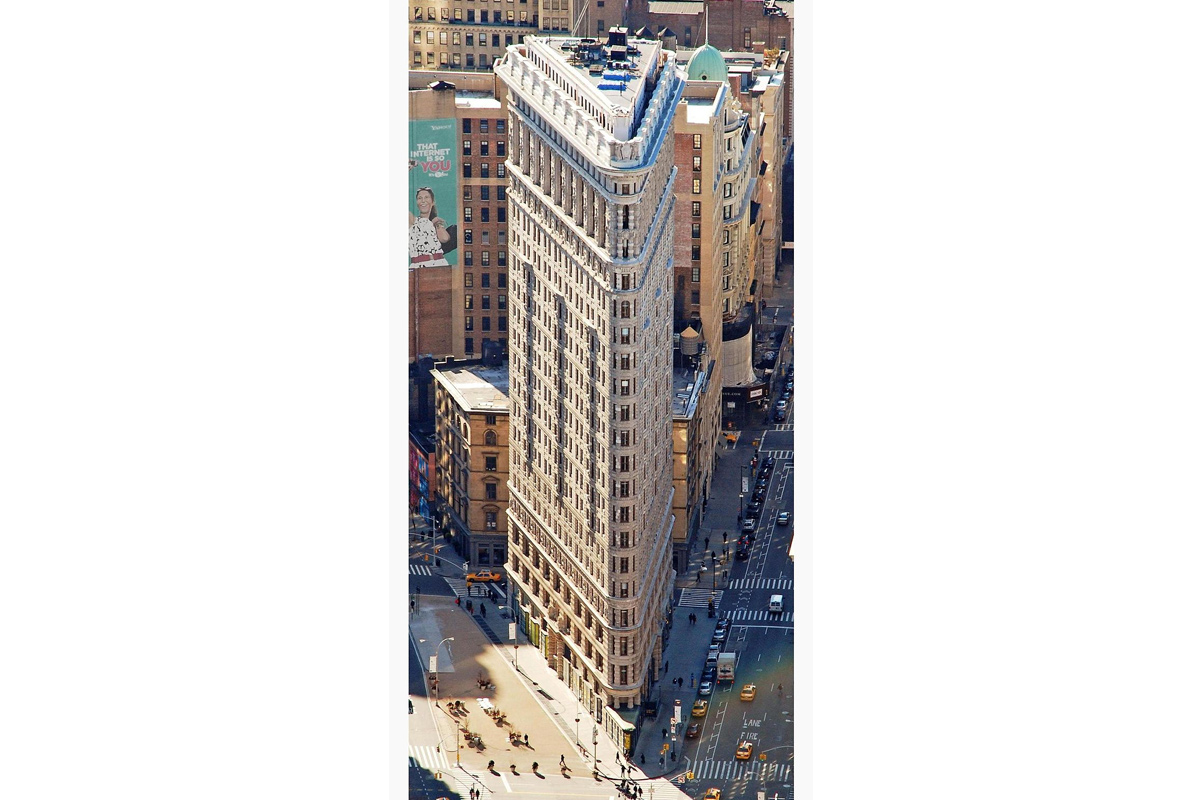
Aerial view of the Flatiron building at the corner of Fifth Avenue, Broadway, and East 22nd Street. Although this triangular prism resembles the shape of a clothes iron the building derives its name from the Flatiron District neighborhood in Manhattan.
This 22-storey, 285-foot (86.9 m) tall steel-framed building is located at 175 Fifth Avenue in Manhattan, New York City. The name for the building has nothing to do with its metal structure but comes from the Flatiron District neighbourhood where it is located.
The Flatiron District rests on an area of Manhattan where its schist bedrock is deepest underground and as a result under the influence of zoning laws, the tallest buildings in the area could reach 20 storeys.
The building was designed by Daniel H. Burnham who was a pioneer in the development of skyscraper building and design. He founded the architectural practice, Burnham and Root with his friend John Wellborn Root in 1873. Burnham is considered by many to be ‘the father’ of the skyscraper.
Burnham and Root had previously designed The Montauk Building, a ten storey high steel commercial block which was constructed between 1882 and 1883. Although the building was demolished in 1902 to make way for the First National Bank headquarters there are claims that the Montauk was the first building to be referred to as a skyscraper. It cost around $325,000 at the time , about $8.3 million in today’s money.
Designed as a vertical Renaissance palazzo
Using the lessons learnt on projects such as The Montauk Building, Burnham set about designing and constructing the Flatiron Building which was originally called the Fuller Building in honour of George A. Fuller a Chicago based architect and real estate developer. The latter had expanded his business to the NYC marketplace and is often credited as being the “inventor” of modern skyscrapers. However, NYC locals persisted in calling the new tower block “The Flatiron” a name which has since been made official.
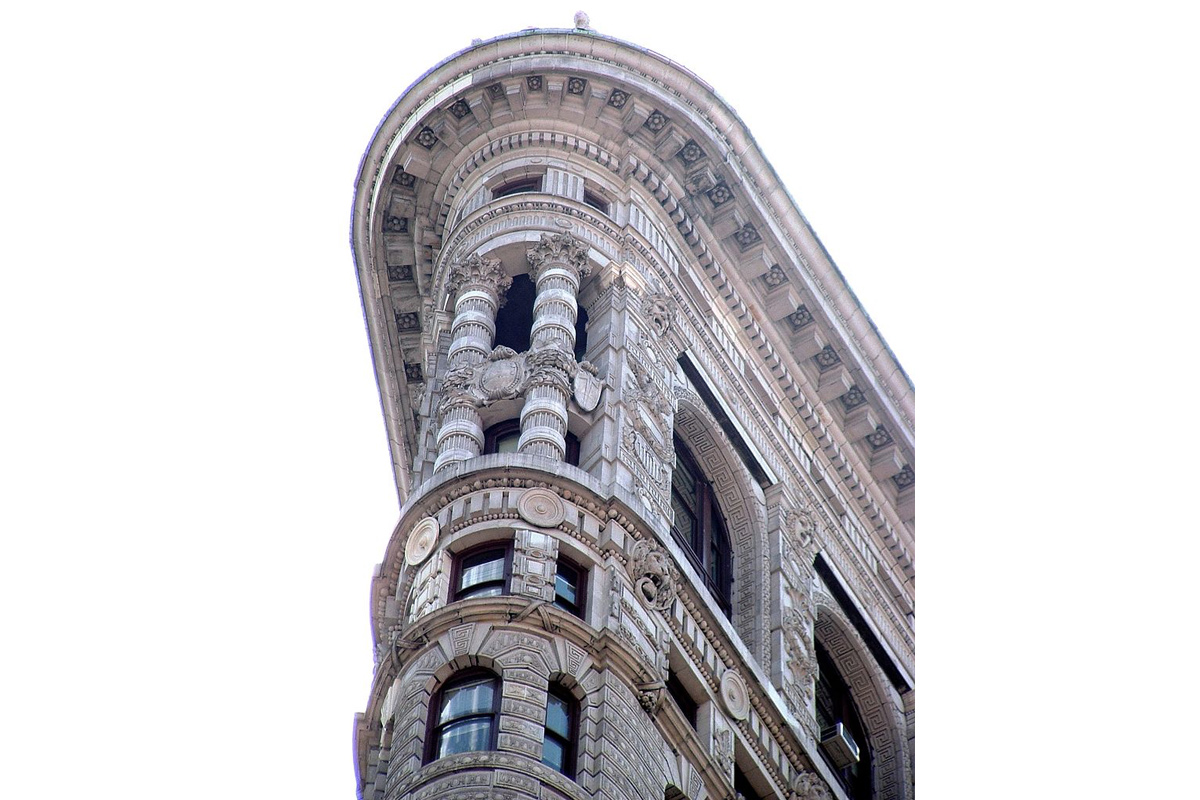
The rather abstract triangular shape of the building was governed by the layout of the plot owned by Harry S. Black, George Fuller’s son-in-law who had taken over the Fuller Company. The layout forms a triangular prism around an almost perfect right angle triangle so that the building is only six feet wide where the two longest sides of the building meet. The building’s design stems from the Beaux-Arts school of architecture, a relatively short-lived movement that started in 1895 and lasted around 45 years. The buildings designed in the Beaux-Arts school are all characterised by symmetry and include lots of design elements, such as balconies, pilasters, balustrades etc. The Beaux-Arts school was also very fond of Italian and French renaissance influence so Burnham designed the building as a vertical Renaissance palazzo.
Behind the ornate facades lies one of NYC’s first steel skeleton structures
The building contains a skeleton of steel, and the building’s frame was clad with limestone and terra-cotta curtain walling. Like a classical Greek column, its facade is divided into a base, shaft, and capital with limestone at the bottom changing to glazed terra-cotta as the floors rise,
The architects used the then-revolutionary curtain wall method. This method took advantage of a change to New York City’s building codes in 1892, which eliminated the requirement that masonry be used for fireproofing considerations. This opened the way for steel-skeleton construction.
Once construction kicked off in the summer of 1901 the building went up at an amazingly fast pace of one floor a week. All the steel parts were meticulously pre-cut off-site and slotted together very quickly. By February 1902 the frame was complete, and by mid-May the building was half-covered with terracotta tiling. The Manhattan neighbourhood watched on in awe as this giant Meccano was put together and completed in just one year by June 1902. The 20- story high steel-framed building topped out at 307 feet tall which made it one of the tallest tower blocks in NYC at the time.
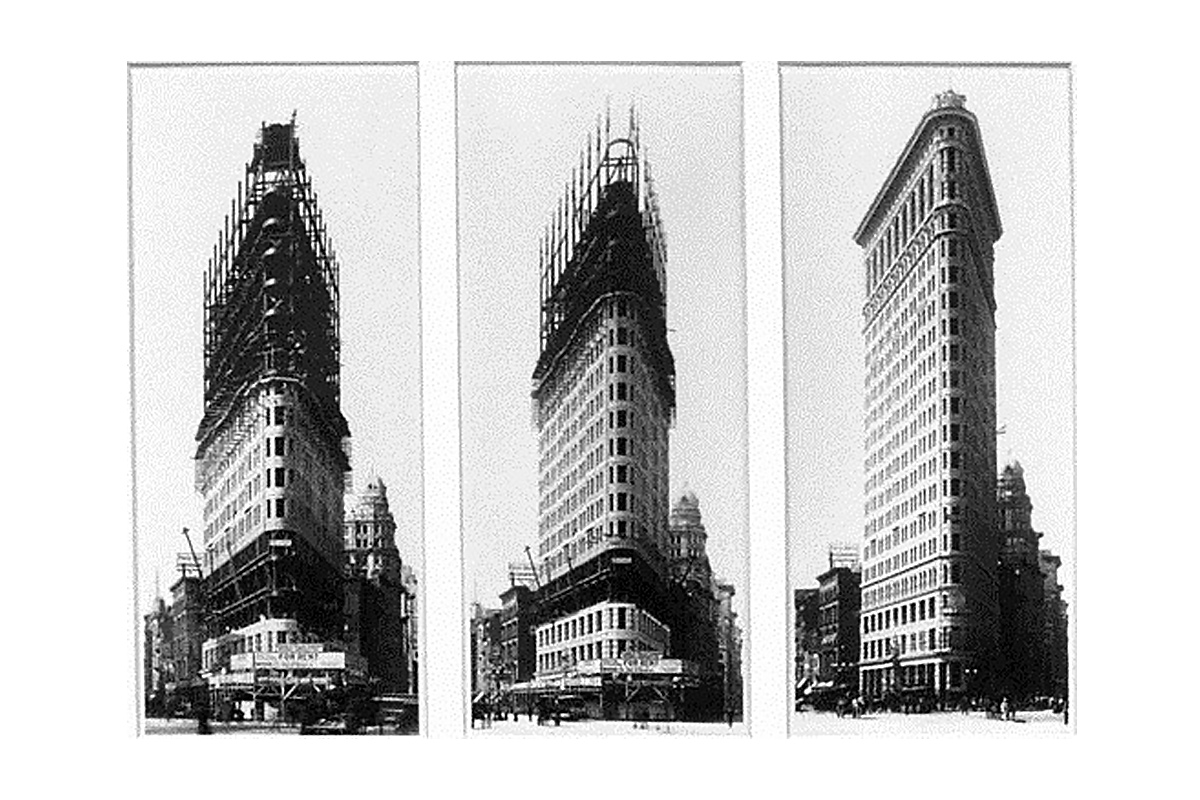
These images show the different construction phases of the Flatiron building: first the steel frame structure followed by the limestone and terracotta envelope (159 words)
Image from the Library of Congress
On completion, many leading experts expected the expectation the building might blow over in the first strong wind. But Purdy and Henderson, the building’s structural engineers had anticipated this problem: since the building was quite narrow and therefore had less volume to resist wind load they strengthened the structure. Steel bracing enabled the building to withstand four times the amount of wind force which it could ever be expected to endure. In 1905, three years after completion it was decided to add a penthouse level at the top of the building as well as a basement floor so that made a total of 22 floors. A retail space at the front of the building (dubbed as a “cowcatcher”) was also added in order to maximize the use of the building’s lot and produce some retail income.
The building’s novelty attracted a flow of criticism
As so often happens with iconic buildings, its design was not popular with architectural critics, and The New York Tribune memorably described the building as ‘a stingy piece of pie.’ The New York Times described it as ‘a monstrosity.’ The original owners moved out of their 19th floor home in 1929 and although the mayor of NYC tried to turn the area into a new business district, north of Wall Street this idea never worked. So for many years the surrounding area remained underdeveloped.
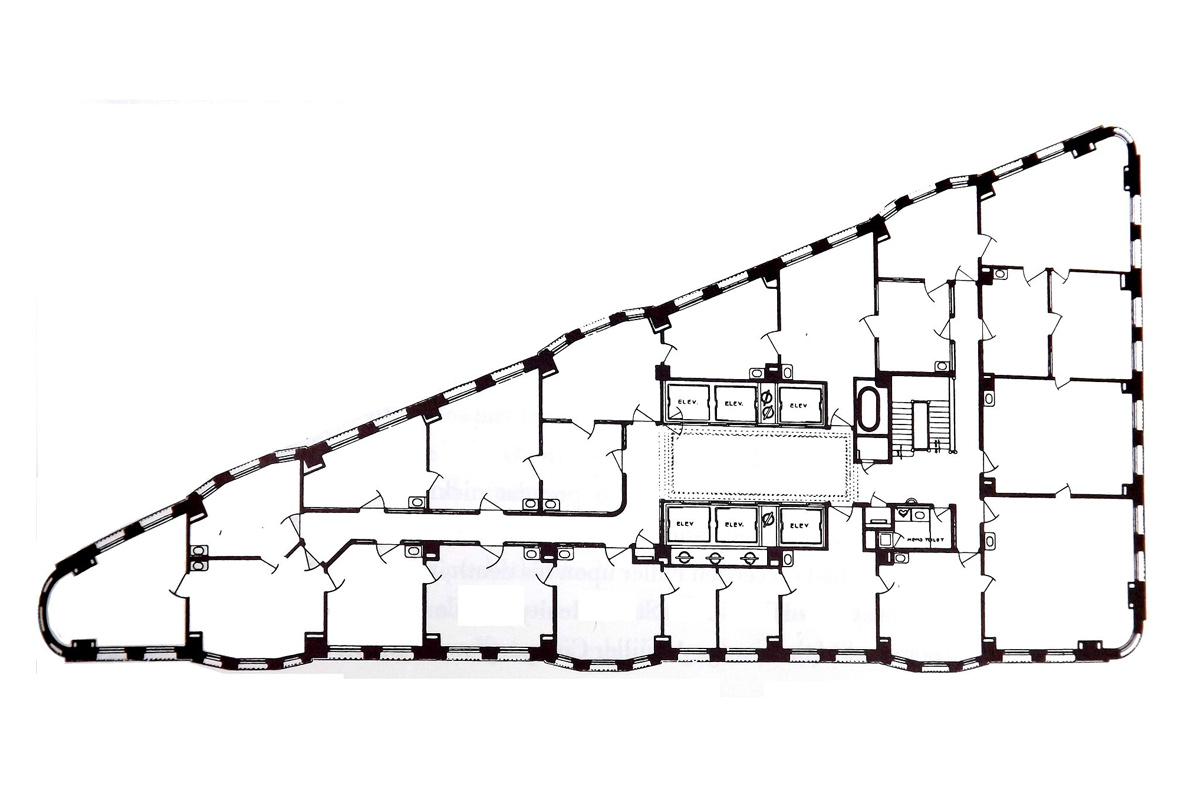
The office space within the Flatiron building was cramped and awkward to furnish because of its triangular shape. The architects also ‘forgot’ to include female restrooms
Because of the triangular shape of the structure, office space was extremely cramped and awkward to furnish. Tenants described it as a “rabbit warren” of oddly-shaped rooms.The building was considered to be “quirky” overall, with drafty wood-framed and copper-clad windows, no central air conditioning, a heating system which utilized cast-iron radiators, an antiquated sprinkler system, and a single staircase should evacuation of the building be necessary.
Despite its many shortcomings the Flatiron became very trendy
The building’s elevators were an Otis water-powered hydraulic type. This first generation of elevators were remarkably unreliable and extremely slow. Part of the problem was that the elevators were famous for leaking and flooding the building. The original and beautiful elevator cars are still in use to this day.
To make things worse, Burnham forgot to install or more likely did not install female restrooms. This omission meant that the building’s management had to alternate floors for male and female bathrooms. Additionally, to reach the top floor – the 21st, which was added in 1905, a second elevator has to be taken from the 20th floor. On the 21st floor, the bottoms of the windows are chest-high.
Despite all its shortcomings the Flatiron has attracted over the years an eclectic variety of tenants going from the prestigious Imperial Russian Consulate, to the crime syndicate Murder Inc. during the Prohibition period in the 1920s-30s. In 1959 Macmillan the publishers occupied the entire building between 1959 until 2004. The retail space (or”cowcatcher”) at the “prow” of the building was leased by United Cigar Stores, and the building’s vast cellar, which extended into the vaults that went more than 20 feet (6.1 m) under the surrounding streets was occupied by the Flatiron Restaurant, which could seat 1,500 patrons. In 1911 the Flatiron Restaurant was bought by Louis Bustanoby, of the well-known Café des Beaux-Arts, and converted into a trendy 400-seat French restaurant, Taverne Louis.
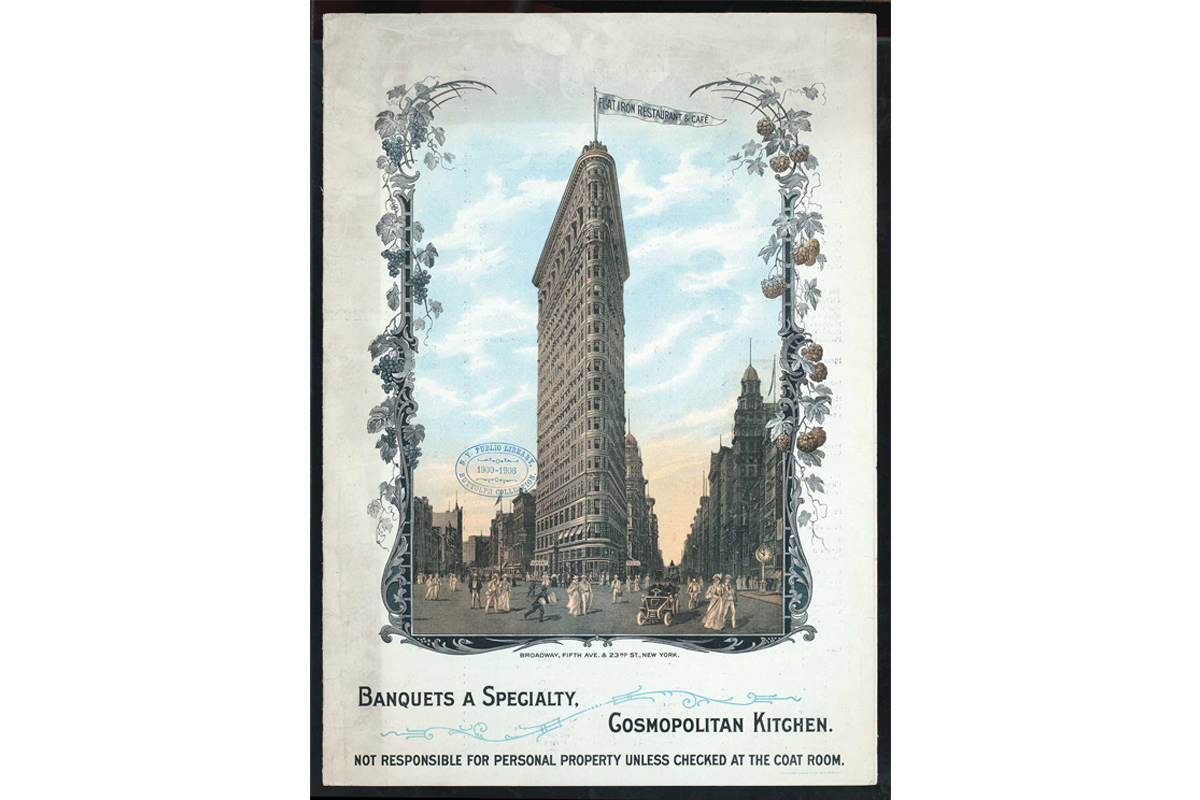
A massive basement restaurant in the Flatiron building attracted Broadway audiences, artists and jazz musicians.
It was conveniently open from breakfast through late supper to attract the audiences of nearby Broadway shows. It was among the first of its kind to allow a black jazz band to perform, thus introducing ragtime to affluent New Yorkers. However The Taverne was forced to close during the period of the Prohibition which led it to become a shady speakeasy during that period.
The Flatiron also attracted the attention of numerous artists such as the French artist Albert Gleize who made a Cubist style etching of the building in 1916. While taking a photo of the building during a snowstorm in 1903 the photographer Alfred Stieglitz fell under its spell “…it appeared to be moving toward me like the bow of a monster ocean steamer – a picture of a new America still in the making”. He added that the Parthenon was to Athens what the Flatiron was to New York.
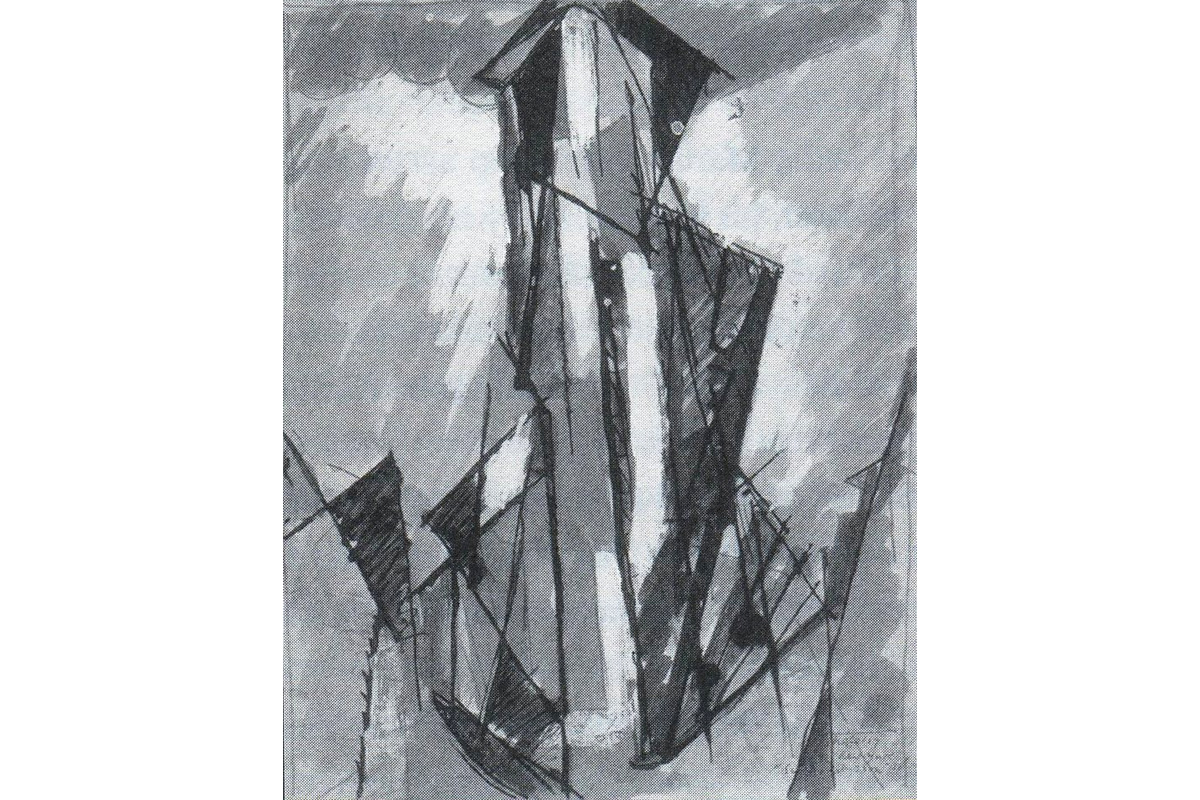
“Sur le Flat-iron”, graphite, ink and gouache by Albert Gleizes, 1916 held in the permanent collection of The University of Michigan Museum of Art. Following its completion the Flatiron building inspired many artists such as this French Cubist painter.
As the building’s enduring appeal to New Yorkers grew, it helped to attract high-end shopping and fantastic restaurants. The Flatiron Building was designated a NYC landmark in 1966 and a National Historic Landmark in 1989.
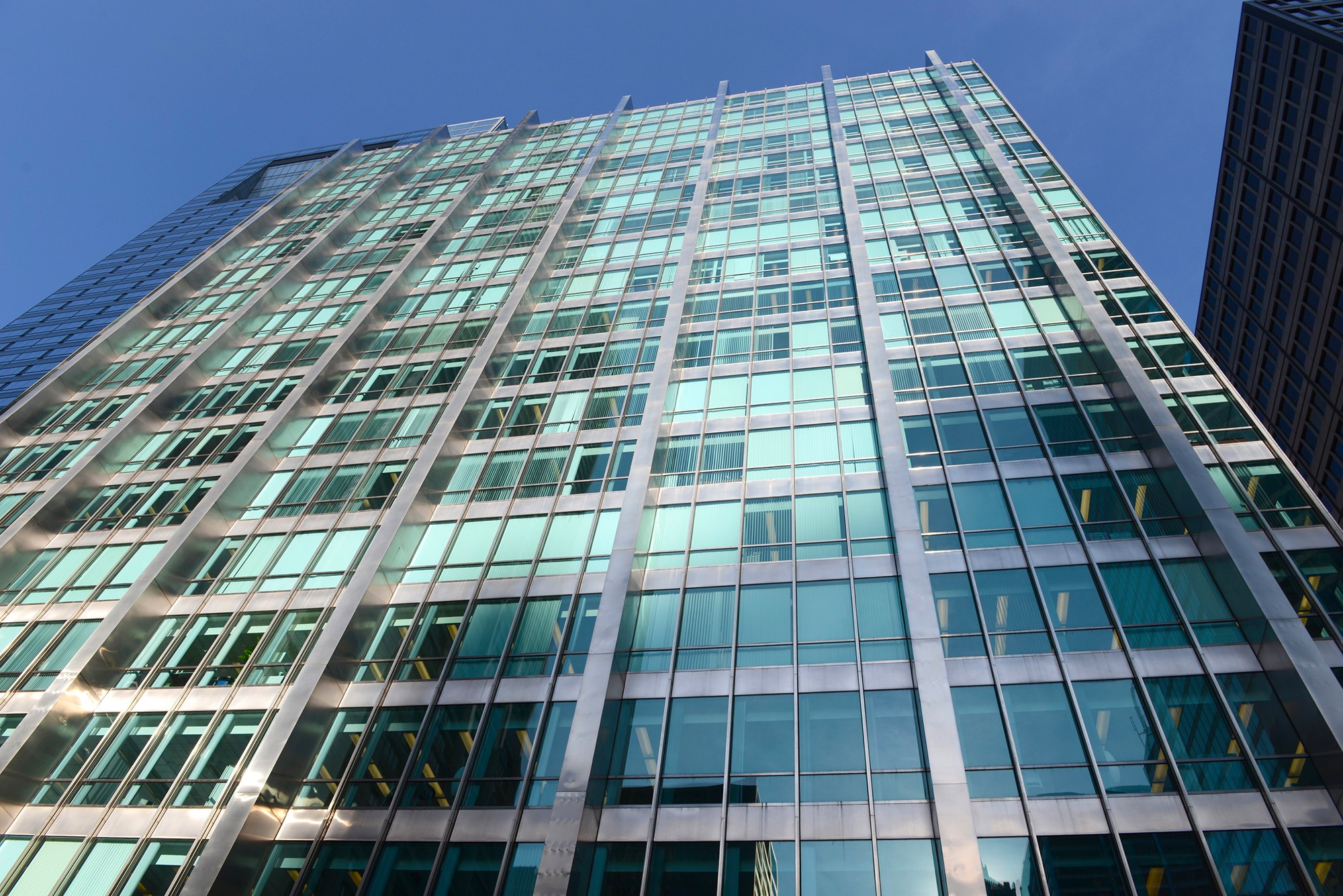
Built in 1958 the Inland Steel building ushered in a new era of modernity for Chicago with its shimmering façace that combines aquamarine glazing and brushed steel.
Founded in Chicago in 1893 by financier Phillip Block, the Inland Steel Company had grown from strength to strength to become the eighth-largest steel producer in the United States by the 1950s. To celebrate this success, Inland Steel commissioned a new corporate headquarters in Chicago’s Loop in 1954. This was the first high rise to be built in Chicago since the Great Depression during the 1930s so Inland Steel wanted a building with a modern design that would symbolize the resilience of the steel industry and showcase their product as well as other postwar technologies. “We wanted a building we’d be proud of, one that spelled steel,” said Leigh Block, a former Vice President of the Inland Steel Company and descendent of one of the company’s founders.
The Inland Steel building is located in the Loop, Chicago’s downtown district which features today other high-rises that were built later but also public parks, shops and restaurants, hotels, theaters and museums. It has become the second largest commercial business district in North America and home to Chicago’s City Hall, the seat of Cook County, and numerous offices of other levels of government and foreign consulates.
Ushering in Modernist architecture
The original concept design was by Walter Netsch but it was later taken over by Bruce Graham who completed the project and received most of the credit for the building design. This was to cause a life-long feud between Netsch and Graham.
(Bruce Graham was a world-class modernist/brutalist architect. He went on to design many other high-rise buildings including the 108-storey Sears Tower another of Chicago’s landmarks which at the time, was the tallest building in the world. It held that ranking from its completion in 1973 to 1998. The Sears Tower was renamed the Willis Tower in 2009).
This elegant 19-storey office tower displays sleek facades combining shimmering aquamarine glass and brushed stainless steel. Its sleek sophisticated design ushered in a new era of modernity in the city. The primarily glass facade is completely devoid of ornamentation. This must have been a surprising change for Chicagoans accustomed to the richly ornamented terra cotta, brick and stone facades of the past. The building’s design illustrates all the principles of Modernist concepts such as perfect proportions, attention for detail, quality materials.
An open plan aesthetic
Inland Steel’s column-free interior demonstrates the Miesian design concept of universal space. The structure of the building is based on 3 Miesian boxes. The term Miesian is from the incredibly influential German-American architect Ludwig Mies van der Rohe.
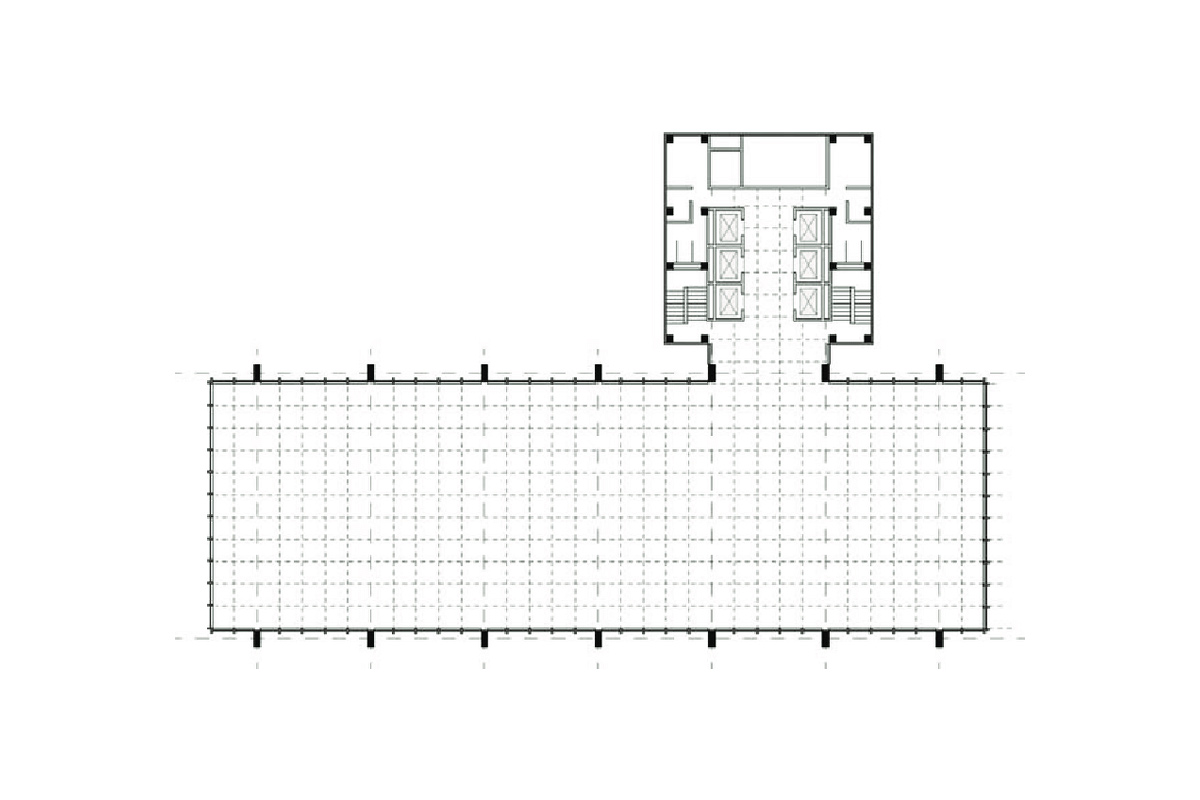
Floor plan of The Inland Steel Tower showing the location of the service tower behind the office tower and the supporting 14 exterior columns that free up the floor space completely on each level
The building form consists of two towers: a 19 storey office tower to which is attached to a 25 storey service tower that stands behind it and contains all the building’s essential systems including its lavatories, seven elevators, staircases and vertical circulation. Because the central core of the building is all contained in the attached service tower this frees up all the floor space in the adjoining office tower. As a result each level had 10,200 square feet of unobstructed, expansive space. There are no internal columns on the floors because all the structural elements have been pushed outside of the building’s curtain wall. The clear-span construction is also made possible by seven pairs of nickel-chrome stainless steel clad columns (carrying the weight of the structure). The exterior columns of the building were clad with brushed stainless steel cladding.The irony was that Inland Steel were only producing carbon steel at the time of construction so the stainless steel for the building had to be purchased from another steel company.
The building’s open plan design was truly innovative at the time of its completion. It provided unmatched, flexible square footage to tenants. This was made possible by running 60ft supportive girders beneath each floor between the pairs of columns spanning the length of the tower’s exterior. The heating/cooling distribution system and telephone lines were also run beneath the floors to further clear the interior of obstructions. The floor is made up of a grid of modules that can be lifted to access these systems. The wide-open floor plan of the Inland Steel office tower is partly responsible for the building’s enduring popularity. Even today, it allows fast developing companies to adapt the space to their constantly changing needs brilliantly illustrating the Modernist concept that ‘form follows function’
Lightness, serenity and polished grace
Construction started in 1957 and was completed within a year thanks to the straightforward construction techniques utilized. The office tower seems to float above its glass-enclosed, transparent lobby—staying true to a Mid-Century Modern aesthetic. The sculpture in the lobby,Richard Lippold’s Radiant One, 1957, seen below, is a golden rod-and-wire construction, shaped like an atomic era asterisk, a clear indicator of mid-century style. It dominates the space and feels weightless against a black marble wall that reflects the sculpture and the city outside. His art belongs to a sculptural tradition that began in the early 20th century with Cubism and Constructivism, which shifted focus from the shaping of solid materials to the orchestration of spatial relations among abstract elements. Many of his works were suspended but here Lippold has used the reflective qualities of a shallow marble pool.
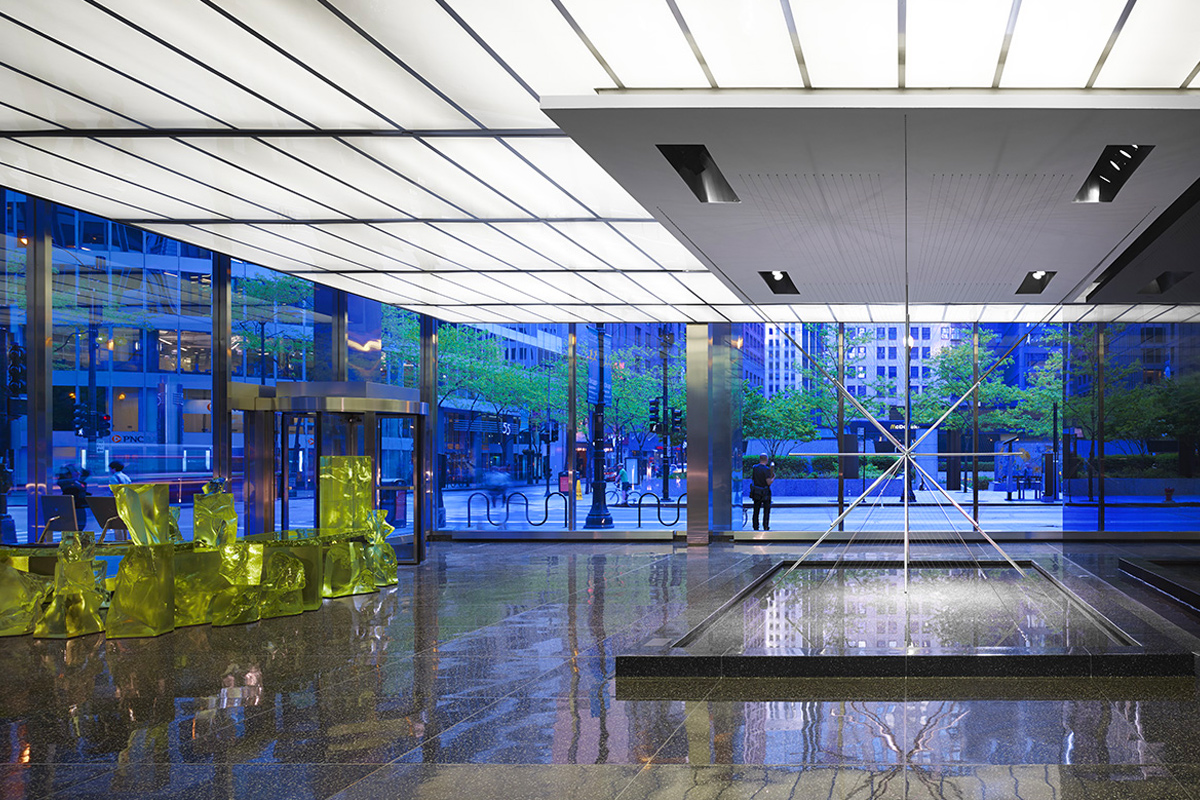
Richard Lippold was an industrial designer before becoming a sculptor. His geometric constructions play on the reflective qualities of goldenrod and wire as a medium
In 1969 the Inland Steel company had 25,000 employees. The company was heavily focused on the automotive sector, producing steel for most American car manufacturers. The company did suffer in the 1970s from imported steel, but due to outstanding management, they stayed profitable. They became so profitable in the late 1990s that they became a takeover target. Ironically just when the Inland Steel Building was designated a Chicago Landmark in 1998 the Inland Steel Company was bought out by ArcelorMittal.
A building that refuses to grow old
In 2018 the building underwent an extensive ground-up renovation conducted by SOM to make it more energy efficient and sustainable for the 21st century. This included for instance, refitting the existing glazing with low-e high performance glazing, installing a high insulation green roof to manage stormwater runoff, integrated daylight facade and chilled beams, which use less energy for cooling than conventional HVAC systems. However as Cate McCormack vice president and general manager of Inland Steel underlines: “maintaining the attributes of the property that make it so historically and architecturally significant, as well as not disrupting tenants’ spaces, were our biggest obstacles when integrating energy-efficient technologies.”
McCormack added that, “We successfully delivered building systems that will curb energy costs and reduce the property’s impact on the environment and our community, while maintaining its classic features.” The design also calls for new art in outdoor plazas and a revolving art program in the tower’s lobby.
To conclude, architect critic M.W. Newman wrote in 1982 when the tower won an AIA 25 year honor award “In a steel-building city, [the Inland Steel Building] . . . retains a lightness, serenity, and polished grace that continue to make it an influential emblem of modernism.”
History of the Inland Steel Company
It was Phillip Block, a Chicago based financier who set up Inland Steel Company in 1893.
He rapidly expanded the company which grew from 250 staff members in 1897 to 2600 workers in 1910.
As the business began to thrive so did East Chicago where it was located. The area experienced explosive demographic growth. Between 1900-1910 the US census shows that the population soared from 3411 to 24 000. In just a decade the city had become the largest industrial powerhouse in the whole of the USA with over 80 per cent of land zoning dedicated to heavy industry. It acted as a suction pump attracting immigrants from all over Europe and the United States. Labor shortage during the First World War brought waves of Mexicans followed by the Great Migration of Black Americans from the rural Southern States but also Polish families. According to a city demographic survey in 1959, there were 1,000 Mexican families, 10,000 African American families, along with 3,000 Polish families
Inland Steel would be a massively important part of East Chicago’s economy until the late 1990s.The company carried out all its manufacturing at one major steel plant in East Chicago, Indiana. The Indiana Harbor Ship Canal was built in 19107 to connect the Grand Calumet River to Lake Michigan. This waterway allowed the company to take shipments of iron ore into its production facility and send finished goods easily out of the plant afterwards.
The growth of the company’s steel output was quite remarkable. In 1903 Inland Steel produced approximately 60,000 tons of steel. In 1914 the company’s production had expanded to over 600,000 tons. In 1917 the company broke the magic 1 million tons for the first time. At its peak of production in 1978, the company produced 8.6 million tons.
By 1969 the company had 25 000 employees. The company was heavily focused on the automotive sector, producing steel for most American car manufacturers. The company did suffer in the 1970s from imported steel, but due to outstanding management, they remained profitable. They went on to be so lucrative that in 1998 The Inland Steel Company was bought out by ArcelorMittal.
Agora
a. the marketplace in Athens, used for popular meetings, or any similar place of assembly in ancient Greece
b. the meeting itself
Architecture has been defined in many different ways over the centuries until it became the discipline that we recognize today. It encompases a varied mix of art, craft, engineering and an increasing level of information management. Nevertheless, one thing that has proved a constant throughout its history is the role of Architecture as an artificial medium to define a kind of relationship between people and the surrounding environment, be it the landscape, the sea or the city.
Agoras are places that, since ancient greek society times, have served as spaces where people meet to discuss, share, gather, talk, trade or relate in society; they are spaces that represent the values of the polis – the city.
Probably one of the minimum expressions of architecture is to build a roof several meters above the floor. The simple gesture of drawing a line parallel to the ground gives birth to an element capable of accomplishing several things at the same time: it gives shelter and protection from the climate to the people, marks a place in the city and symbolizes values of comunion and collaboration that are rooted in the spirit of the concept of city.
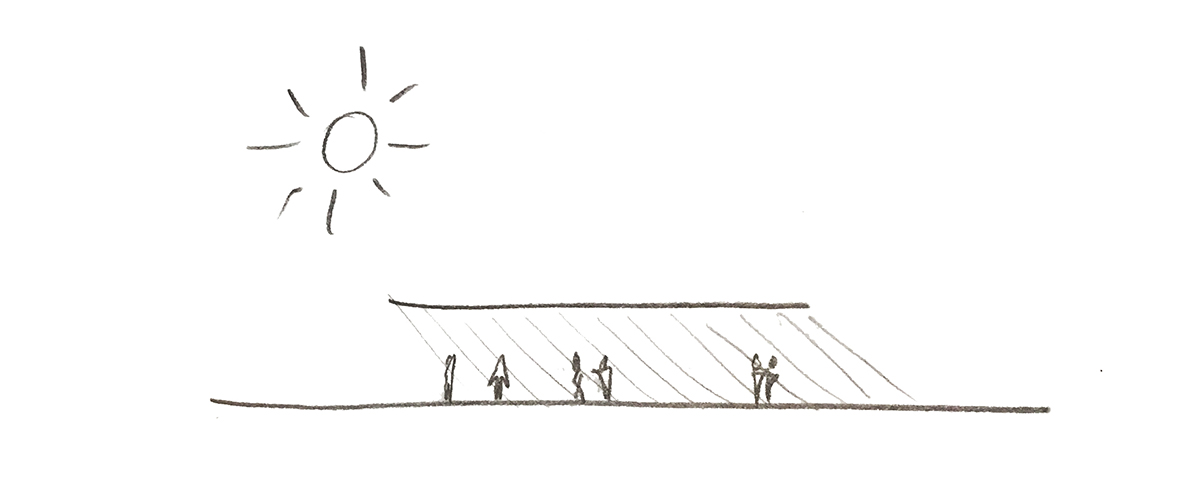
Simple sketch illustrating how people gather under a single roof that protects them against the climate.
Sketch by Antonio Moll
Black Steel modern symbols
The Cervantes theatre in Mexico City was designed by Ensamble Studio – directed by Antón García-Abril and Débora Mesa – in 2012 and its construction finished in 2013.
From the outside one can’t really tell what the building is about, because the only visible part above ground is a gigantic black steel canopy. It acts as the central piece articulating a group of buildings that surround it: the Jumex Museum, the Soumaya Museum and the Plaza Carso Shopping Mall.
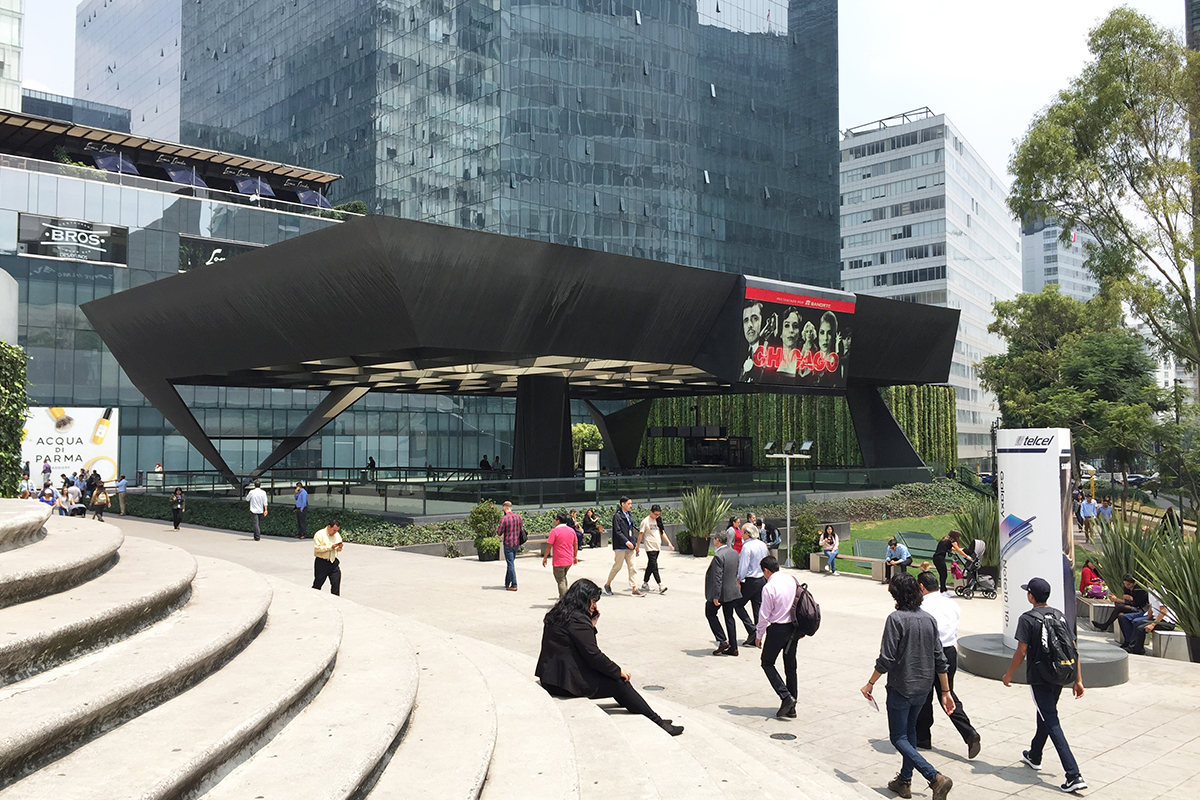
Cervantes Theatre in Mexico raises from the ground in the form of a black steel canopy supported by origami like columns. Architecture: Ensamble Studio, Antón García-Abril and Débora Mesa.
Photograph by Antonio Moll.
This floating metal keystone – as the architects refer to it – is the access lobby to the theatre, which is buried underground, and at the same time welcomes visitors to the public restaurant located inside the sunken courtyard.
I often refer to similarities with Mies Van der Rohe projects, but I think this only shows the immense influence that the german architect has had among all architects practicing these days. Is the Cervantes Theatre not a contemporary version of the temple-like typology concept proposed for the Neue Nationalgalerie in Berlin fifty years before? Are they both not heirs of the ancient greek agoras?
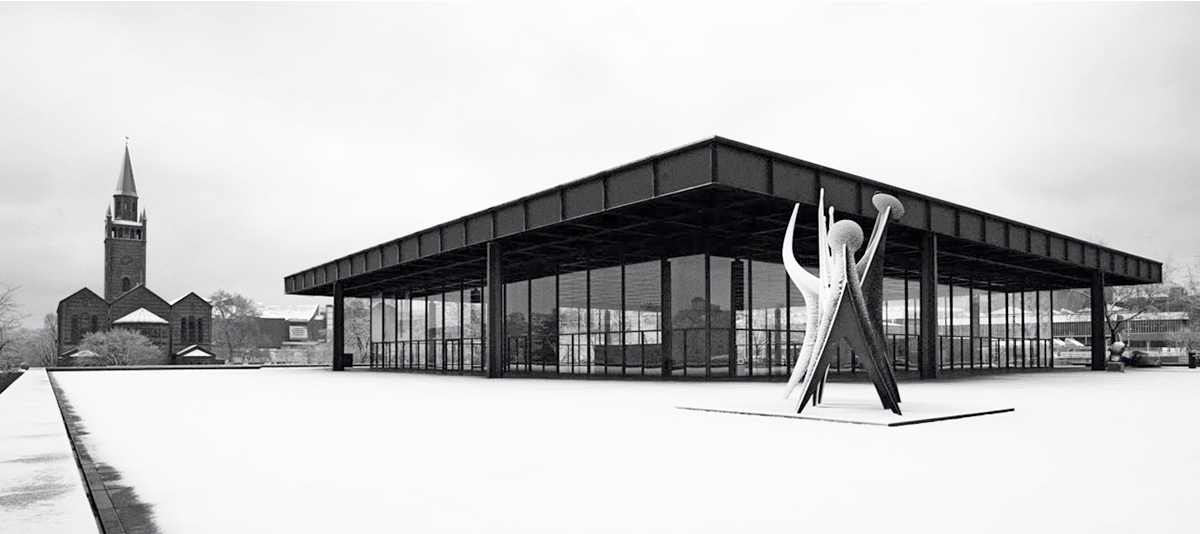
Neue Nationalgalerie in Berlin. A sculpture in the foreground by Alexander Calder welcomes visitors to the museum. Architecture: Mies Van der Rohe.
Photogram of the film Die Neue Nationalgalerie by Ina Weisse.
Both buildings stand alone in an urban void. They are composed of a buried plinth containing most of the spaces of the brief- an art gallery in the german building and a theatre in the mexican one – plus a monumental canopy that covers a gathering space and acts as a civic symbol. It seems that design and construction evolve, but the essence of building typologies remain.
Design language evolution
From the ancient temples, passing by the rational architecture of the 20th century to the contemporary designs, the look of our buildings has changed thanks to the different tools that architects and engineers can use nowadays in the studios.
Mies designs were all about dimensions, proportions and the relationships of the different parts of the building among them and the whole. He often incorporated visual corrections to his projects so they could be perceived as the pure geometries that he pursued. During the design process he liked to test his proposals producing big scale drawings and models that could bring him closer to how the real building would be perceived once built.
Some time around 1964, when the architects in his office produced a 1:5 scale drawing of the image of the Neue Nationalgalerie he realised that, due to its dimensions, the four corners of the roof gave the visual impression that they were hanging down. As a consequence Mies decided to slightly lift up each of them so the roof could be perceived perfectly flat once built.
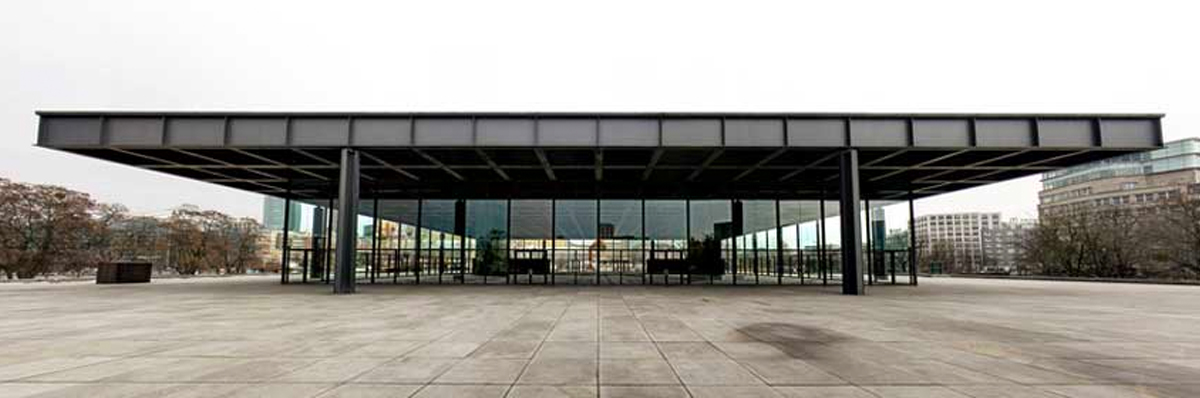
Neue Nationalgalerie in Berlin. The corners of the black steel roof have been raised to correct the visual effect of the ends hanging down. Architecture: Mies Van der Rohe.
Photograph from masdearte.com
Ensamble’s proposal differs from the German architect´s one in the sense that all, or nearly all, of the pieces that compose the roof are different. New software has made it possible to be more precise when drawing and dimensioning steel elements so the components of the theatre’s canopy can present themselves as if they were folded sheets of paper resembling an origami figure. The steel loses its load bearing condition appearance. Its geometry also reminds me of the stealth aircrafts, demonstrating that architects can draw knowledge and inspiration from different disciplines besides architecture itself.
By means of using computers, not only during the design stages but also during the construction, it becomes feasible for an architect to avoid repetition or rationalisation and explore different and singular forms.
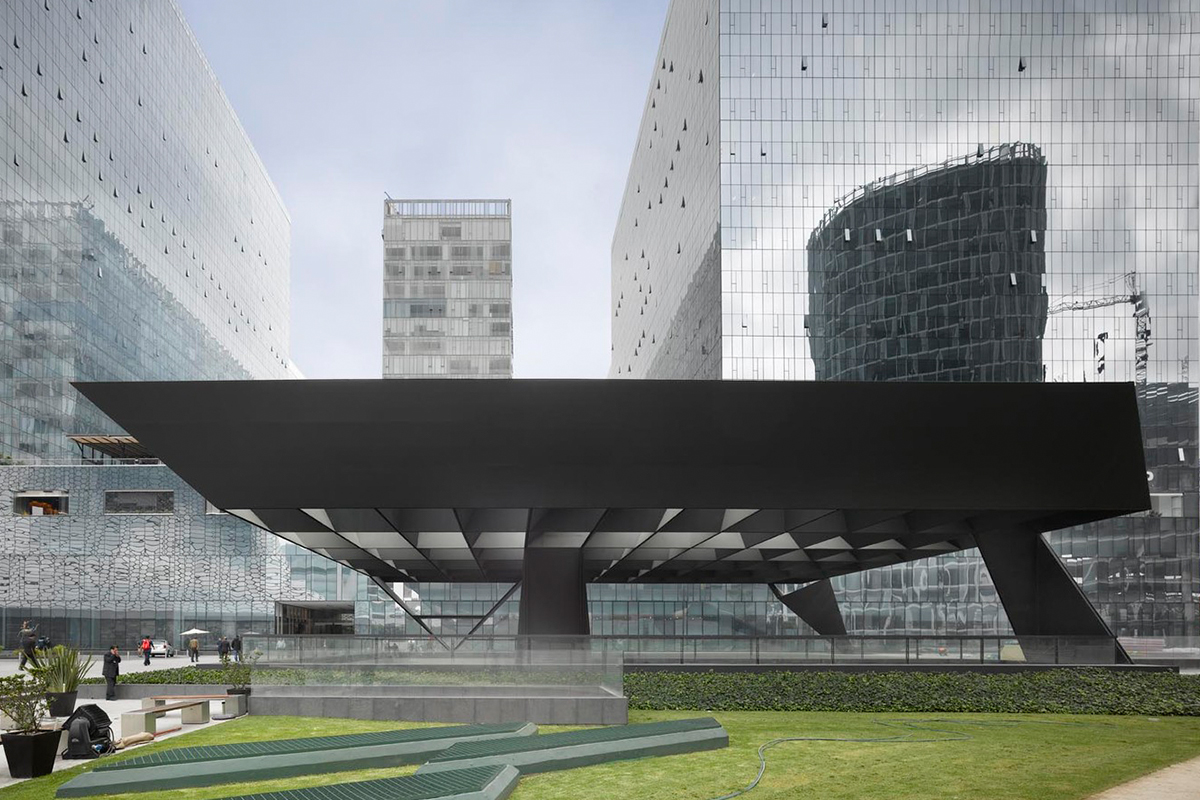
Cervantes Theatre in Mexico. Front elevation, the steel girder is covered by glass panels that let the light through to the lower levels. Architecture: Ensamble Studio, Antón García-Abril and Débora Mesa.
Photograph by Roland Halbe ©.
Construction techniques evolution
We all acknowledge the Neue Nationalgalerie as a masterpiece of history of architecture that summarizes Mies career but, besides the attractive and futuristic geometry that define the Mexican theatre’s black steel piece I also find extraordinary Ensamble design’s construction and assembled nature.
Mies’ museum construction required skilled welders to achieve a high level of precision. The different steel components arrived at the site on lorries. Once there they were moved on rails until each of them reached the correct location on the floor where they were welded. The entire roof was then lifted up in one piece to a total height of over eight metres with the help of eight hydraulic cranes in a public ceremony that lasted over nine hours.
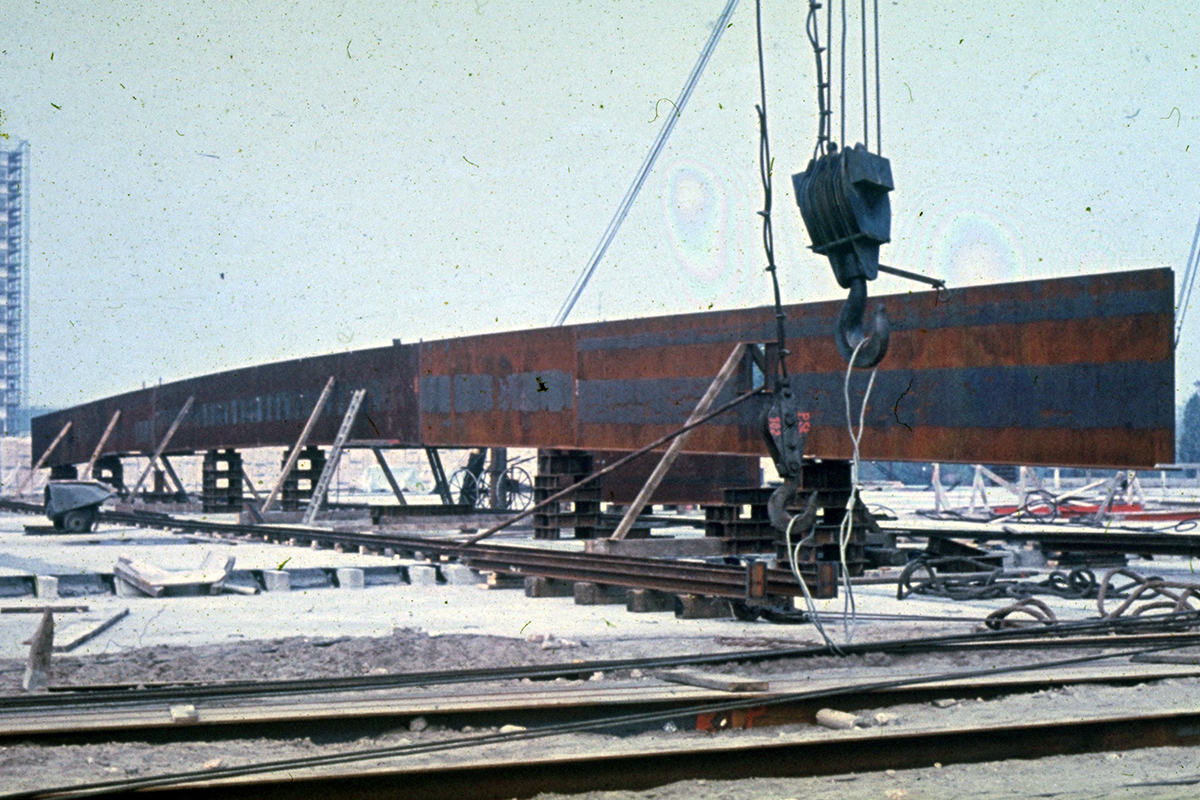
Neue Nationalgalerie steel beam on site during the construction. The different steel elements were moved on rails and pulled by lorries to their correct location. Architecture: Mies Van der Rohe.
Photograph by Heinz Oeter.
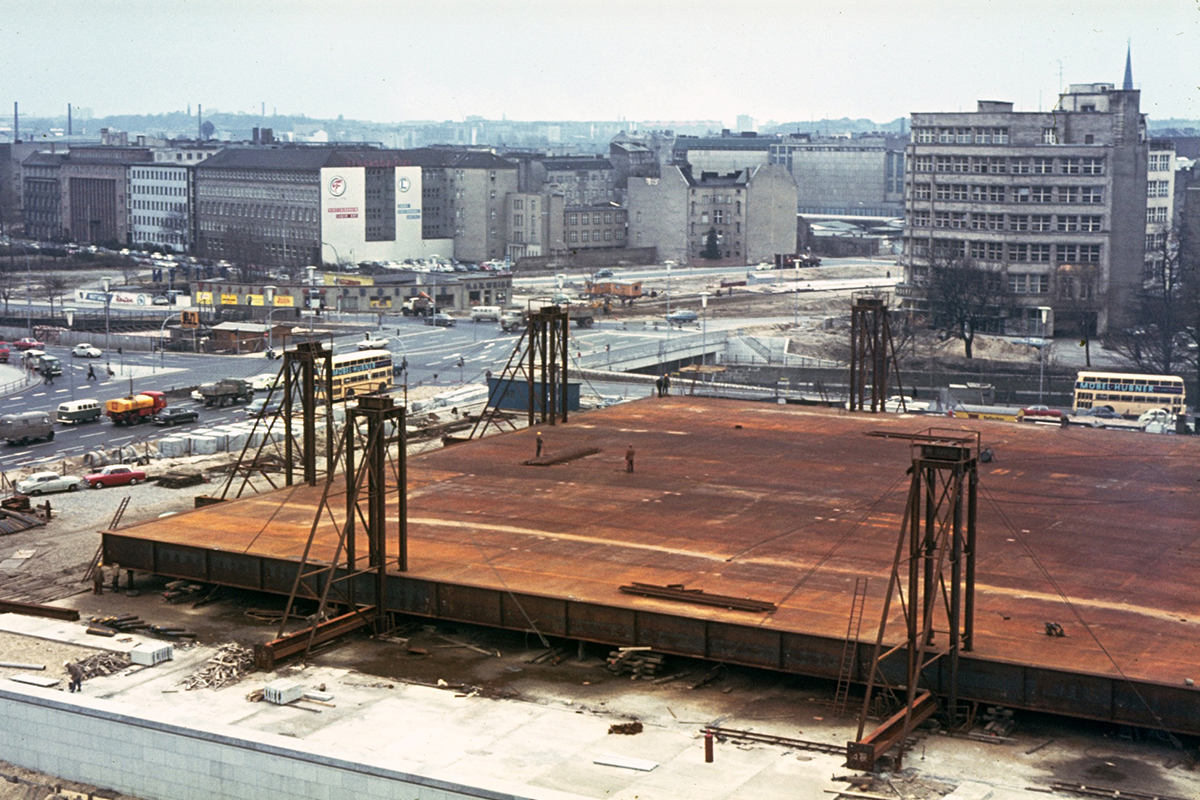
Neue Nationalgalerie roof before being lifted up with the hydraulic cranes during a public ceremony in 1967 . Each of the segments in which the side beam is divided is 3.6m long. Architecture: Mies Van der Rohe.
Photograph by Heinz Oeter.
On the contrary and in line with contemporary possibilities, García-Abril and Mesa decided to design a canopy that was composed of a series of precisely cut, full-length ribs with slots for them to interlock. They even tested their design assembly at the factory before dismantling it again and transporting it to the site for its final construction. Once on site, each of the ribs was lifted up individually by means of a crane and later welded at its final position.
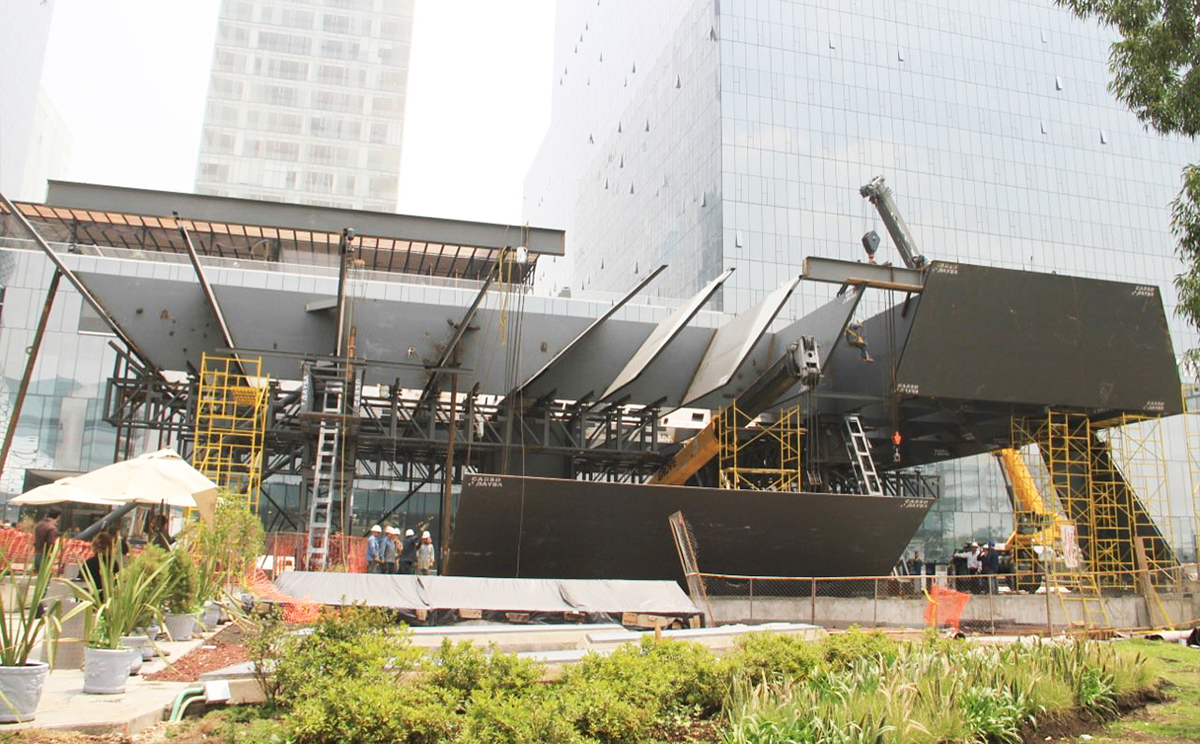
Cervantes Theatre during the steel ribs construction. The beams are put together by means of interlocking slots and welded at its final position. Architecture: Ensamble Studio, Antón García-Abril and Débora Mesa.
Photograph by Ensamble Studio.
Architecture is for the people
Our tools at the design studios change and it is logical that the results obtained also change but, there are things in architecture that remain. It serves people in our quotidian life actions, it offers us places to gather and enjoy a theatre play, a concert, to eat in the shadow, to protect us from the sun,rain or wind; and it serves society expressing the values of the community in a certain place at a certain time.
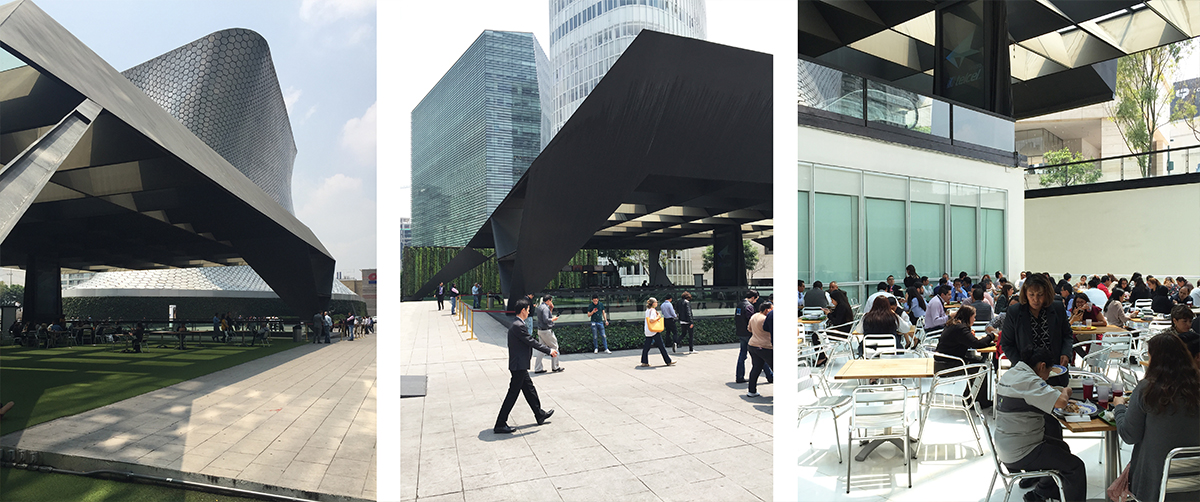
Cervantes Theatre. The canopy serves the public space in different ways, it signals a place, it protects from the sun or rain and it functions as the lobby for the restaurant and theatre buried underneath. Architecture: Ensamble Studio, Antón García-Abril and Débora Mesa.
Photograph by Antonio Moll.
‘Dymaxion’ was a word coined by Richard Buckminster-Fuller in the 1920s to refer to his various design and engineering projects. A portmanteau of the words dynamic, maximum and tension, Buckminster-Fuller designed the Dymaxion Car, the Dymaxion Map as well as the Dymaxion House.
An inventor, engineer, poet and architect, Buckminster-Fuller originally conceived of his transportable, circular, metallic Dymaxion House in the mid to late 1920s. It was not until the housing shortage just after World War II that Buckminster-Fuller, also known as Bucky, found a potential backer willing to fund prototypes of the house.
Dymaxion House design
The purpose of the design was to enable mass-produced houses that were easily transportable to any location in the world. Buckminster-Fuller’s design concept was to be fire-resistant, earthquake-proof and able to withstand extreme winds of up to 180 miles per hour. He wanted the dwelling he was perfecting to be suitable for all location and weather types.
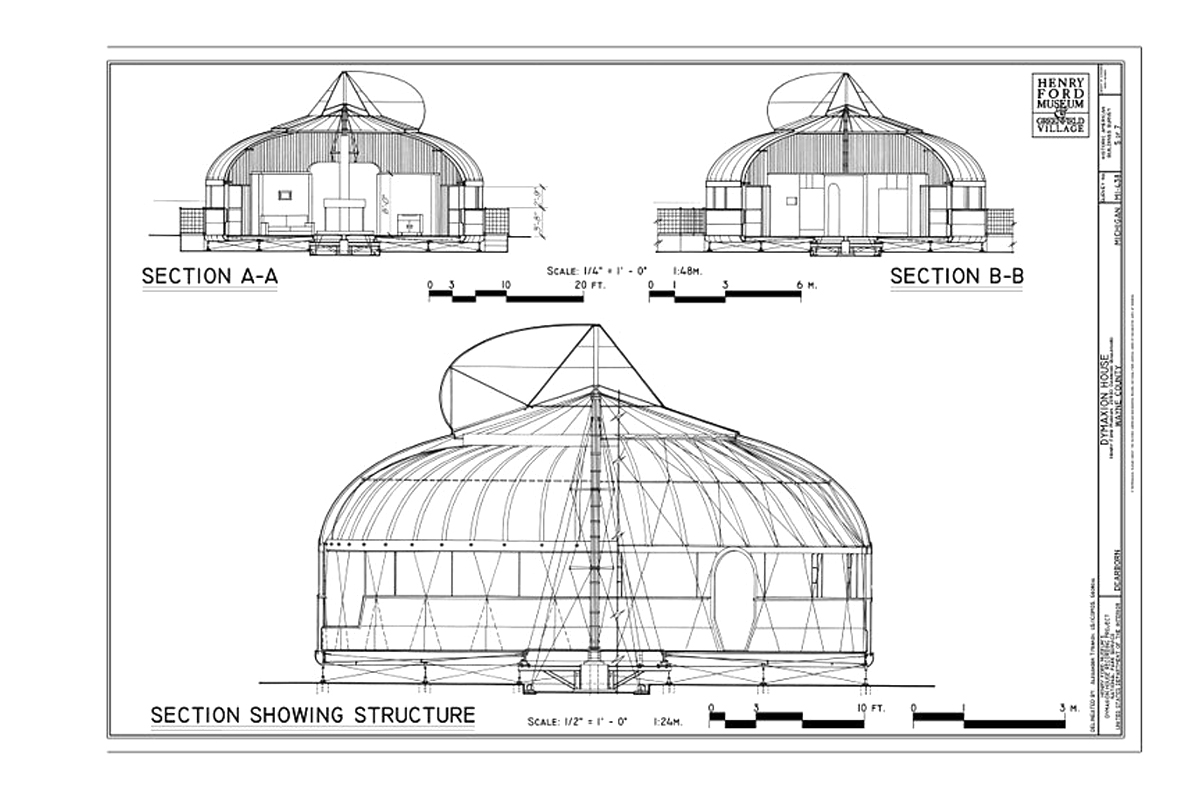
Cross-section drawing of the Dymaxion House, an innovative housing solution first developed by American architect and inventor Richard Buckminster-Fuller in the late 1920s.
Buckminster-Fuller’s lightweight design weighed just 1,360kg or 3,000lbs compared to the average weight of 150 tons for a home at the time in the USA. It used a light, central stainless steel mast or column to give the necessary tension to support the structure. The design also allowed the 1,100ft² house to be erected without the need to use a permanent foundation – you can imagine it as a robust umbrella!
Interior design of the Dymaxion Home
The circular structure contained a living room, two-bedrooms, two bathrooms and a kitchen with the window in the living room an impressive 33ft long. The house had a number of space-saving features including built-in closets that rotated out of the wall and a dustproof hat-rack located behind the bedroom mirror. Other innovations included the ‘O-volving’ shelving system which eliminated any bending down by rotating shelves to the correct level, bringing the clothes or sheets to you.
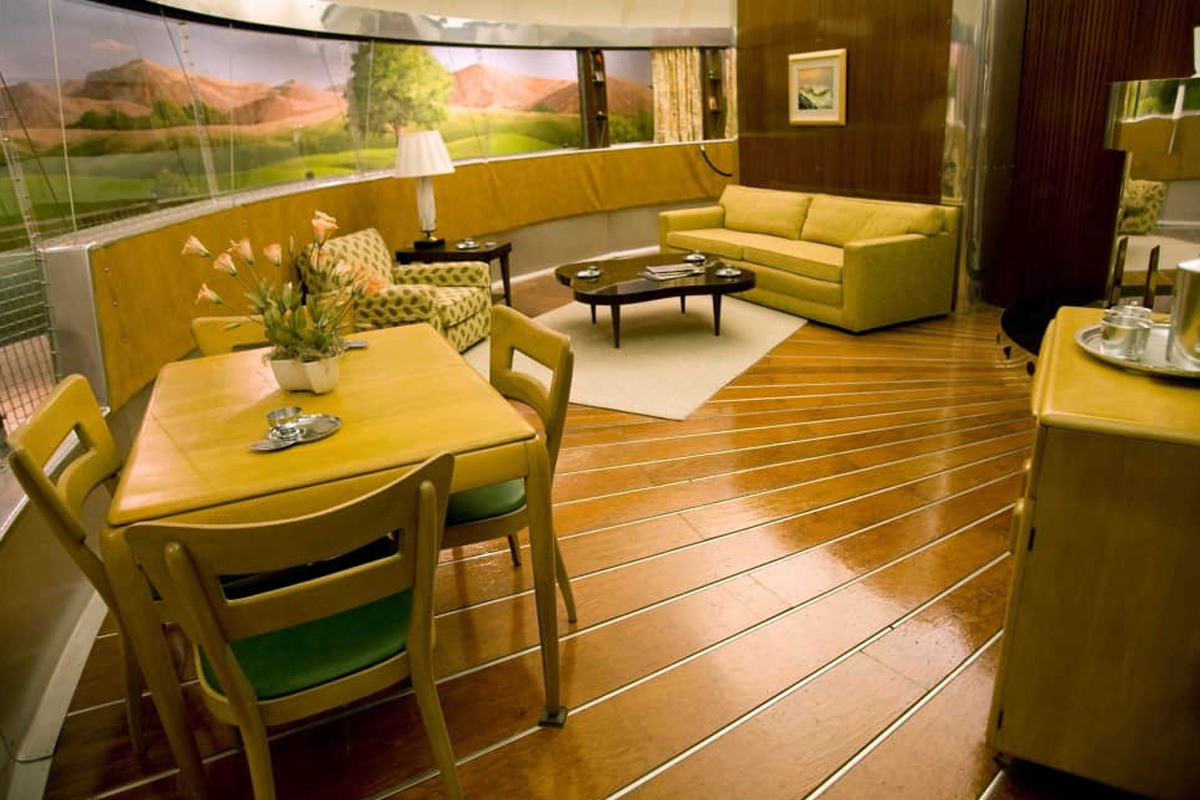
The interior of the Dymaxion House designed by Richard Buckminster-Fuller on display at the Henry Ford Museum in Michigan. The lounge contained a 33ft long window. Image from the Collections of The Henry Ford Museum.
Buckminster-Fuller also wanted the Dymaxion House to be as environmentally efficient as possible. The house heated and cooled itself by natural means as well as having a compact built-in air conditioner and heater. The house, beautifully fabricated out of aluminium, didn’t require painting and had minimal exterior maintenance needs.
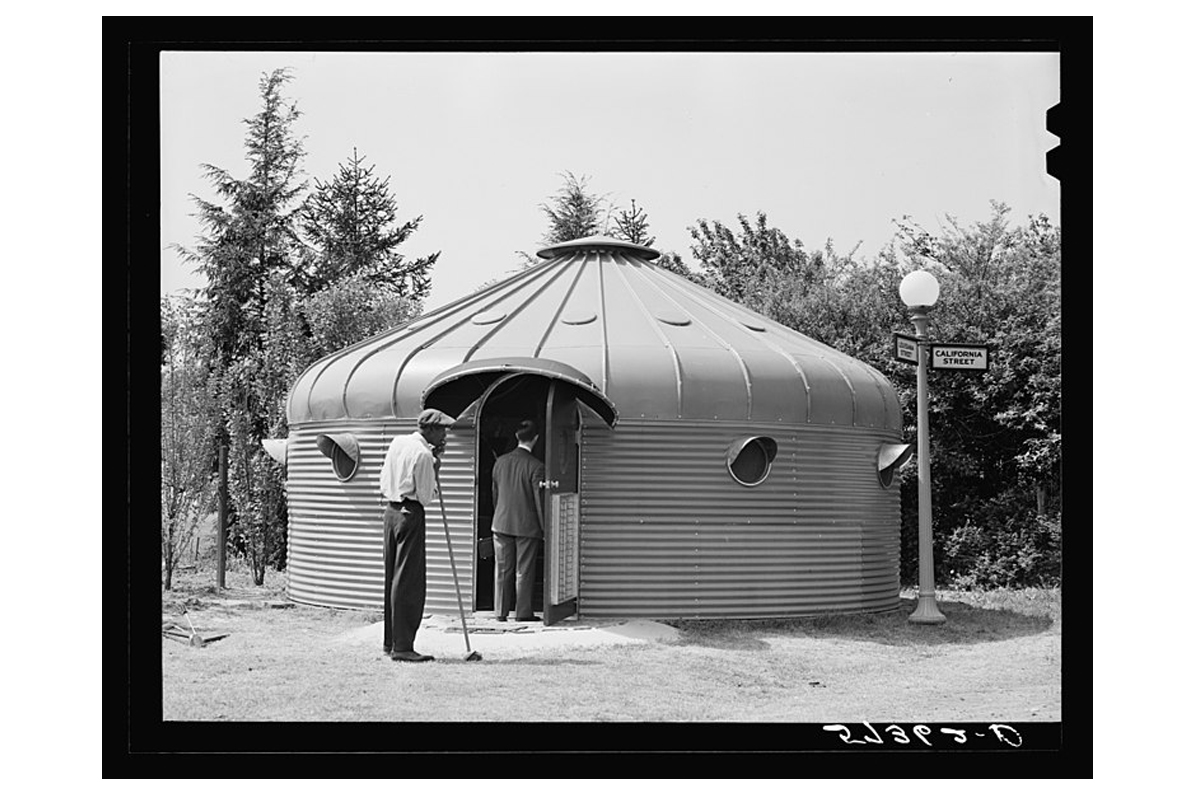
A 1940s version of the Dymaxion House designed by Richard Buckminster-Fuller. He spent many years perfecting his concept for a mass-produced, easily-assembled, resource-efficient home.
Roof of the Dymaxion House
The Dymaxion House had a remarkable revolving roof with an engineered downdraft that meant all the air contained within the building was changed every six minutes. A second advantage of the building’s air-flow was that it blew atmospheric dust downwards towards the skirting boards. The collected dust was then removed from the house via filters which significantly reduced the need for vacuuming.
There was also a greywater system in the roof that collected water for the toilets and a gutter on the inside to collect condensation.
Business plan
Buckminster-Fuller’s business plan was to lease units to buyers or sell each one for the price of a high-end automobile to be paid off over five years. That meant each Dymaxion House would carry a relatively steep price-tag of $6,000, which in 1945 would equate to around $86,000 in today’s prices.
In 1946, Fortune magazine saw a very successful road ahead for the futuristic homes. They described it as ‘a product that would have more significant social consequences than the introduction of the automobile’.
They were wrong. Buckminster-Fuller was too slow in perfecting his designs and only the prototypes ever made it into production. The project’s failure confounded many people who thought these spectacularly innovative dwellings were going to be one of the solutions to the post-war housing shortage.
The Dymaxion House, or the ‘dwelling machine’ as members of the public in 1945 called it, recently finished an extensive eight-year renovation (so much for low maintenance), and this restored unit is on permanent display at the Henry Ford Museum in Michigan.
I think this environmentally friendly, mass-produced housing solution would be more appreciated today. ‘Less is more’ was the philosophy that Buckminster-Fuller lived by which is definitely in tune with today’s global trends.
State of the art technology encompassing steel, glass and concrete.
I find fascinating in the construction process of any skyscraper that every piece that has been installed on site, has made a long journey from where it has been fabricated to its final position in the configuration of the building. In the construction of 22 Bishopsgate for example, some of the stone came from Italy, steel arrived from China, the façade panels came from Germany, the BMUs (those mechanical arms where the people that clean the façade hang from) come from Spain, some furniture in the lobby was produced in France…
Every beam, column, concrete block, door, toilet, handle, signage, has been fabricated and installed by a human being, and this proves that, still nowadays, construction is very much a handmade process. Of course some tools are still required to manage the heavier pieces of construction, but even then those tools, are actively controlled by people.
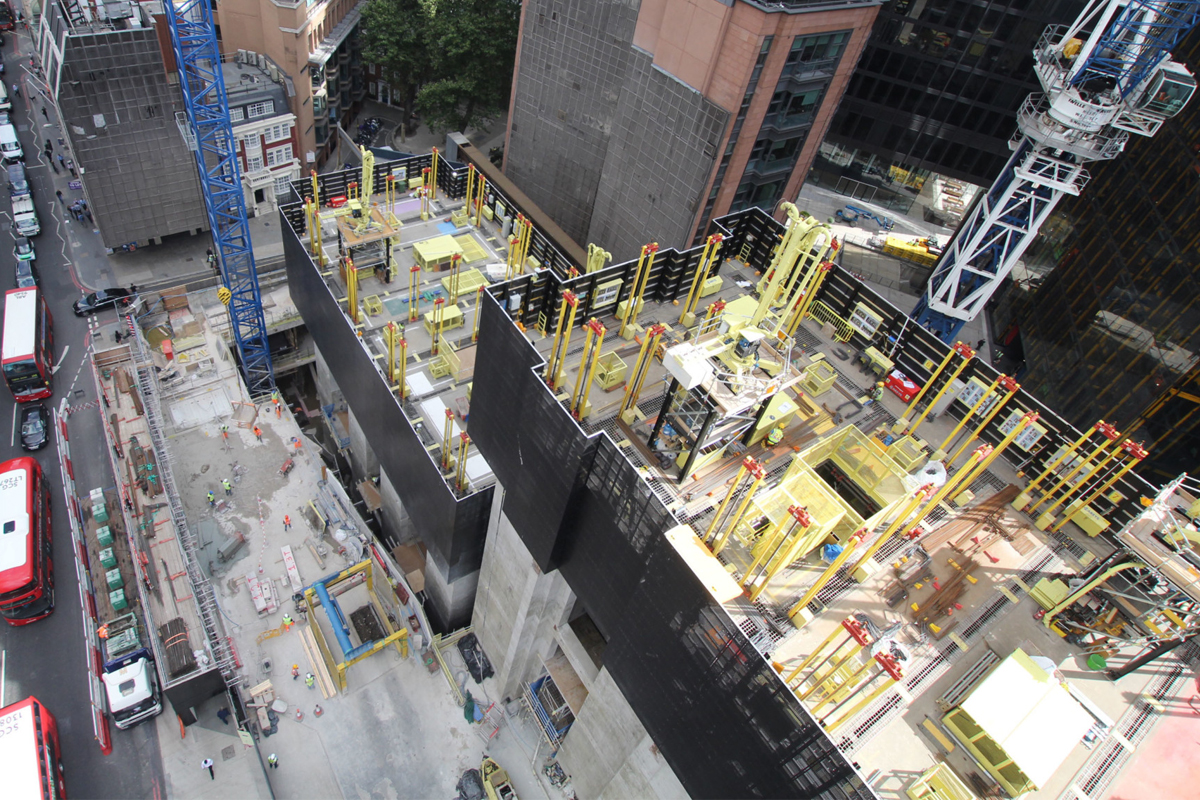
View of the building site from above, we can see how the multiple pieces of construction equipment are organized to allow for the builders to move around the site. 22 Bishopsgate designed by PLP Architects, construction by Multiplex.
Photo from Careys Design Team by Lobster Pictures.
A great team effort
The design team of a project of this scale, at peak times, probably involved around 25 architects, 8-10 structure engineers, some more Mechanical, Electrical and Public Health engineers, Landscape architects, Lighting Designers, Security Consultants, Façade Access Consultants, Fire Engineers, Planning Consultants, Visualization artists, Wayfinding consultants to name a few. Besides all these designers, there is an even bigger team working for the main contractor company full time on the project, and then there are the countless subcontractor companies involved in the construction.
And if all these people weren’t enough, an even bigger greater amount of people are involved in constructing the building with their own hands and their construction equipment. In order to finalise the job on time it has been required to have people working 24/7 and this implied having 1200 people spread around the site at once during construction peak times.
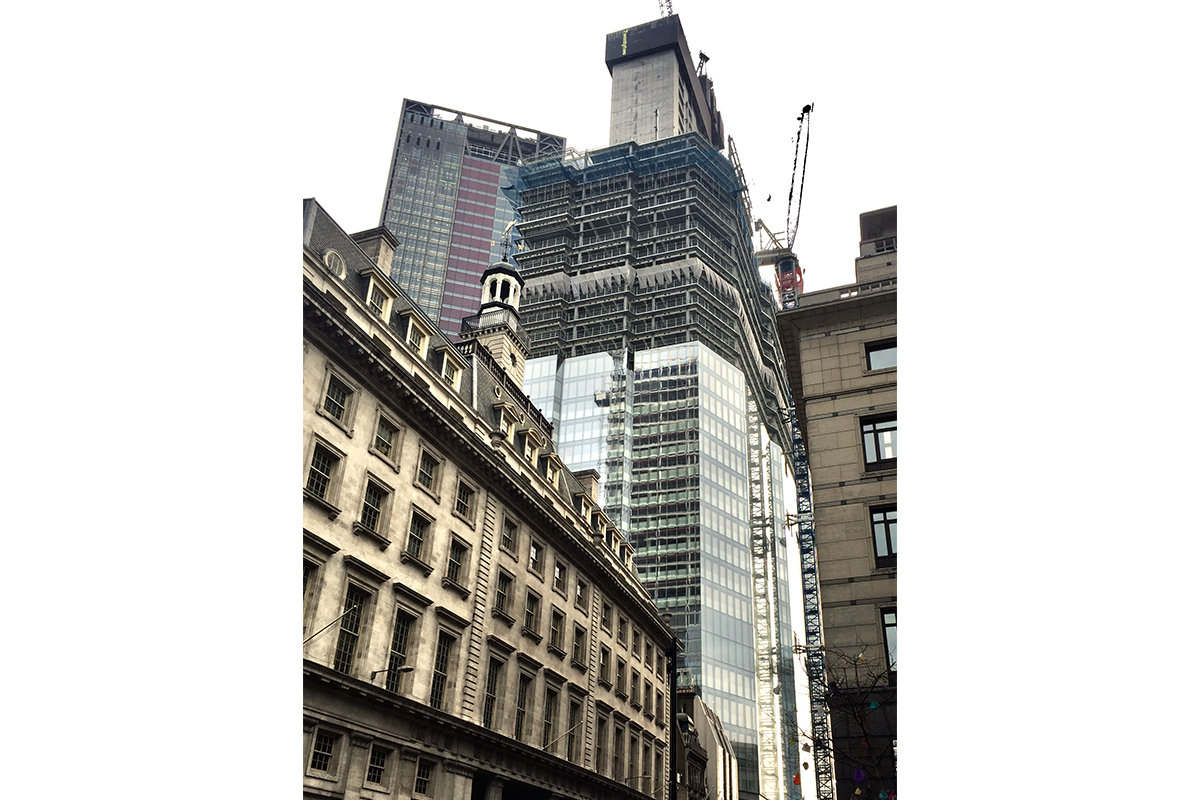
Images of 22 Bishopsgate at different stages of the construction process, we can see how the three main parts of the building: core, slabs and façade progress in a stepped sequence over time.
Photograph by Antonio Moll
Top down construction
Construction began by demolishing the existing core and cutting those parts of the basement slabs that were required to build the new core and to facilitate the construction of the new design. It was decided to use the Top Down construction methodology. This technique is often utilised to shorten the duration of the construction programme and the associated money that comes with it. It consists in starting to build the core from an elevated level, in this case from the ground floor. This way, construction can progress simultaneously above and below ground.
Temporary structural elements are built to support core. These usually occupy less space than the final configuration of the core walls would thus freeing space underneath and facilitating the execution of the works required below ground. These temporary structure elements are removed at a later stage accommodate the underground portion of the core.
This way, the works above ground level can start earlier because it is not needed to wait those 3-4 months required for the core to reach ground floor – in the case the core was built using the traditional construction method starting from the lowest basement and foundation level. Apparently, at one point during construction, the core reached level 20 before its basement levels and foundation had been built. This is an impressive feat of engineering without any doubt.
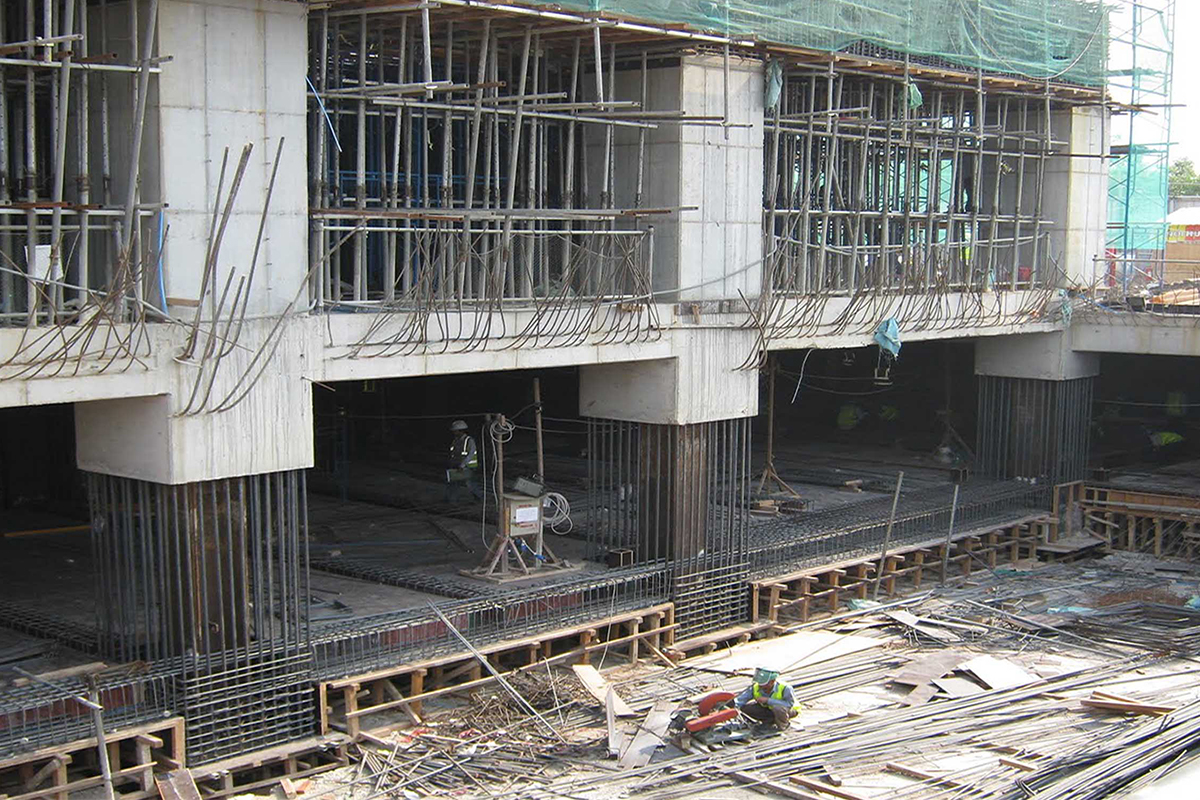
Image from a building site which is being built using the top down construction method, the above ground structure is already finished while the lower part is still due to be infilled with concrete.
Image from Engineering Discoveries.
A skyscraper structure
The structure of 22 Bishopsgate is primarily divided in two parts, the central core made of concrete and the surrounding beams and columns which are fabricated of steel. The gigantic core – its footprint at the ground floor is roughly 60 x 15 meters – is formed by walls that reduce their thickness as they rise to the top floors, accommodating the reduced structural demands of the upper levels in comparison to those of the lower ones. At the same time the footprint of the core also reduces as a result of the lesser number of lifts and services that reach the top floors. This is not uncommon in high rise structures.
The design coordination process of the structure of a building requires a continuous back and forth. Architects and engineers exchange drawings, mark-up comments and hold meetings on a weekly basis during the busiest times of the coordination. This exhaustive dedication is required to check progress and make sure that scheduled programme is met.
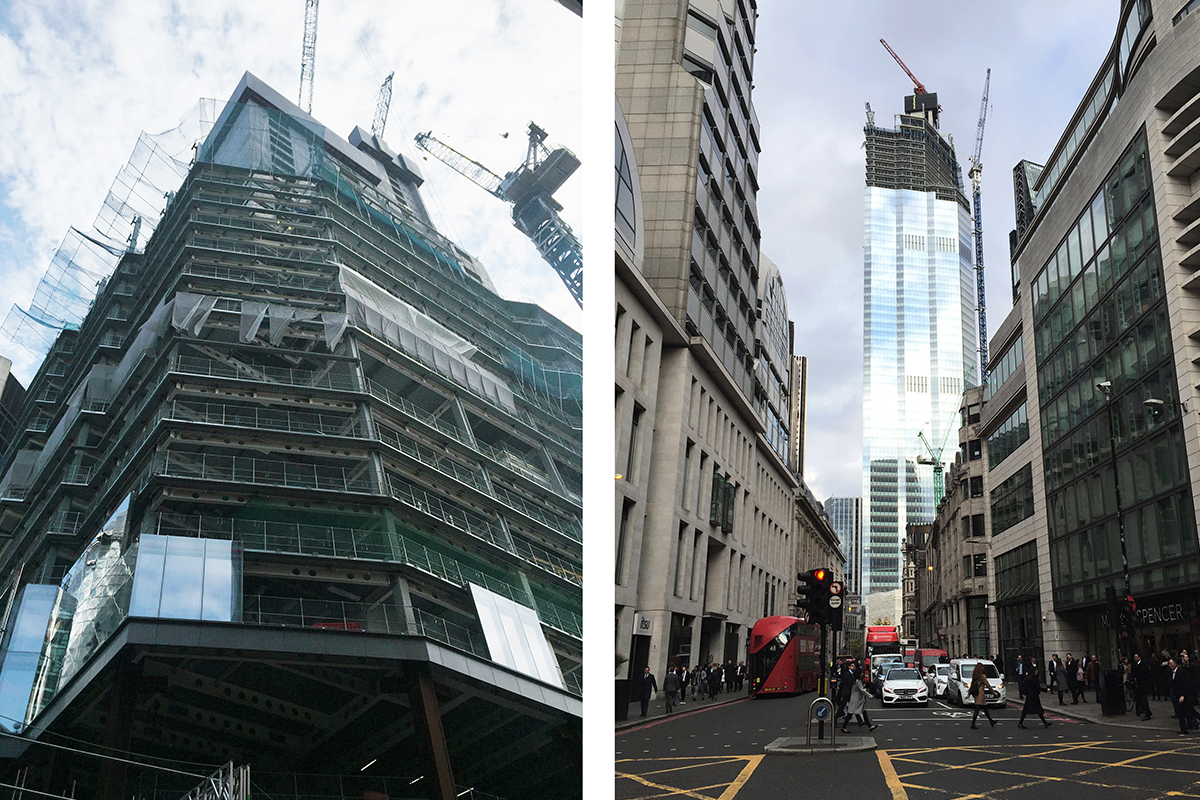
22 Bishopsgate during different stages of construction. We can observe the sequence in the construction of the main elements of the buildings: the core, the steel frame and the cladding.
Photographs by Antonio Moll
A bit of technical knowledge
The most interesting concepts of the overall functioning of the structure from my point of view are the lateral stability and the axial shortening.
We should understand lateral stability as the resistance of the building to fall sideways due to the action of the wind hitting the building, or an earthquake in a seismic area- luckily London is not one of these. In order to respond to the pushing forces of the strong winds affecting the top of the building at such height, the engineers designed a series of trusses that play the role of outriggers located at levels 25 and 41. These are gigantic steel structures that span from floor to ceiling and tie back to the concrete core. The main role of these structural elements is to restrain the building, helping it to stand still when the wind tries to bend it down.
On the other hand, the axial shortening affects the structure of a skyscraper vertically. As construction progresses and the building reaches higher levels, the entire building sinks marginally into the ground, we are talking of dimensions in the range of a few centimetres. And not only this, the structure also compresses and shrinks gradually due to the effect of the increased weight that it has to support as work progresses on site and more material and weight is added to the building. All of this has to be taken into account when designing the structure. Explaining it in a very simplistic way: columns are designed longer than required so that after the axial shortening occurs, they reach their nominal length so each floor remains at the exact level defined in the architectural project.
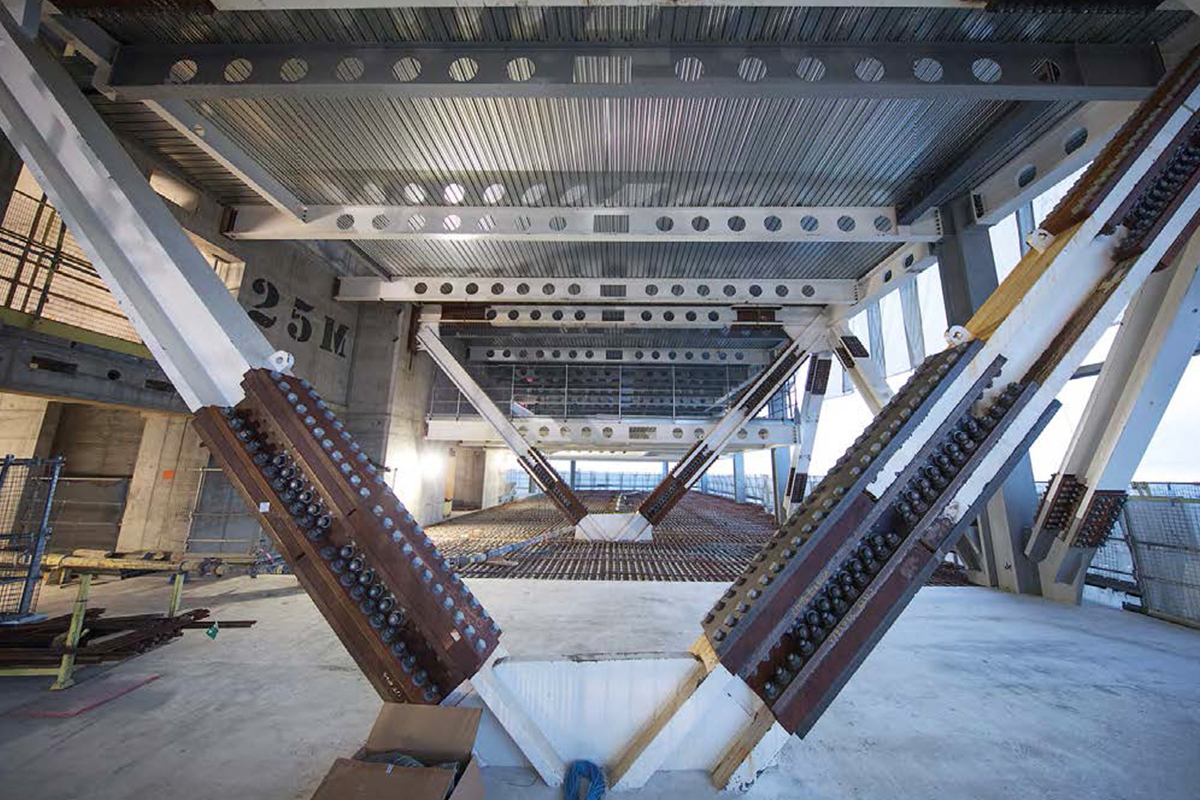
View of the outriggers at level 25, these structural elements provide lateral stability to the skyscraper and impede the lateral movement due to the action of wind.
Façade Panels
The skin of the building is composed of a double layer of glass with a pressurized cavity in between. This type of cladding is named under the acronym CCF which stands for Closed Cavity Façade. The entire envelope is divided in single panels, each of them of around 4m high and 1.5m wide that come from the factory ready to be installed in place. Each of the cavities of each panel is fed by a constant flow of air that keeps it over pressurized, like a balloon, improving the thermal performance of the façade.
The glass employs the latest technology to achieve a great level of transparency from the inside and a beautiful white reflection when seen from the outside that makes the building vanish, reflecting the surrounding environment and changing the tone as the different tones of daylight strike on the different faces of the building.
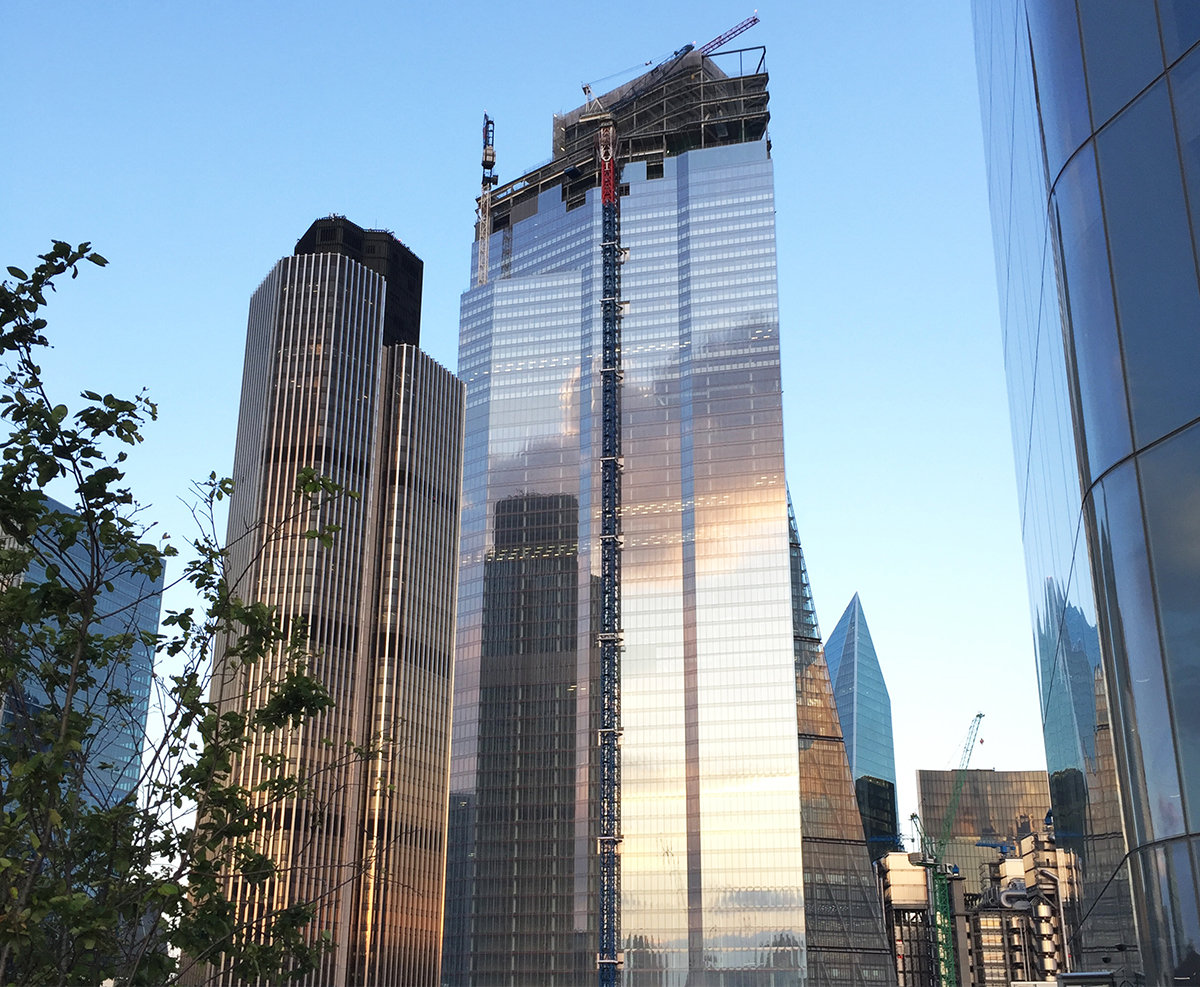
Tower 42 reflected on 22 Bishopsgate. The state of the art technology of the glass makes it vanish in between the surrounding environment.
Photograph by Antonio Moll.
My business interests require that I spend a lot of time in the United States with our stainless steel, PVD partners Kloeckner Metals Corporation at their Cincinnati plant in Ohio.
One recent weekend I was walking around Cincinnati’s Central Business District when I walked past a relatively non-descript and dilapidated office block. The building had a filthy brass commemorative plate bolted to it.
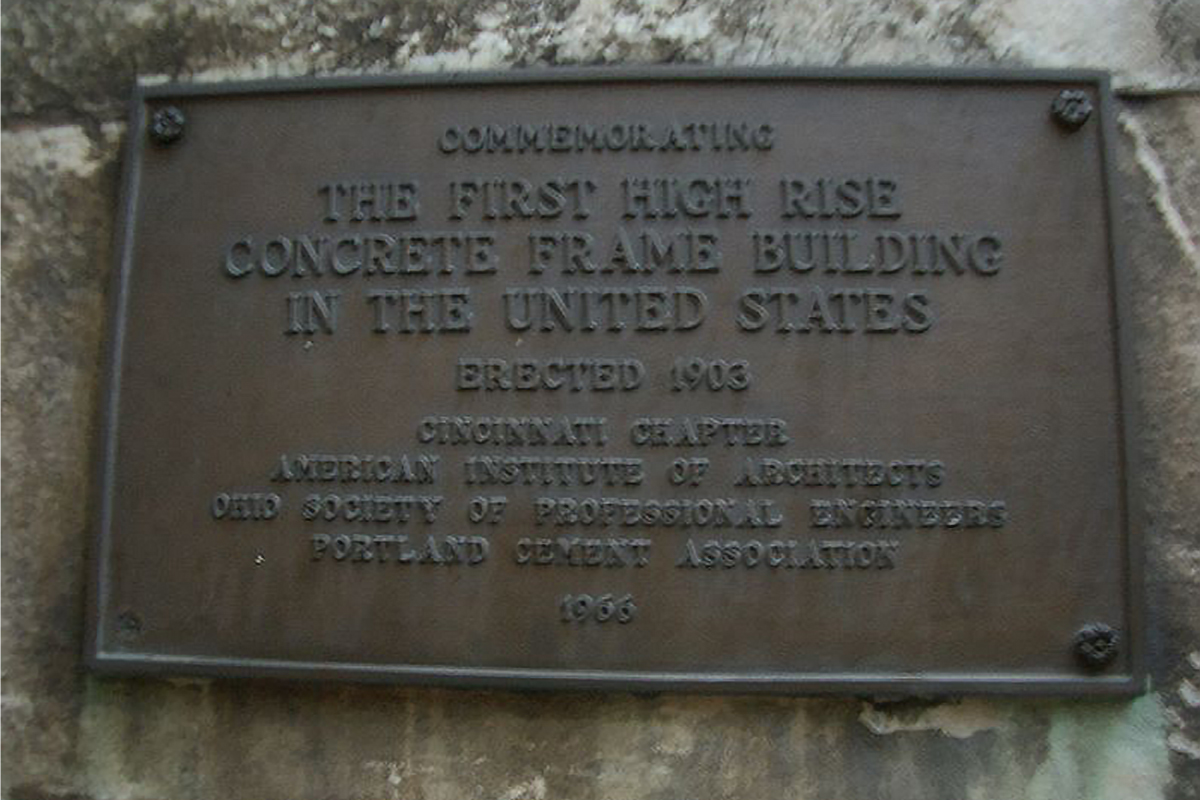
Brass plaque commemorating the Ingalls Building in Cincinatti, Ohio. Built in 1903, it was the first high-rise concrete frame building in the United States. Photograph by Charles Clark.
To my surprise, I realized that I had stumbled across the Ingalls Building – the first reinforced concrete high-rise structure in America. Before this remarkable building was constructed, the tallest concrete building in the entire world was only six stories high. Concrete is weak when subjected to pulling (tensile) forces and engineers feared a higher structure would risk collapsing under its own weight or wind loading.
Reinforced concrete construction
However, businessman Melville E. Ingalls and engineer Henry N. Hooper believed that, using the construction system patented in 1884 by the English engineer, Ernest Ransome, they could build much higher. Ransome’s method utilized casting concrete slabs around a cage of twisted steel bars, which allowed for floors, beams and joists all to be formed in concrete. This method also gave the building additional favourable properties such as excellent fire resistance and was a very rapid and economical construction method.
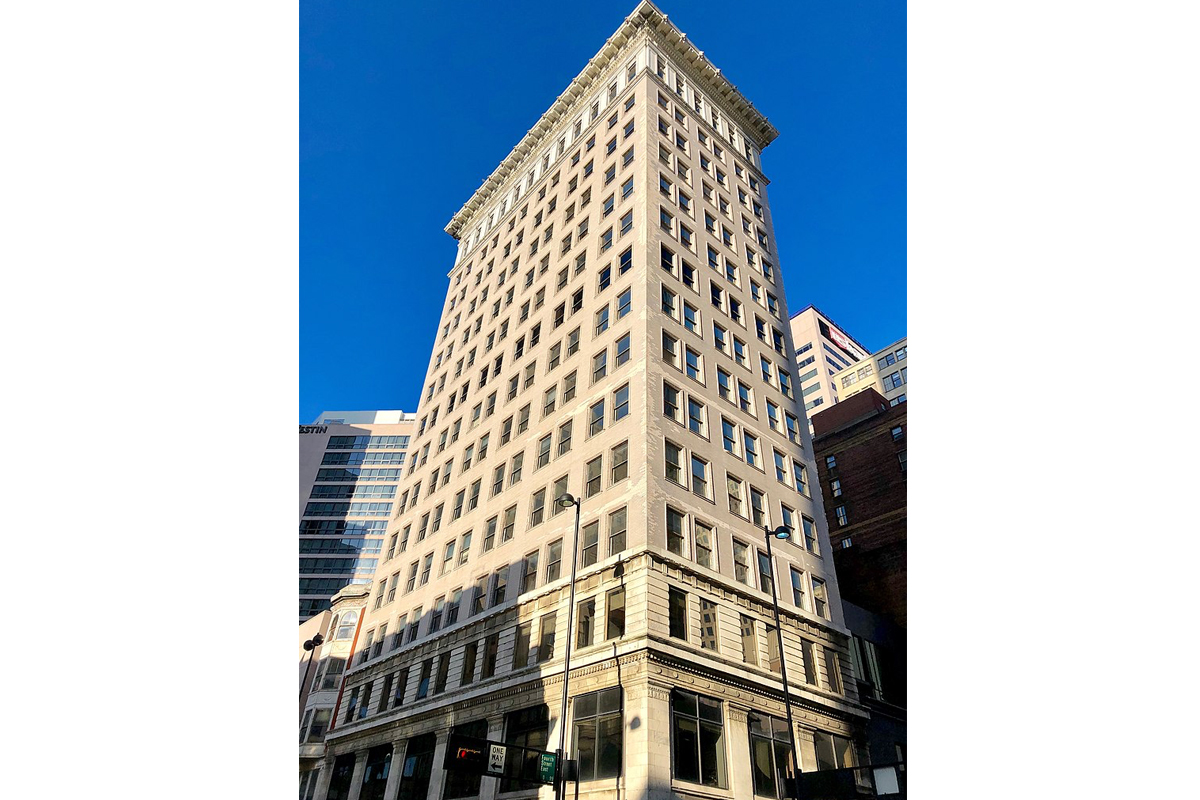
The Ingalls Building in Cincinatti,Ohio. The first concrete skyscraper in the United States, it was designated a National Historic Civil Engineering Landmark in 1973.
The plan was to use this new system of reinforcing concrete to build a sixteen-story office block and architects Elzner & Anderson were commissioned to design the ground-breaking, ‘skyscraper’. It took two years for Ingalls, the principal investor of the project, and Hooper to convince the city authorities, sceptical of this new construction method, to issue a building permit.
Construction of the Ingalls Building
Hooper decided that the structure of the building would be a monolithic concrete box, with the beams, floors, stairways and columns all made from reinforcing bar and concrete. All the reinforcing bar was interleaved and wired together so that the entire building was technically one piece and there was no need to use steel beams in the building.
The building took shape very quickly, and the construction team were able to produce three floors a month, working out to approximately 76 cubic meters of concrete per ten-hour shift.
The architects used the school of Beaux-Arts for the exterior design of the building and the first three floors of the concrete frame were clad in white marble. The floors from 4 to 15 were a resplendent grey glazed brickwork with the 16th floor, and the cornice above, all clad in terracotta that had been glazed white.
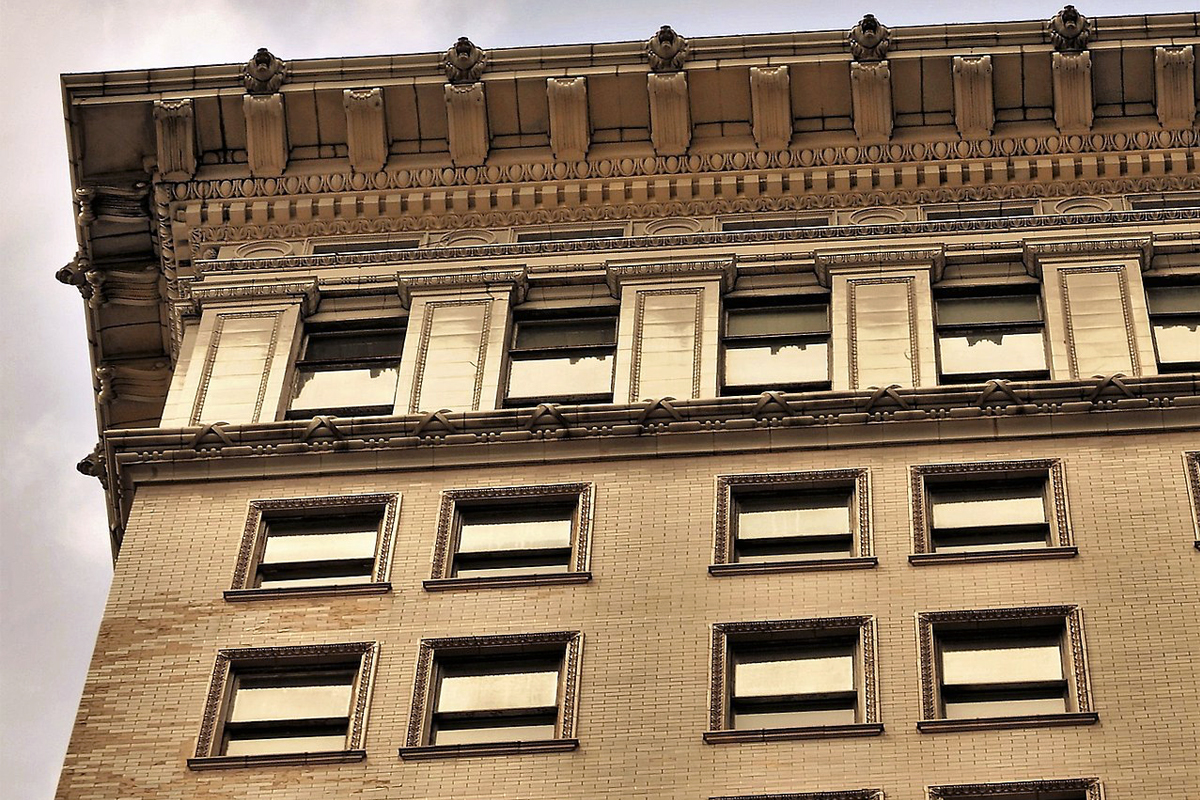
South-facing details of the upper floors and cornice of the Ingalls Building in Cincinatti. Designed by architects Elzner & Anderson at the turn of the 20th Century.
Photograph by Hhelvey.
The first concrete-frame skyscraper
On the day the building was completed and the supports were removed, one reporter sat up all night waiting for the building to collapse so that he could be the first to report on the disaster. Fortunately for all concerned the building confounded its doubters who could only stand and marvel at this structure soaring an unbelievable sixteen stories into the sky above the city.
Ingalls and Hooper’s success meant that reinforced concrete construction was gradually accepted as a solution for high rise construction, not only in the United States but the entire world. It is beautiful to think that all the stunning high rise concrete buildings around the world owe their existence to this neglected, old tower block in downtown Cincinnati.
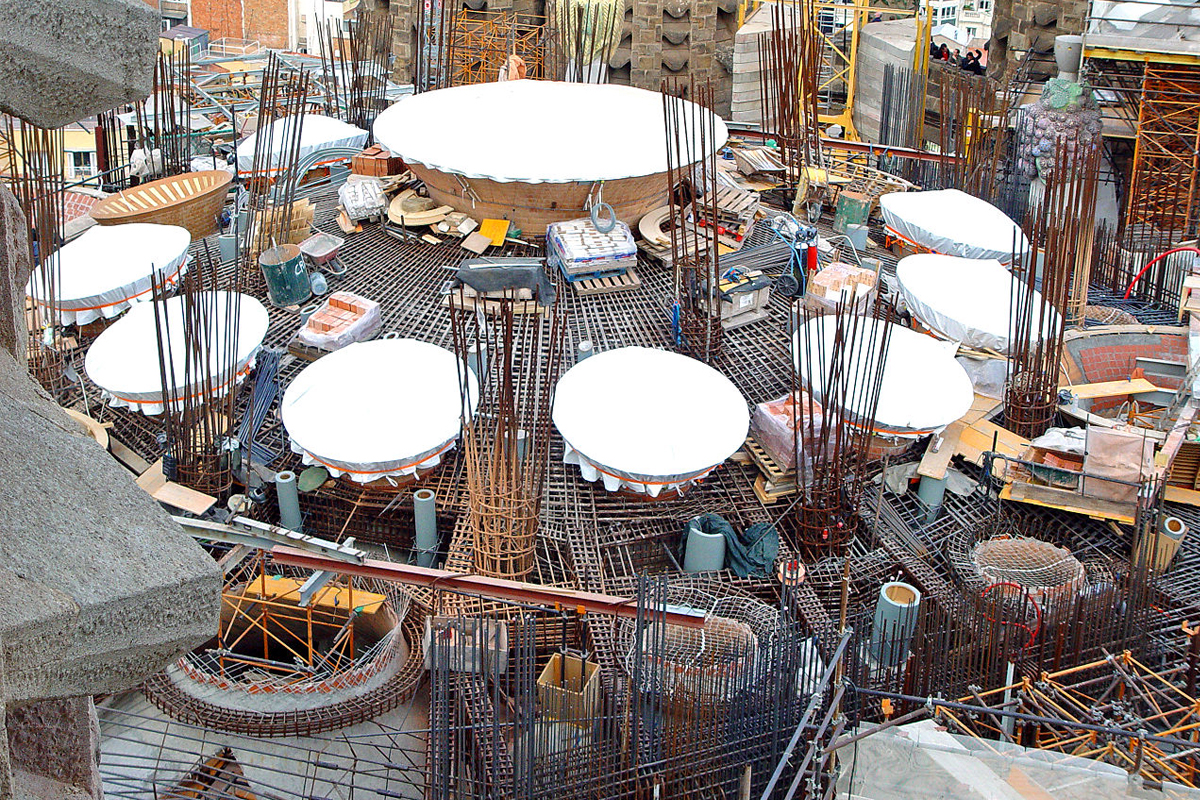
The roof of the Sagrada Familia Basilica in Barcelona under construction. Concrete reinforced with steel bars is the method being used to erect this famous building.
Photograph by Etan J. Tal.
Reinforced concrete construction is now so successful that many of the world’s most famous buildings utilize this tried and trusted construction method. This includes the Sagrada Familia Basilica in Barcelona and the world’s tallest building, the Burj Khalifa in Dubai, which is an astonishing 828 metres tall.
JAUME PLENSA – “Poetry can seriously damage your health”
Content in grams of an adult male weighing 70kg.
Water | 41,400 | Mg | 21 |
Fat | 12,600 | Cl | 85 |
Proteins | 12,600 | P | 670 |
Carbohydrates | 300 | S | 112 |
Na | 63 | Fe | 3 |
K | 150 | I | 0.014 |
Ca | 1,160 |
Barcelona 1996
Jaume Plensa, Sombras y Textos 1990-2007, Galaxia Gutenberg – Circulo de Lectores, 2008, p.39.
Barcelona has been a city that during the 20th century served as the operational base of many internationally acclaimed artists like Picasso, Gaudí, Dalí, Miró or Tàpies to name a few of the most famous.
Jaume Plensa (Barcelona, 1955) refers to them as his family, his friends. He was raised under their influence and nowadays he is considered one the most internationally recognised Spanish, or Catalan, artists of his time.
He describes himself as a classical artist interested in the sound and texture of materials, the human body, the face, the language. As a kid of his time he likes to utilise the latest technology to express his ideas. He often talks about pairs of concepts like letters and languages, individuals and societies, body and soul, light and darkness. It appears that some of his preoccupations are shared with those of Antony Gormley. What’s the relationship of the human being and the transcendental, with that world of energy and ideas? More interested in posing questions than offering answers, defends that the curious attitude is the engine of progress and development. The beginning of the creative process.
Plensa’s work can be organised in families of pieces around a common topic. Human heads, letters of different alphabets that come from his love of poetry, or huddled human figures protecting themselves from the environment that he then places in both the urban and the natural landscape.
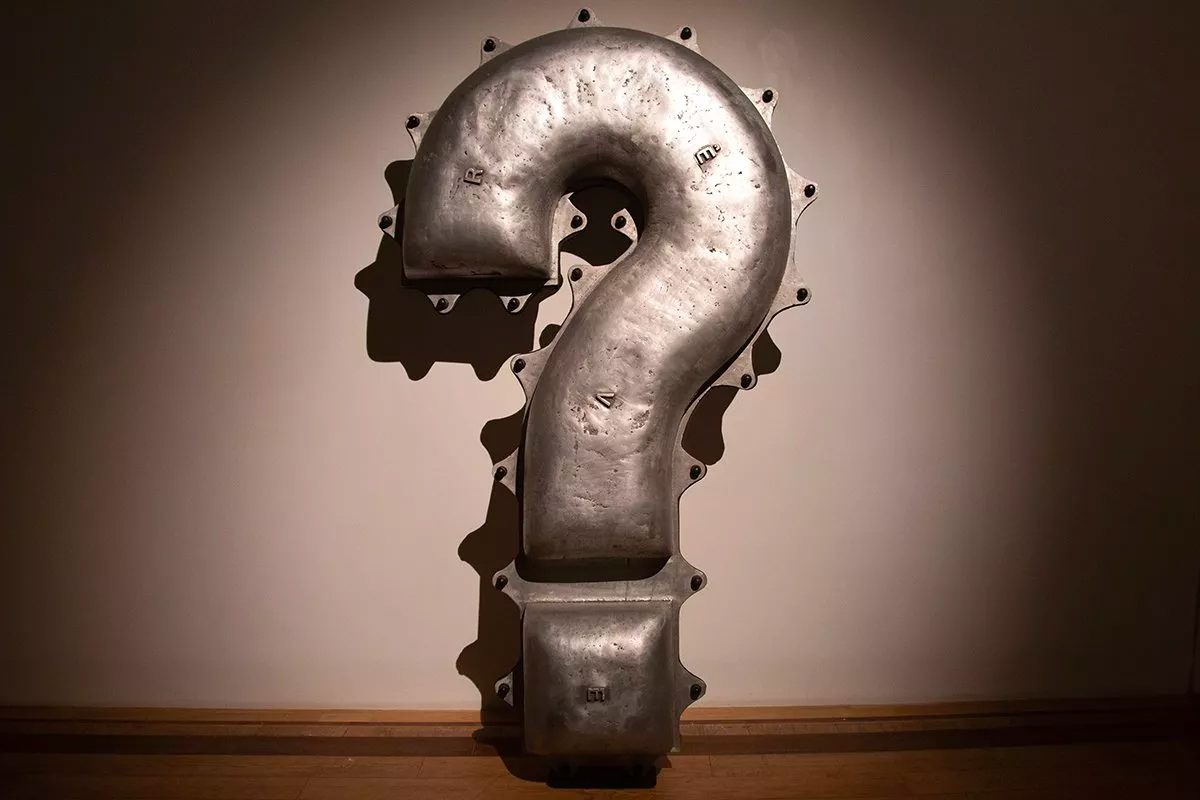
Jaume Plensa, Florence II, 1992. This 2m tall question mark made of steel and aluminium with the word RÊVE – meaning “dream” in french – engraved. It could be understood as a representation of the artist’s question about how to sculpt a dream.
Bringing the landscape inside the sculptures – The wire heads
“Nuria and Irma” represent the heads of two girls, whom he probably met at some point. They seem to be between eleven and fourteen years old, an age when they are no longer girls but they are not yet women. They face each other establishing a kind of dialogue. They are made of a beautifully executed stainless steel wire mesh and have their eyes closed, alluding to that introspection moment that also Gormley looks for in his work.
Different shades of grey draw the lines that make the sculptures appear in front of us. He says that this transparency allows him to bring the surrounding landscape inside the sculptures and let the people see the shape of a head from the inside.
The wires seem to become rays of light and this way one could say that he’s used technology in a reverse way, he has given a physical dimension to a hologram. After observing part of his work it is fair to say that he seems to want to bring to the physical world those manipulations that computer software allows him to explore.
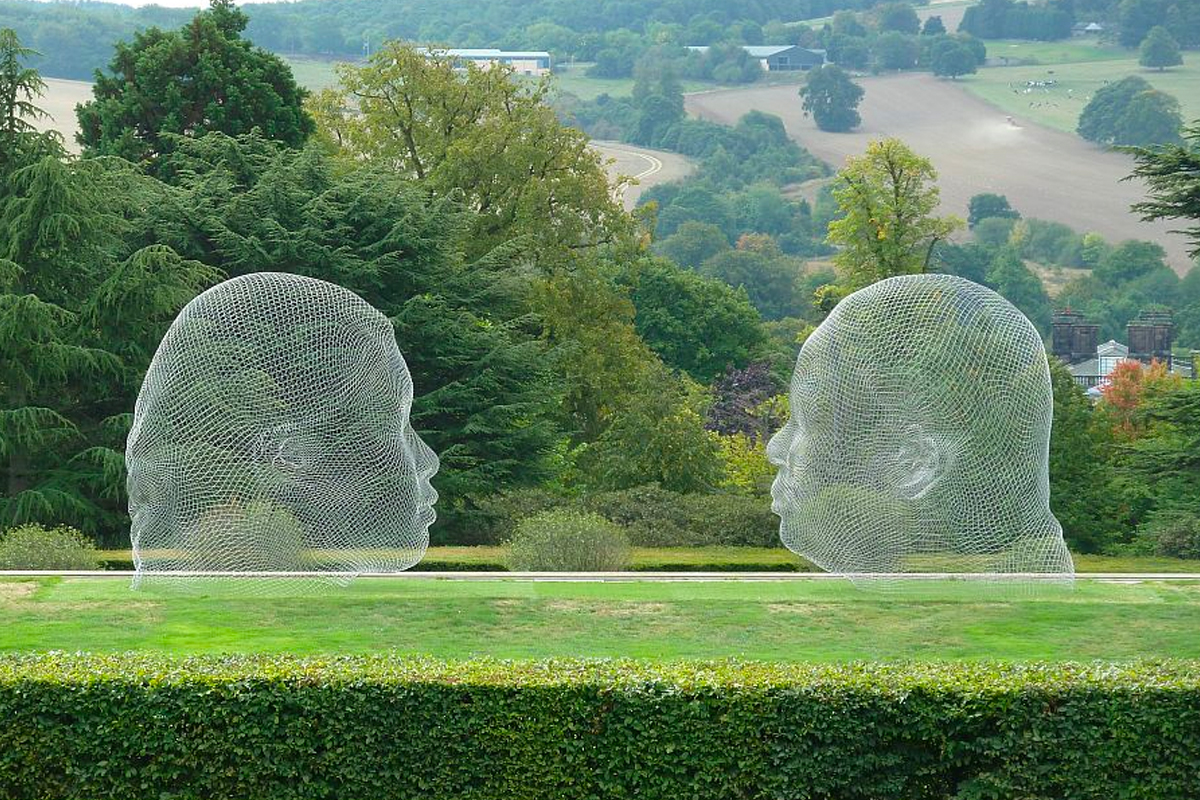
Jaume Plensa, Nuria (2007) and Irma (2010) in stainless steel wire mesh at Yorkshire sculpture park. By putting the two facing each other with eyes closed, the artist refers to the internal dialogue of each and the relationship with the surrounding landscape.
An evolution of this work, three times bigger this time, can be seen at the entrance of a skyscraper in Calgary. “Wonderland” is twelve meters tall and by means of increasing the size of the sculpture, he establishes a balanced relationship between the piece and the buildings around. This also permits him to define openings either side of it through which people can enter and experience the space enclosed by the mesh.
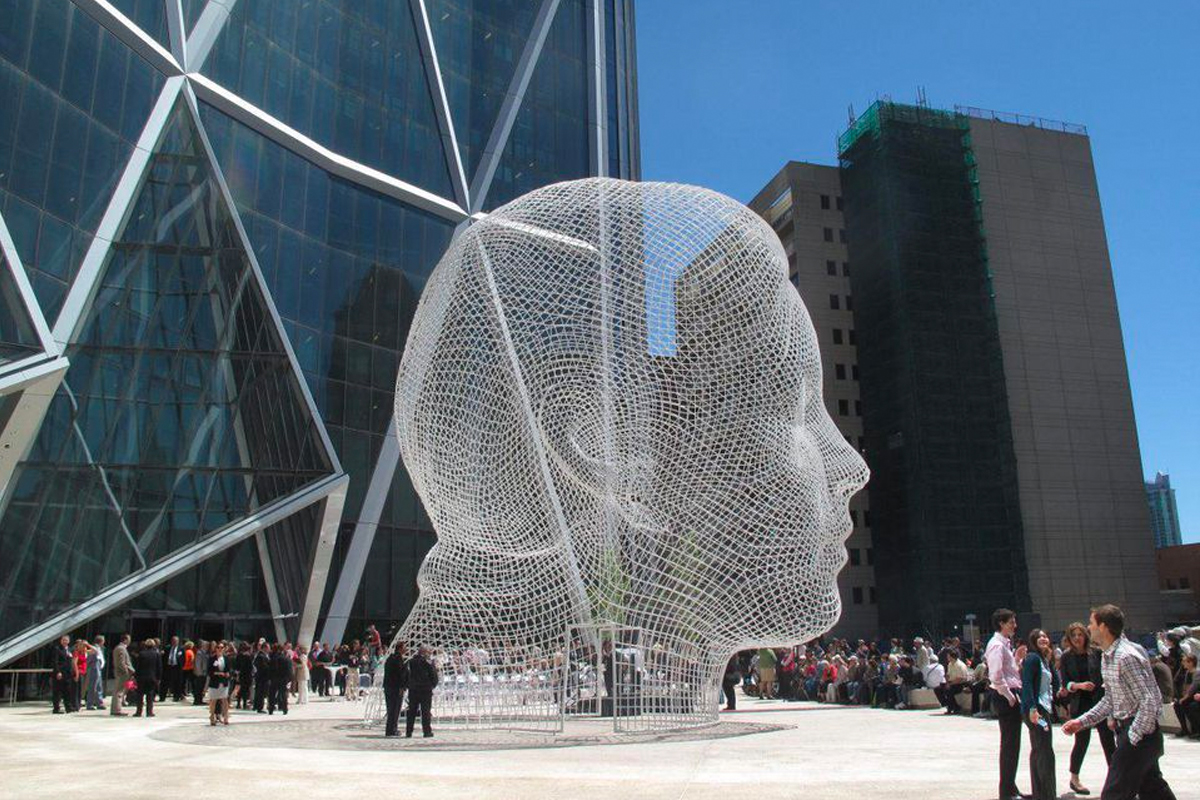
Wonderland, Calgary (2012). The sculpture made of white painted stainless steel receives visitors to the building behind. The two openings on either side allow people to pass inside and through it. Photo Galerie Lelong.
Discovering different cultures through letters and languages
Plensa’s father was an avid reader and the little Jaume grew up in a household full of books. He recalls being curious about the back of the letters, that side that’s always hidden to us because letters are usually two-dimensional.
Letters, like people, mean little or nothing by themselves. But when they join together they form words, words form sentences, sentences form texts and so on. One can trace the same associations with human beings, groups, cities, countries… For Plensa, a language and its calligraphy is a great tool to understand a culture and its people.
I haven’t travelled the world as extensively as Plensa has, but I agree with him that all cultures have more things in common than things that separate us. We all share similar concerns and want similar things. We want to relate to others, to belong to groups, we want our families to be happy and healthy…
“Spiegel I and II” are born of the combination of this love for texts, cultures and people. Letters of different languages are combined indistinctly to shape two human bodies curling up and facing each other. The scene has an atmosphere of intimacy in the middle of a vast open space, to the point that one feels like interrupting a private encounter.
The figures don’t have faces, preserving their anonymity. Being four meters high one can enter the enclosed space and observe the hidden side of the letters, the one the artist was always curious to see.
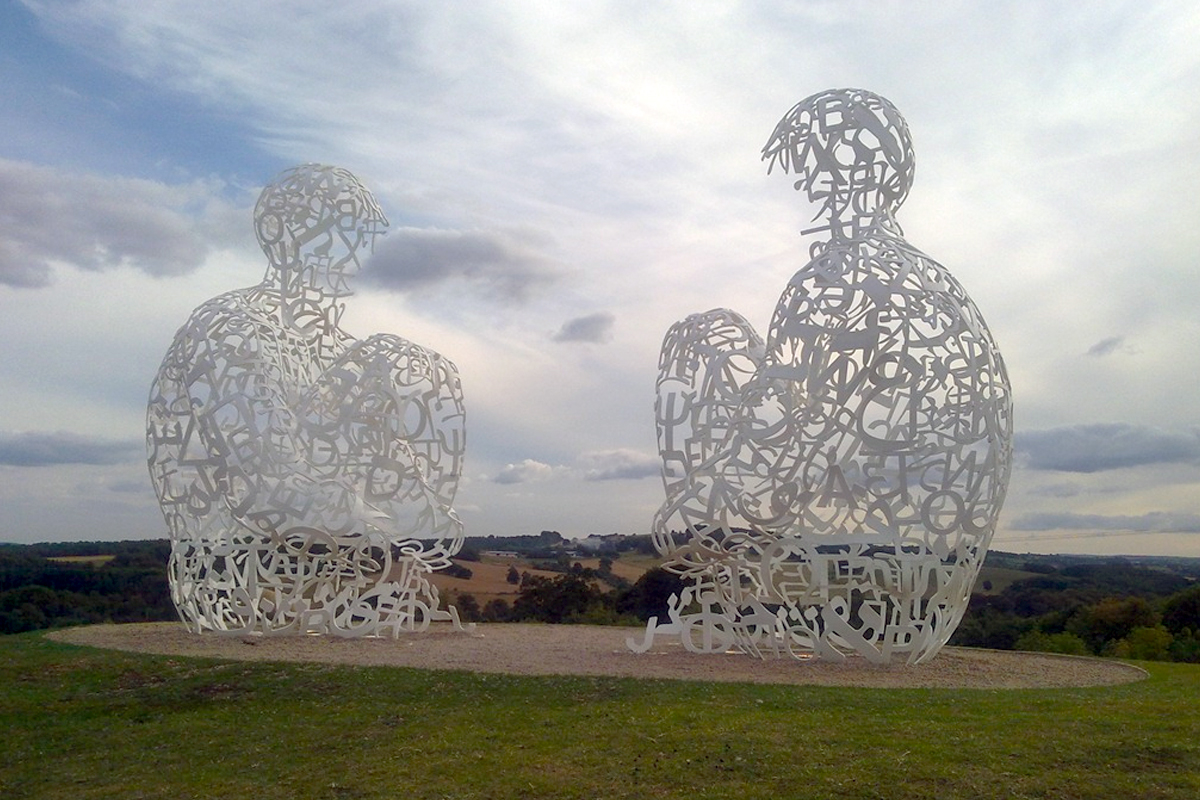
Jaume Plensa, Spiegel I&II (2010) at Yorkshire Sculpture Park, 2011. The steel sculptures facing each other establish their own dialogue leaving the visitor with the impression of witnessing a private encounter. Photograph by Down by the Dougie.
“Alma del Ebro” on the other hand presents just one figure and turns the focal point to the interaction of the sculpture with the people approaching it. This was the first time I experienced Plensa’s work in real life. I was impressed by the twelve meters high sculpture, there is something magical about scaled up human shapes.
It was built as a commemoration of the Expo 2008 held in Zaragoza about water and sustainable development. Probably, as a tribute to its home country, Plensa decided to reconstruct this body using only white painted steel letters from the latin alphabet. According to the artist the figure “is looking inwards more than outwards” and “the intention is precisely to invite the visitor to share this introspective moment”.
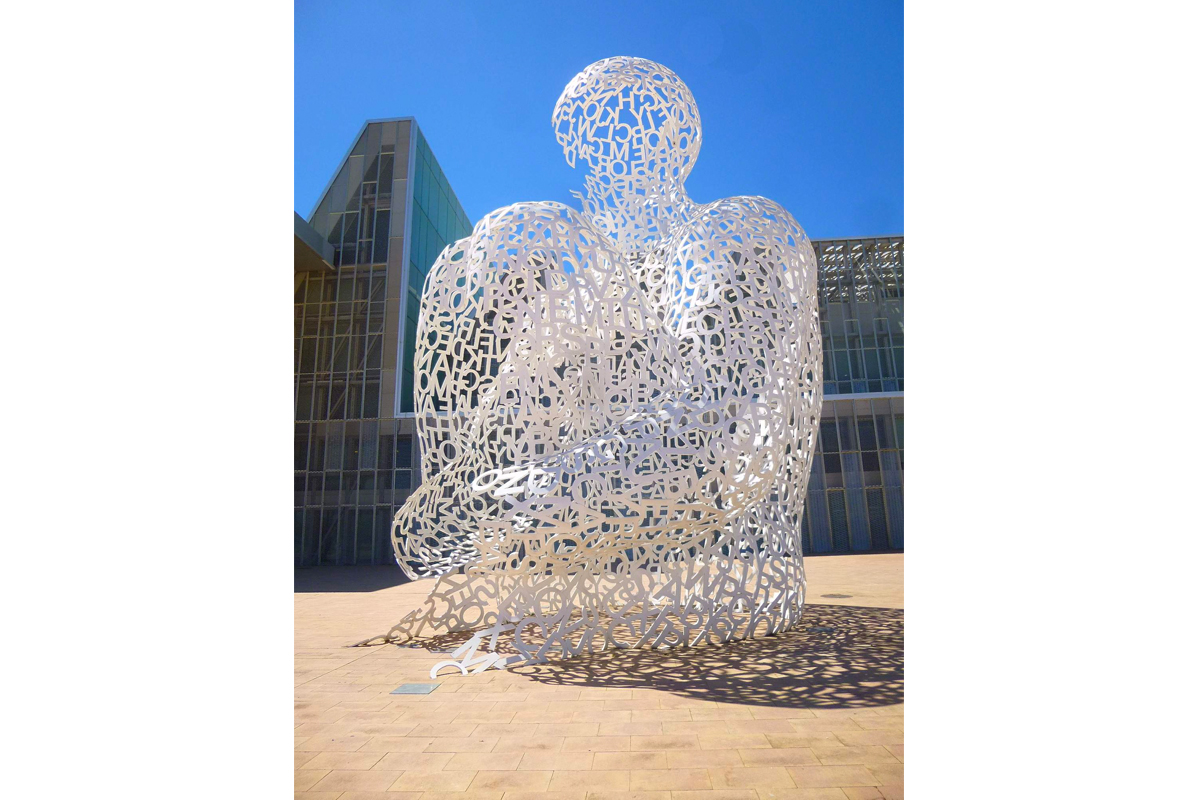
Jaume Plensa, Alma del Ebro, Zaragoza (2008). The 11 m high sculpture traces the pass of time on the floor with its changing shadows. It invites the people to enter the space enclosed and reflect about themselves.
The use of light as a sculpting material: Chicago and Sestriere.
Plensa has also explored the use of light in some of his works in both the landscape and the urban environment.
Crown Fountain in Chicago is probably the work that put him in the spotlight of the international art scene. Plensa won the competition organised by Lester Crown and his design was chosen over proposals by Maya Lin and Robert Venturi.
His idea has proved to be a great success. Not only as a work of art, but also as a public space that citizens love to use. Children gather in groups waiting for the next water jet to emanate from the face projected on the screen. This interaction between art and audience is what the sculptor is most proud of.
It comprises two fifty feet tall towers made of very transparent glass blocks placed seventy meters apart. They display faces of a thousand anonymous people of Chicago that change every few seconds. In between towers there is a very thin sheet of water over a black stone pavement which Chicagoans enjoy as if it were a beach during the scorching summer days.
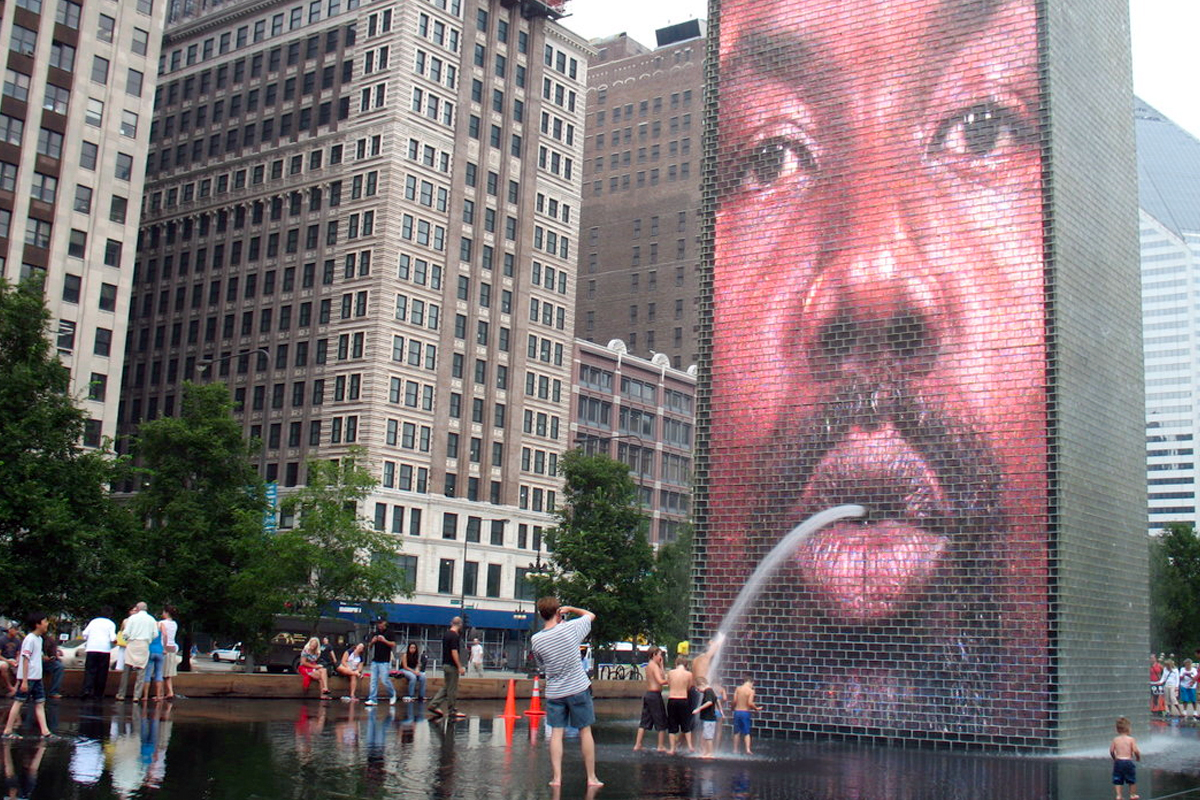
Jaume Plensa, Crown Fountain, Chicago (2004). Two towers made of glass blocks display images of anonymous people that discontinuously throw a water jet. Here Plensa reflects on the role of public fountains and the interaction of art and audience.
In 2006, as a commemoration of the Winter Olympic Games in Torino, a series of artists and architects teamed up in pairs to explore issues related to art and architectural research using ephemeral materials like snow.
Jaume Plensa and Foster + Partners’ response was a 20m diameter and 50 cm tall circle engraved in the snow. It showed the GPS coordinates of Foster’s studio in London, Plensa’s studio in Barcelona and the location of the piece in Sestriere.
It was an artistic installation that combined the precision of a contemporary tool with the poetry of the white landscape of the Alps. The snow started melting a few days after the work had been finished. All that remains is a handful of photographs as a testimony of the collaboration between the artist and the architects in a certain place at a certain time; and a reminder that, in the end, all things man made are essentially temporary.
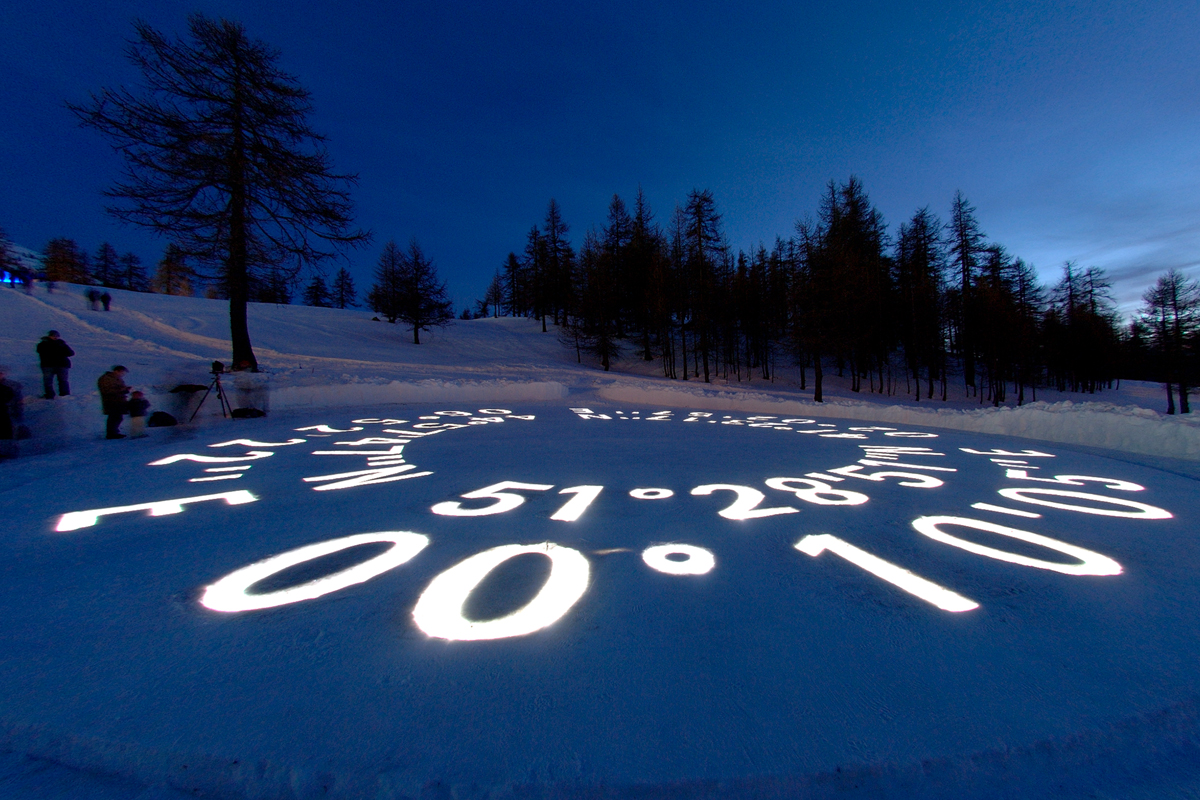
The snow show (Sestriere, 2006). Three GPS locations engraved in the snow forming a circle to commemorate the Winter Olympics in 2006: the location of this point in Sestriere together with that of Plensa’s studio in Barcelona and Foster + Partners’ studio in London.
If you ever find yourself in New York State, in the city of Albany, take a walk to the Rockefeller Empire State Plaza. There you will find The Egg Theatre – a centre for the performing arts. The Egg’s design is the very definition of brutalist architecture. This concrete structure would fit into any secret military base or be a fantastic setting for a James Bond villain’s headquarters. There are no windows to be cleaned, just thousands of square feet of reinforced concrete.
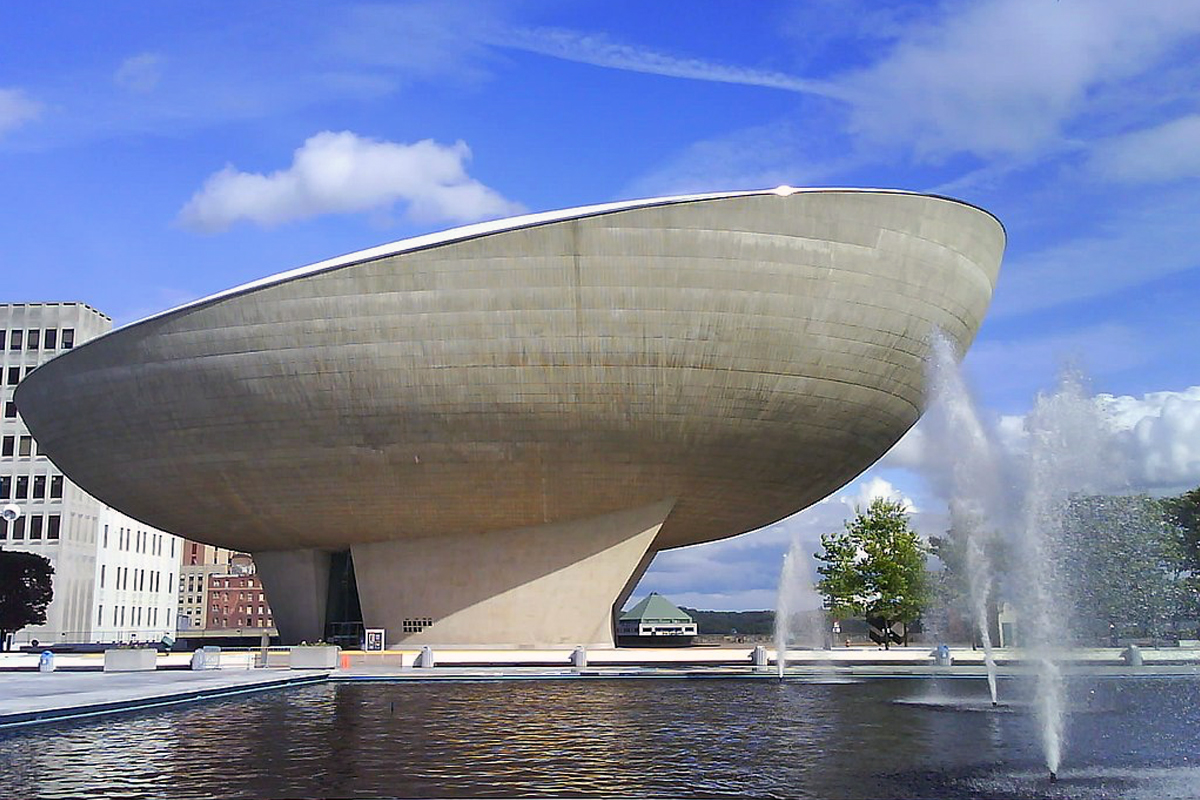
The Egg designed by Wallace Harrison in Albany, New York State. The theatre is an example of brutalist architecture constructed from reinforced concrete without windows.
Photograph by Nitant23
The project started construction in 1966, and was completed a mere 12 years later in 1978.
The Egg is now the home of the Ellen Sinopoli Dance Company which has been resident at the theatre for 28 years.
Rockefeller Empire State Plaza
The architect was Wallace Harrison, a partner in the architectural practice of Harrison & Abramovitz, who were known as proponents of modernist design. The company’s portfolio includes many iconic buildings in New York City such as The Rockefeller Centre, the United Nations Headquarters and the Exxon Building.
Harrison spent 15 years working on the whole development of the Rockefeller Empire State Plaza, a brutalist architectural development that dominates the skyline of Albany. The city is the capital of New York State and sits on the banks of the Hudson River about 123 miles from New York City. Harrison was close friends with Governor Nelson A.Rockefeller and they sketched out the initial layout for the whole project in Rockefeller’s private plane.
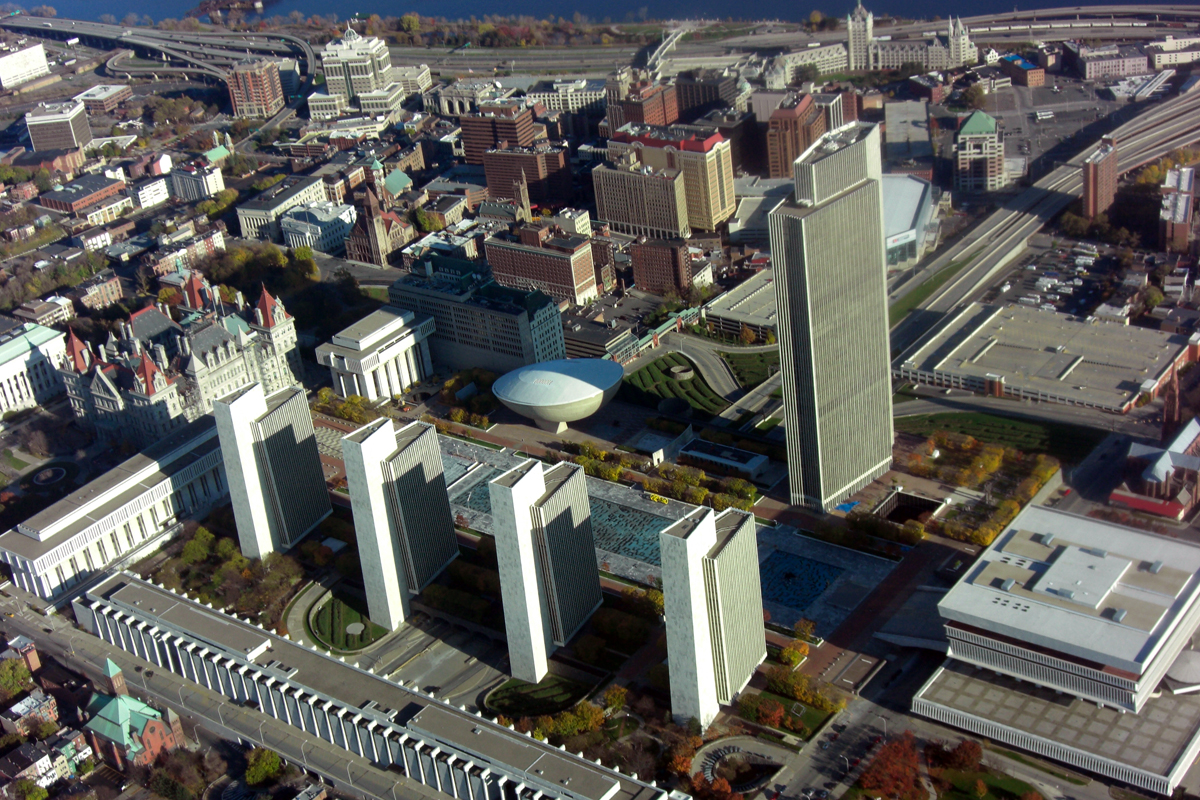
Aerial photograph of the Rockefeller Empire State Plaza in Albany, USA. The complex of state-government buildings was built between 1965 and 1976 at a cost of $2 billion.
The budget for the project was $250 million, but after many delays and cost overruns the final cost was closer to $2 billion, which is almost $18 billion in today’s money. Today over 17,000 government employees work in the area.
Unique design of The Egg
Architecturally speaking, The Egg is one of a kind. It is an enormous egg-shaped bowl that is supported by a central pedestal that sinks six floors below ground. It houses two theatres, the 450-seat Lewis A Swyer Theatre and the larger 982-seat Kitty Carlisle Hart Theatre.
The name, The Egg, implies a delicacy that structure does not possess and it can be thought of equally as a sculpture or a building. It sits beside a reflecting pool, and from a distance, the building seems to float above the earth like a grey flying saucer. The building is slightly inclined, and it does, well to me anyway, look like it is about to take off and head towards space where it belongs.
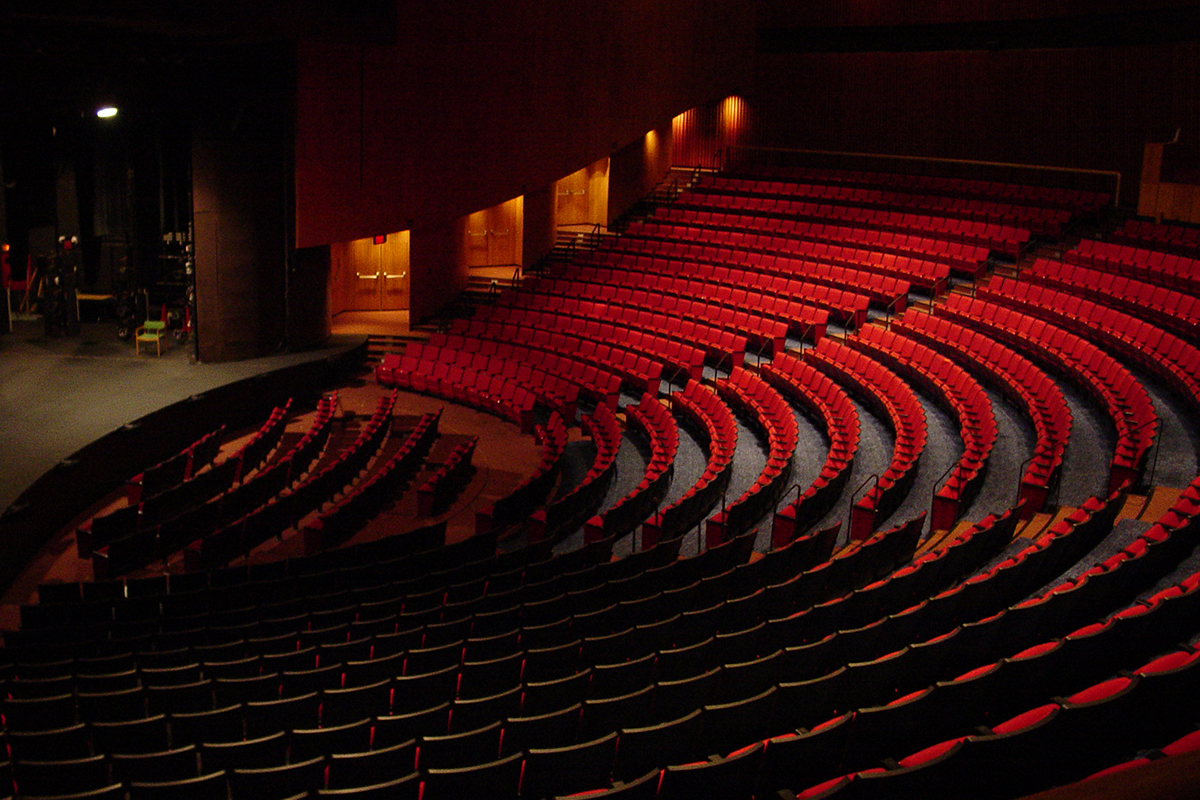
The larger theatre in The Egg, Albany, USA. To reflect the external architecture, the interior design of the building is based on curved lines and soft edges.
Photograph by Bob Keefer
The exterior design of the theatre heavily influences the interior of the building. The external shape does not contain many right angles other than in doorways and inside there are no corners and very few vertical walls. All the structural walls curve towards the concave ceiling.
Both theatres host a wide variety of productions from musical theatre, dance and music concerts to cabaret, lectures and multimedia presentations. Wrapped around the larger Hart Theatre is a lounge area that is used for functions such as seminars and after theatre parties.