Key data
Architects: Cox Architecture with Architects 61
Location: Queen Elizabeth Walk, Esplanade Mall, Singapore
Consultant Team: Arup, Tierra Design, Landscape consultant, Davis Langdon
Cost At Completion Of Construction was SGD$82.900.000 (66,320,000 Million USD)
Construction By Sato Kogyo Pte Ltd
Project Completed 2010.
The Design Concept
The Helix bridge is a beautiful, lightweight stainless steel structure and is said to be the world’s first double helix curved bridge, whatever that means. The design was the winner in an international design completion held in 2006 and it beat 36 other designs.
A double helix is defined as ‘A pair of parallel helices intertwined about a common axis.’ The image in your mind should be the Watson and Crick’s 1953 sketch of DNA , that is a double helix.
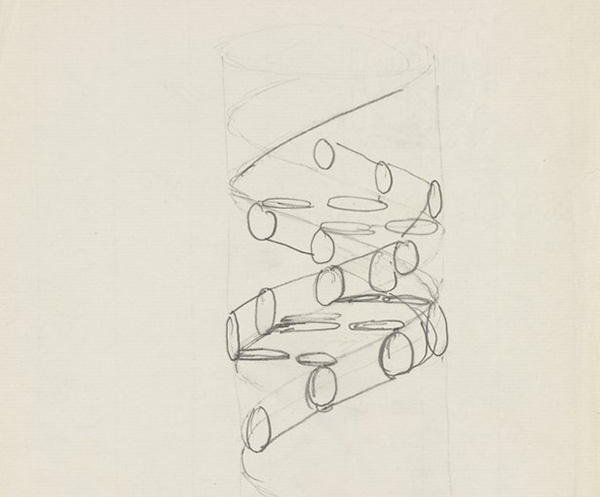
Watson and Crick’s sketch of DNA, 1953, showing a double helix
The gently curving bridge links Marina Bay to the Marina Centre and is solely for pedestrians to use. The stainless steel structure is 280 metres long and weighs 650 tons. The bridge is actually sited above the Singapore River, rather than the sea. On an aside the bridge curves to the left, natural DNA curves to the right.
The design and the design process
The double helix walkway is an extremely complicated structure and had to be engineered and fabricated with very high degree of accuracy. The stainless steel bridge was designed by a consortium, including the Australian Architectural Practice, Cox and the engineering was designed by Arup. From Singapore the spectacularly talented Architects 61 were included in the architectural team as they had actually produced the original architectural design. The company also developed the Botanical Gardens, that structure makes it onto the list of the top ten attractions to visit in Singapore.
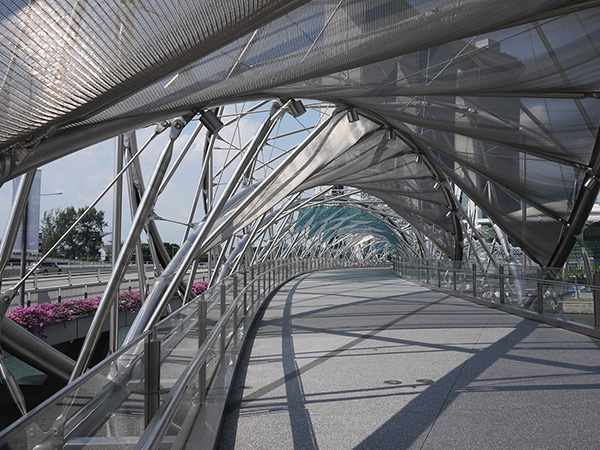
A pedestrian’s view of The Helix Bridge, photograph from The International Molybdenum Association and by Nicole Kinsman
I visited the bridge with my family in 2013. We walked over the bridge and took photos from the viewing platform along its length. The bridge is light and airy, no wobbling.
You get a killer view of the Marina Bay Sand casino and adjacent area. I mention this as Double Stone Steel supplied stainless steel for the casino project.
The Helix bridge is almost lost in the huge amounts of iconic landmarks in Singapore. The bridge unbelievably, does not feature on any top 10 sites to visit in Singapore. It is just a beautifully constructed, beautifully functional piece of engineering. It gets you from A to B with spectacular views on the way.
I come from a construction background, very high-end interior projects all over the world to be exact. Part of the construction process for a hotel project, is mock-ups. Mock-ups for all the furniture and mock-ups for all the room types, so not mood boards or looking at a couple of tiles. We would make full sized room simulations of how the room would actually be seen by the end users. Models can be a nightmare, all the designers, architects, owners and finally the hotel management have to sign them off.
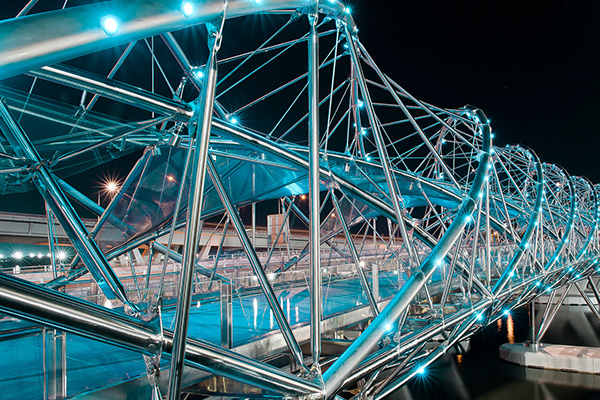
The Helix Bridge at night, illuminated through the work of Technolite lighting designers. Photograph by Technolite
On the Helix Bridge project the engineers took mock-ups to another level by mocking up the entire bridge in mild steel. The whole bridge, not sections or joints or flanges, the whole structure was mocked up in the factory and then on the finished bridge every element was also fully assembled before being sent to the construction site. The mock-up alone took one year to complete. This complex process eliminated many potentially costly mistakes in the fabrication process.
The bridge was constructed out of grade 2205 Duplex Stainless steel. This grade of stainless steel was used for its combination of tensile (means you can pull or stretch it) strength. The 2205 stainless steel is also very good at resisting fatigue and corrodes evenly.
There are canopies within the inner spiral fabricated from fritted glass and perforated steel mesh. These are positioned to create shade for passers-through. On the exterior of the structure are illuminated letters c, g, a and t which represent the four bases of DNA (cytosine, guanine, adenine, thymine).
Which brings us back to the first point made in the article!